今日は雨が降らないはずでしたが昨日と全く逆に何と雪が降ってきました。
降水確率は20%だったのにね・・・おかげでブルーベリーの作業が進みません・・・
まあ他にも月末なので支払いとかお見舞いとか雑務がたっぷりと有りました・・・おまけにCafeのK子さんが風邪をひいてしまったので厨房係まで回ってきました。だから結構忙しいのだ!(笑)
その上に今日はギャラリーの展示物の入れ替え日でして作品等は展示をされていた方がお持ち帰りになりますがパネルや机などの重量物の片付けは私の仕事なんですね・・・展示をされていた方が女性の方なのでこれを運ぶのはちょっと無理ですから。
そして明日はまた新たな展示が始まります、明日の展示に合わせてパネルの配置換えなどもしています。
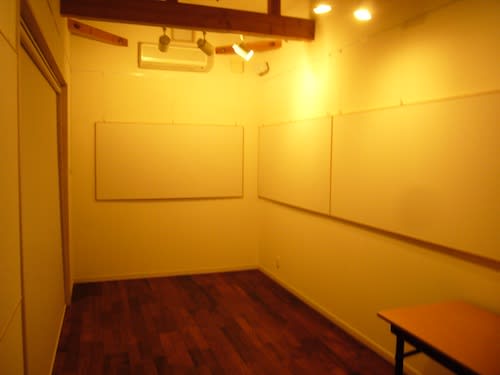
それからやっと製作を始めました。
今日はスピナーの製作でしたね。
このスピナーは前作のトロップフェンワーゲンから旋盤に寄る自作の物になりました。
今まではエッチング板や既製品を使っていましたが一度自作のパーツが出来る様になりますとエッチングを貼るだけでは満足いかなくなるのも事実ですね・・・困った物です。
まず最初は・・・削っています。
何を削っているのか?

そうなんです、端面の仕上げをしておきます。
この作業は実は大切な作業でして端面を整える為に突っ切りバイトで切りそろえるのですが、その刃物の特性から端面の中央に出っ張りが残ってしまったり致します。
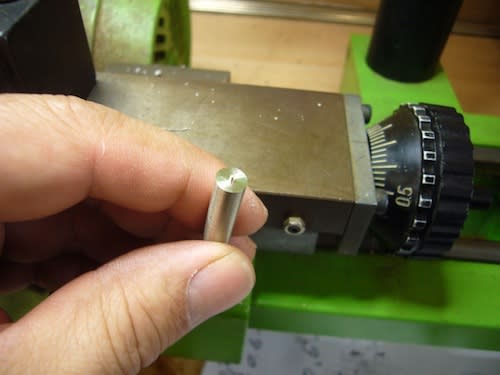
この出っ張りは後で修正しようとしますとペーパーかヤスリで削る訳なのですが寸法が変わってしまう恐れが有りますからこの時点で端面を削っておくのです。
切削用のバイトで端面を仕上げますとこんな感じになります・・・奇麗でしょ?
ついでにきちんと90°も出ますしね。
ちょっと注意が必要なのは使い回しの丸棒を使いますとセンタードリルの凹みが残っている事も有ります後では盛れません(ハンダを盛りますと色が違ってきますので磨きで仕上げられなくなります)ので注意をして確認をしておかないといけませんね~。
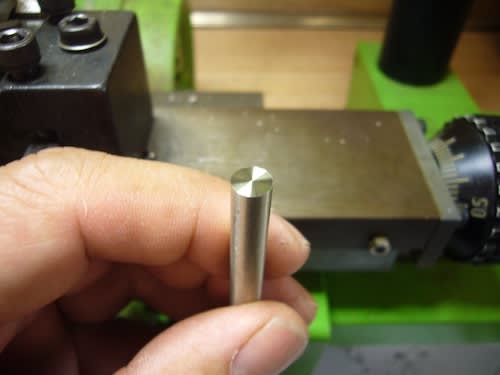
外径を削っておきます。
今回はウイングローブ氏の図面から計算しますとスピナーの爪の外径は4.8mmになります。
確認の意味でCMCのミニカーで寸法を当たってから計算してみますとやはり4.8mm(四捨五入しています)で良い様ですね。
と言う事でこの洋白の丸棒は6.0mm有りますから4.8mmまで落としておきます。
今回は12本の洋白の丸棒の両端で一緒に加工していますから24個のスピナーが出来ますね。
必要なのは20個で良いはずなので4つだけ予備が出来る訳ですね・・・。
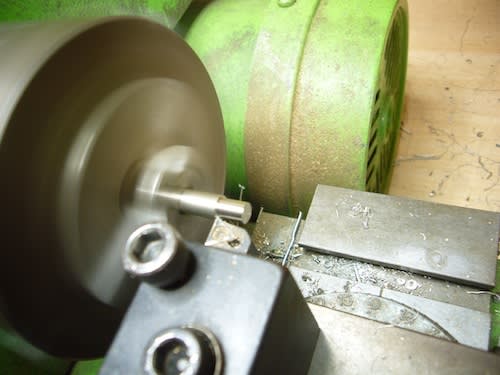
ここまでは事前の準備ですよ、いよいよスピナーを作ります。
最初に作るのはスピナーの中央の膨らんだ部分ですね。
ここは0.3mmの高さで直径は1.8mmの予定です。
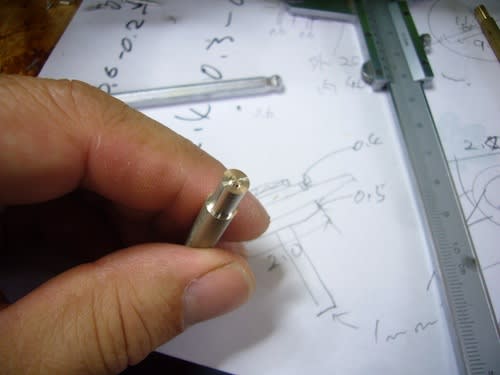
次はスピナーの爪の部分になる様に幅1.0mmの突っ切りバイトで1.4mm削り込みますと残った中央部分は2.0mmの直径になりますね。
爪の厚みは0.3mmになっています。
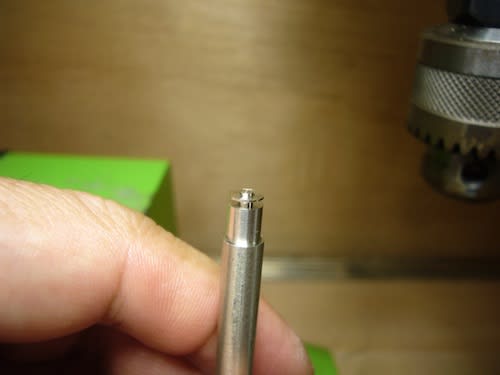
フライス盤で爪の不要な部分を削っておきます。
いつもの様に私の割り出し円テーブルは40回転で1周しますので1.5mmのエンドミルで12回転分回しながら削りまして上側にエンドミルを逃がしておいてから8回転ハンドルを回しエンドミルを下に動かして12回転分削りますと・・・こんな感じになります。
まあ割り出し円テーブルの使い方がおわかりにならない方はちょっと理解不能かもしれませんが・・・一応説明をしておかなければならない!?ので(笑)
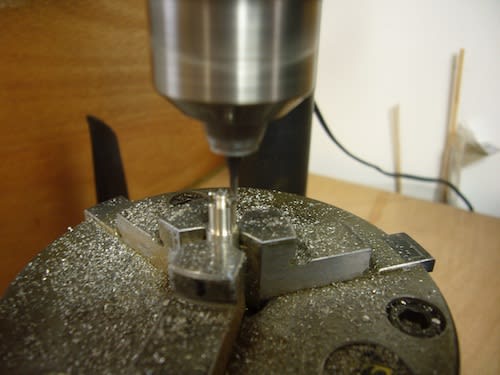
削り出した物は・・・ヤスリで更に削りまして・・・試作品ですがもう立派に爪が付いているのがわかりますでしょうか?
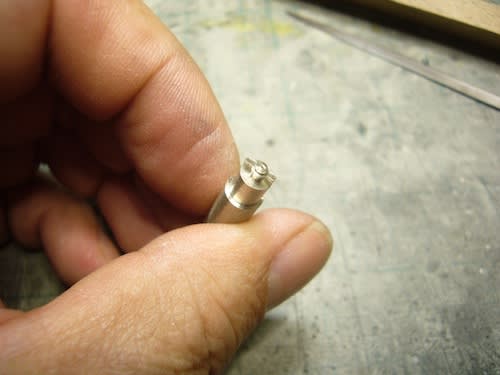
次にホイールに差し込む為の0.9mmのピンを削り出しております。
3mmも有れば良いのかな??
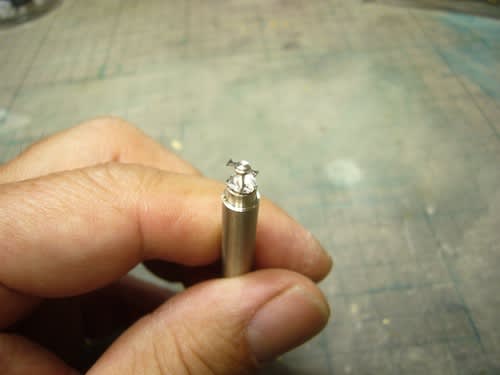
この部分を削る専用のバイトは持っていないのですが幅1.0mmの突っ切りバイトで3回ずらして削ればこんな物は簡単に出来ますね。
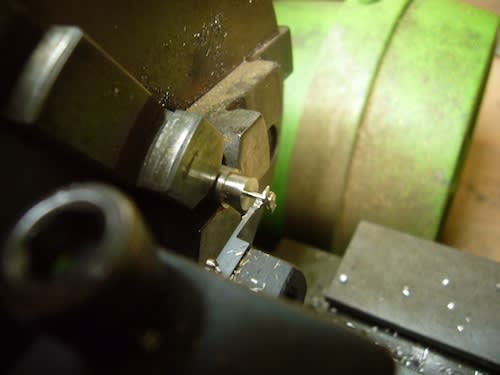
全てのスピナーの加工が終わりました。
後はヤスリで削るだけですね・・・
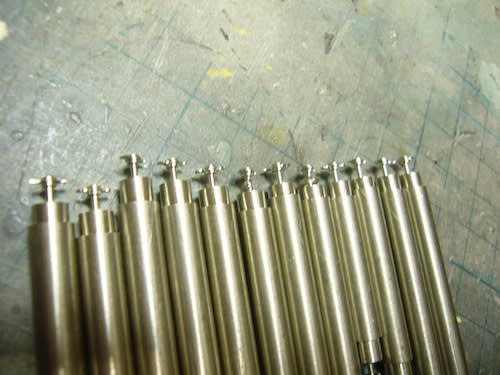
ヤスリの作業は目の疲れていない明日の午前中が良いのかな・・・と言う事で今日の作業は終了ですね。
降水確率は20%だったのにね・・・おかげでブルーベリーの作業が進みません・・・
まあ他にも月末なので支払いとかお見舞いとか雑務がたっぷりと有りました・・・おまけにCafeのK子さんが風邪をひいてしまったので厨房係まで回ってきました。だから結構忙しいのだ!(笑)
その上に今日はギャラリーの展示物の入れ替え日でして作品等は展示をされていた方がお持ち帰りになりますがパネルや机などの重量物の片付けは私の仕事なんですね・・・展示をされていた方が女性の方なのでこれを運ぶのはちょっと無理ですから。
そして明日はまた新たな展示が始まります、明日の展示に合わせてパネルの配置換えなどもしています。
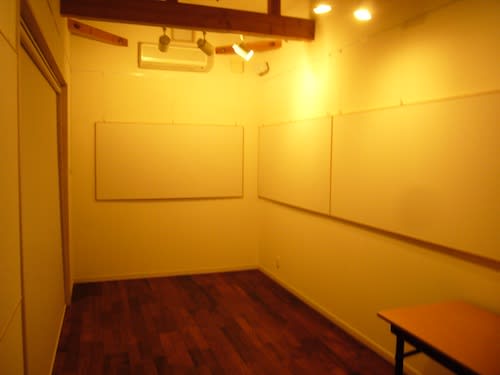
それからやっと製作を始めました。
今日はスピナーの製作でしたね。
このスピナーは前作のトロップフェンワーゲンから旋盤に寄る自作の物になりました。
今まではエッチング板や既製品を使っていましたが一度自作のパーツが出来る様になりますとエッチングを貼るだけでは満足いかなくなるのも事実ですね・・・困った物です。
まず最初は・・・削っています。
何を削っているのか?

そうなんです、端面の仕上げをしておきます。
この作業は実は大切な作業でして端面を整える為に突っ切りバイトで切りそろえるのですが、その刃物の特性から端面の中央に出っ張りが残ってしまったり致します。
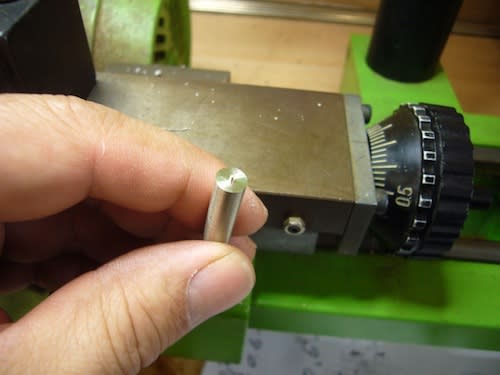
この出っ張りは後で修正しようとしますとペーパーかヤスリで削る訳なのですが寸法が変わってしまう恐れが有りますからこの時点で端面を削っておくのです。
切削用のバイトで端面を仕上げますとこんな感じになります・・・奇麗でしょ?
ついでにきちんと90°も出ますしね。
ちょっと注意が必要なのは使い回しの丸棒を使いますとセンタードリルの凹みが残っている事も有ります後では盛れません(ハンダを盛りますと色が違ってきますので磨きで仕上げられなくなります)ので注意をして確認をしておかないといけませんね~。
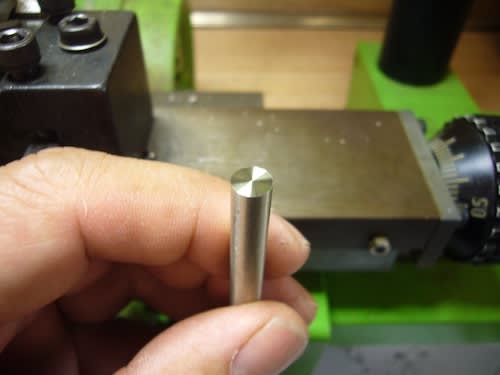
外径を削っておきます。
今回はウイングローブ氏の図面から計算しますとスピナーの爪の外径は4.8mmになります。
確認の意味でCMCのミニカーで寸法を当たってから計算してみますとやはり4.8mm(四捨五入しています)で良い様ですね。
と言う事でこの洋白の丸棒は6.0mm有りますから4.8mmまで落としておきます。
今回は12本の洋白の丸棒の両端で一緒に加工していますから24個のスピナーが出来ますね。
必要なのは20個で良いはずなので4つだけ予備が出来る訳ですね・・・。
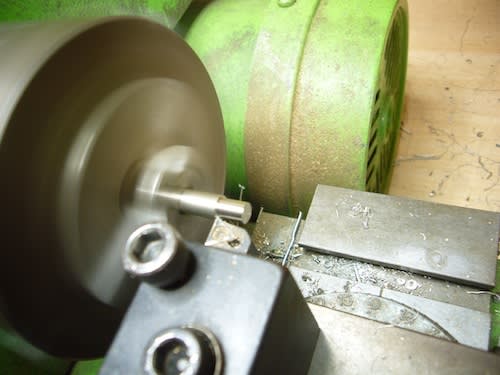
ここまでは事前の準備ですよ、いよいよスピナーを作ります。
最初に作るのはスピナーの中央の膨らんだ部分ですね。
ここは0.3mmの高さで直径は1.8mmの予定です。
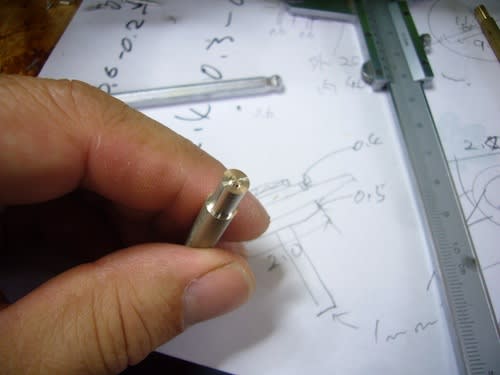
次はスピナーの爪の部分になる様に幅1.0mmの突っ切りバイトで1.4mm削り込みますと残った中央部分は2.0mmの直径になりますね。
爪の厚みは0.3mmになっています。
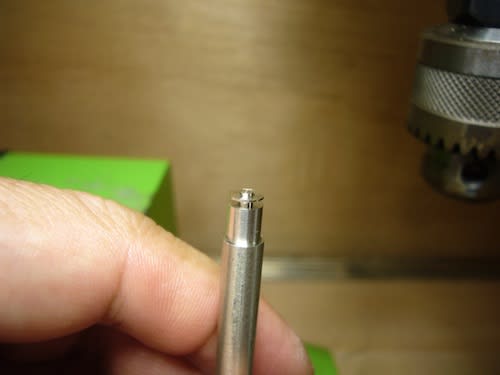
フライス盤で爪の不要な部分を削っておきます。
いつもの様に私の割り出し円テーブルは40回転で1周しますので1.5mmのエンドミルで12回転分回しながら削りまして上側にエンドミルを逃がしておいてから8回転ハンドルを回しエンドミルを下に動かして12回転分削りますと・・・こんな感じになります。
まあ割り出し円テーブルの使い方がおわかりにならない方はちょっと理解不能かもしれませんが・・・一応説明をしておかなければならない!?ので(笑)
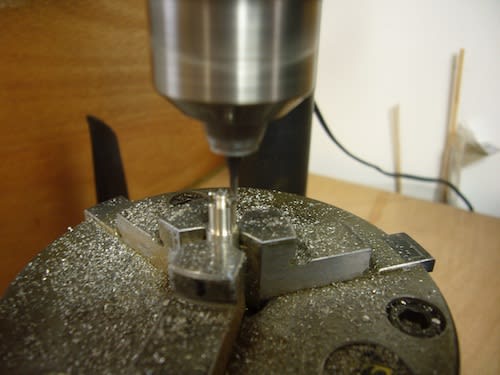
削り出した物は・・・ヤスリで更に削りまして・・・試作品ですがもう立派に爪が付いているのがわかりますでしょうか?
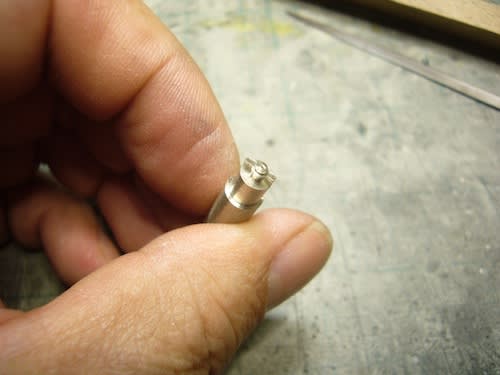
次にホイールに差し込む為の0.9mmのピンを削り出しております。
3mmも有れば良いのかな??
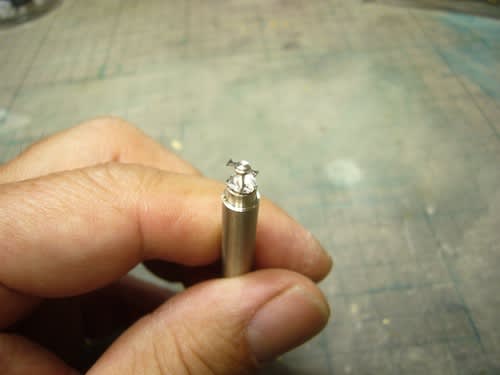
この部分を削る専用のバイトは持っていないのですが幅1.0mmの突っ切りバイトで3回ずらして削ればこんな物は簡単に出来ますね。
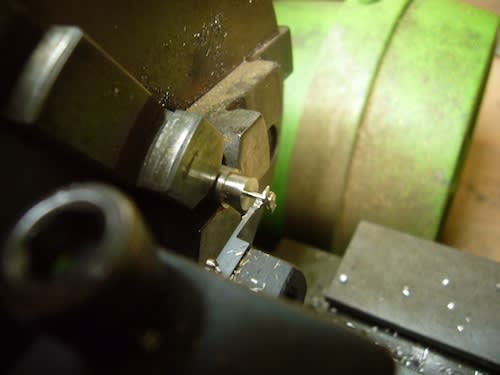
全てのスピナーの加工が終わりました。
後はヤスリで削るだけですね・・・
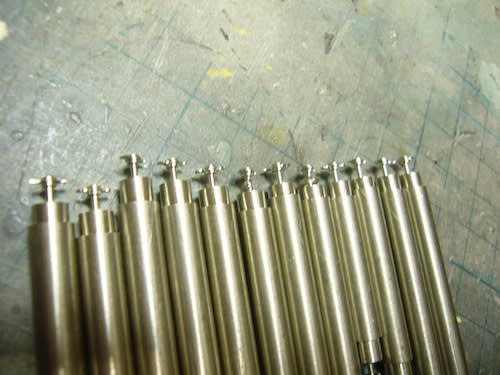
ヤスリの作業は目の疲れていない明日の午前中が良いのかな・・・と言う事で今日の作業は終了ですね。