なかなか冬らしくならない12月の屋久島です。
今日も日中は強い日差しでした。
前回、木取りした材を再び製材します。
まずはバンドソーで大まかに厚みを揃えます ↓

200ボルト仕様なので、そこそこパワーあります ↓
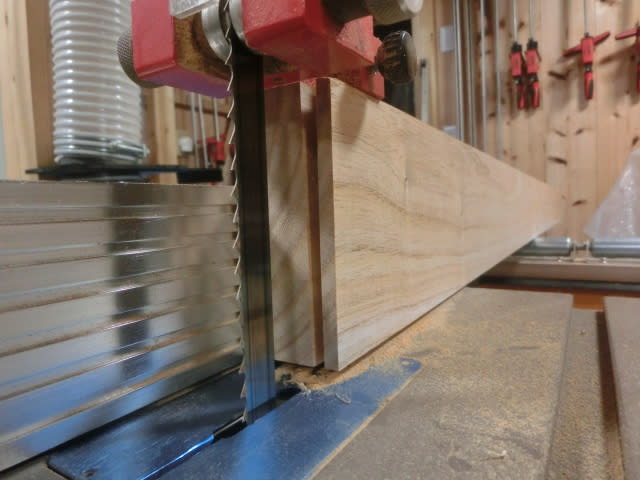
自動カンナできっちりと厚みを揃えました ↓
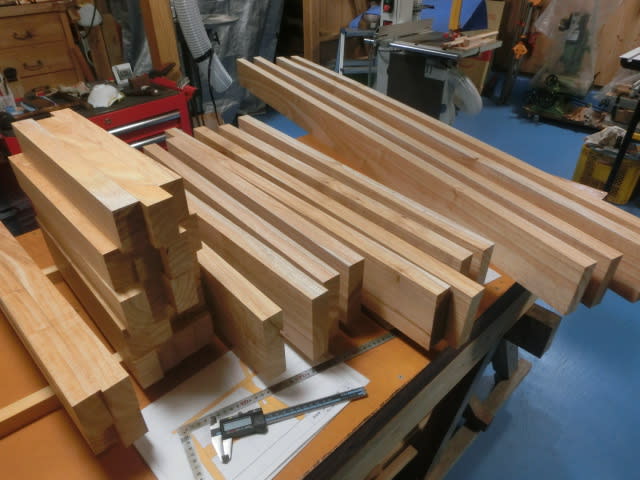
これで2台分のソファの背もたれ部分の材です。
その後、ドラムサンダーで研磨。
途中に、水引といって、濡れたタオルで材を湿らせる工程を加えます。
自動カンナやドラムサンダーなど、材に圧力を加えながら加工する機械を通すと、
その時に木材の繊維が押しつぶされいることになります。
その材を湿度の高いところへ置くと、木材が湿気を吸い込み、潰れていた繊維が元に戻ろうとして膨らみます。
一生懸命に磨いて、木材の表面を綺麗にしたはずなのにガサガサになってしまった経験からです。
特に、現在加工しているセンダンの木は要注意のなのです。
水引の後に再びドラムサンダーを通して表面を均一に研磨。
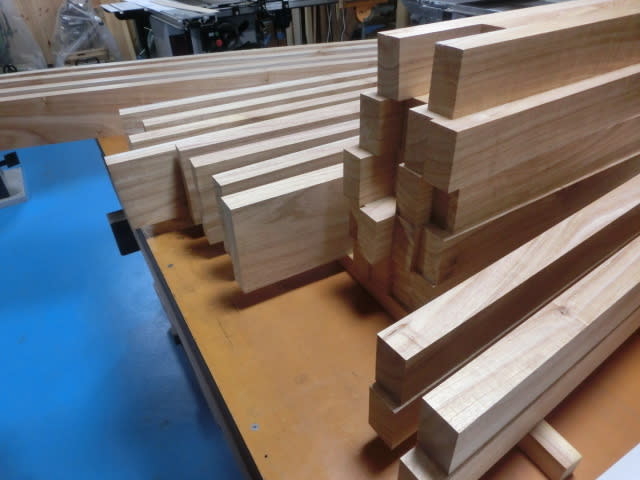
これで材は大人しくなりました。
十分に乾燥させてあるので、少々のことでは材は狂わないでしょう。
こちらは型作りの原図で、A4用紙を3枚繋げています ↓

パソコンのCADでR3000のラインをプリントアウトしました。
R3000とは、半径3m、つまり直径にすると6mの円。
その円弧となります。
べニア板に円弧を描き写してカット ↓

後日、ソファの部材加工に型として使います。
今日も日中は強い日差しでした。
前回、木取りした材を再び製材します。
まずはバンドソーで大まかに厚みを揃えます ↓

200ボルト仕様なので、そこそこパワーあります ↓
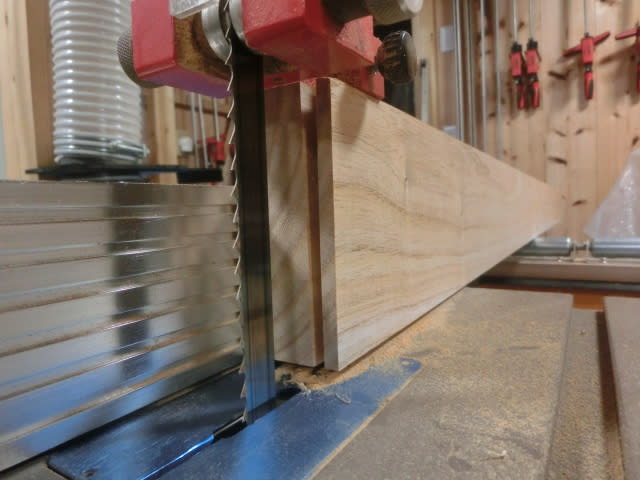
自動カンナできっちりと厚みを揃えました ↓
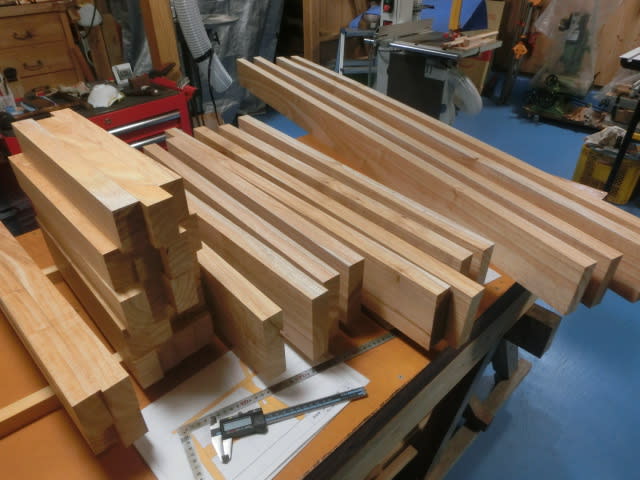
これで2台分のソファの背もたれ部分の材です。
その後、ドラムサンダーで研磨。
途中に、水引といって、濡れたタオルで材を湿らせる工程を加えます。
自動カンナやドラムサンダーなど、材に圧力を加えながら加工する機械を通すと、
その時に木材の繊維が押しつぶされいることになります。
その材を湿度の高いところへ置くと、木材が湿気を吸い込み、潰れていた繊維が元に戻ろうとして膨らみます。
一生懸命に磨いて、木材の表面を綺麗にしたはずなのにガサガサになってしまった経験からです。
特に、現在加工しているセンダンの木は要注意のなのです。
水引の後に再びドラムサンダーを通して表面を均一に研磨。
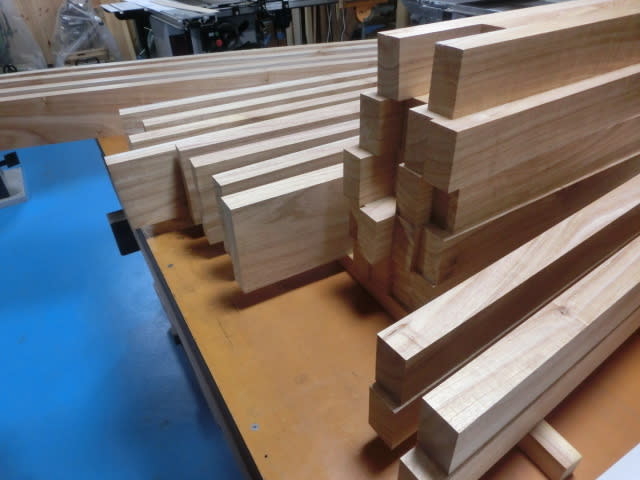
これで材は大人しくなりました。
十分に乾燥させてあるので、少々のことでは材は狂わないでしょう。
こちらは型作りの原図で、A4用紙を3枚繋げています ↓

パソコンのCADでR3000のラインをプリントアウトしました。
R3000とは、半径3m、つまり直径にすると6mの円。
その円弧となります。
べニア板に円弧を描き写してカット ↓

後日、ソファの部材加工に型として使います。