板材加工の紹介
まず、自然乾燥(数ヶ月から数年)してある材料置き場から材を引っぱり出す。
ある材の中で、できるだけ適材適所を心がけて選定。
仕上がり寸法より、プラス数センチ足した寸法でカット、
もしくは、機械のカンナに通すのに、程よい寸法でカットし、
最初のカンナがけを行い、数日ほど自然乾燥。
乾燥後、よく見てみると、やや反りが出ているものがあります ↓

再びカンナがけ。
最初に、手押しカンナ ↓
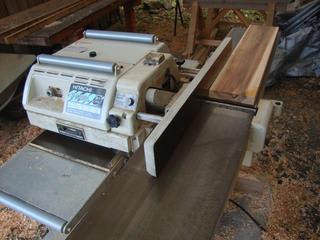
凹面を下にして、写真奥から手前に、手で押しながら回転刃の上を通す。
板材の持ち方に注意しないと、指がはみ出ていたら引っ掛けてしまう。
この手押しカンナがけは念入りに、確実に。
最初の平面を決めることになります。
一面の基準が出たら、その裏面を自動カンナへ通します ↓

材を機械へ入れると、上部についているローラーで、写真手前から奥へと送られていきます。
手で押し込んでいく必要はありません。自動カンナといわれる所以でしょう。
裏面と言いましても、自動カンナの刃物は、手押しと違って上部についておりますので、
手押しを通した材は、そのままの方向、同一面で、自動カンナの口に入れることになります。
木表、木裏の木目によって、削る方向が決まっています。
上手くできていますね。
自動カンナを通した材は、表裏の二面が均一になります。
つまり、25mmに設定したならば、25mmの厚みの材を作ることが出来ます。
そして、再び手押しカンナ ↓

三面目の加工 = 二面に対して直角を出します。
続いて、板幅を揃えるために昇降盤(テーブル丸ノコ)を通します ↓

この機械も刃物がむき出しですので要注意です。
カットした四面目のノコ刃の痕を消すためと、均一に面を出すために自動カンナへ。
一枚では不安定ですので、2枚以上を合わせて ↓

この方法はちょっと強引で、正確な直角が出ないこともあるので、
必ず直方体を出さなければいけない場合は、手押しカンナを通して仕上げます。
ピシッと揃いました ↓

次回は、今回加工した材を使って、本実加工を紹介する予定です。