中子が必要数できていないが、原型の仕上げができてきたので、こちらを先行する
原型

方針を変更、中子は胴体部分にだけ使用して、肢部品はその1と同じ方法で型取りします

型に負荷がかかりますが、前回実績があり、型抜き数が少ないので問題ないでしょう、どれくらい型がもつかが問題です
頭部
中子を取付けた状態


油土に埋める

鉛筆削りで5mmプラ丸棒の先端を削り、注型用ランナーにする

鉛筆削り

5mmプラ丸棒を注型用ランナーに、1mm真鍮線で空気抜きの穴を作る、ランナーに近づき過ぎないように、曲げる

2分割型では成型品が取り出せないので、3分割型にする
型分割の壁をもう1箇所作る、最初の油土とくっつかないように、PVA(ポリビニールアルコール)を油土に塗る

PVA(ポリビニールアルコール)
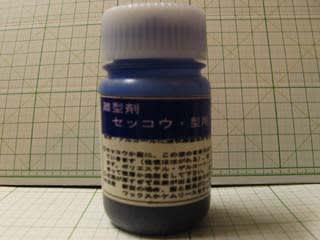
PVAが乾いたら、壁にする油土を盛り付ける

腹部
中子を取付けた状態で油土に埋め、頭部と同様に注型用ランナー、空気抜きの穴を作る
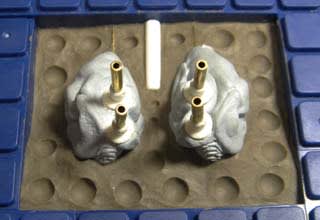
胸部
中子を取付けた状態で油土に埋める、頭部、腹部の取り付け穴は3mm真鍮線を差込んでおく
頭部と同様に注型用ランナー、空気抜きの穴を作る

肢(先端側)
アンダーゲート法でまとめて型取りする
頭部と同様に注型用ランナー、空気抜きの穴を作る

取付穴成型用ピンは切出す作業時間がないので3mプラ丸棒で代用する、注型開始までには真鍮丸棒を切り出しておく
肢(胴体側)
肢(先端側)と同様に、アンダーゲート法でまとめて型取りする
頭部と同様に注型用ランナー、空気抜きの穴を作る

取付穴成型用ピンは切出す作業時間がないので3mプラ丸棒で代用する、注型開始までには真鍮丸棒を切り出しておく
肢(先端側)の取付部のピンが油土に埋め込まれていないことに注目

肢(最前部)
その1で、先端までキャストが流れない失敗が多かったので、注型失敗に備え他とは別で型を作る

空気抜き穴をなるべく少なくするためこういう配置にした
型取り準備完了
ここまで11 hours
この後シリコーンゴムを流しますが、その前に必要量を計算します
必要量=体積×シリコーンゴムの比重
体積=型枠の底面積×型枠の深さ-成型品体積
この数値の中で不確定要素が多いのが型枠の深さと成型品体積
量が不足すると問題が発生するので、多めに見積もっておきます、そのため成型品体積は無視することにして、型枠の深さはだいたいで計算する
今回の必要量は2.2kg
在庫分では不足するので買い足しに行きましたが、本日の営業時間は21時まででした、「しまった」とか思いましたが、後の祭り、仕方ないので在庫分だけで進めます
3分割になるここを真っ先に進めます

ここまで1hours
今回ここまで
今回の作業時間 合計12hours
次回を読む
ワンフェス出展のお手伝い2012年夏その3 キャストキット生産 第5回(型取り2)
前回を読む
ワンフェス出展のお手伝い2012年夏その3 キャストキット生産 第3回(中子の製作3)
1回から読む
ワンフェス出展のお手伝い2012年夏その3 キャストキット生産 第1回(中子の製作1)
シリコーンゴム型取り関連の記事
ブログ記事一覧 「ワンフェス出店のお手伝い2012夏その1」 編
ブログ記事一覧 「ワンフェス出店のお手伝い 河童ガレージキット生産」編
シリコーンゴムによる型取り(流木を型取りする 1回)
ブログ記事一覧 「手首をなんとかする」編
原型

方針を変更、中子は胴体部分にだけ使用して、肢部品はその1と同じ方法で型取りします

型に負荷がかかりますが、前回実績があり、型抜き数が少ないので問題ないでしょう、どれくらい型がもつかが問題です
頭部
中子を取付けた状態


油土に埋める

鉛筆削りで5mmプラ丸棒の先端を削り、注型用ランナーにする

鉛筆削り

5mmプラ丸棒を注型用ランナーに、1mm真鍮線で空気抜きの穴を作る、ランナーに近づき過ぎないように、曲げる

2分割型では成型品が取り出せないので、3分割型にする
型分割の壁をもう1箇所作る、最初の油土とくっつかないように、PVA(ポリビニールアルコール)を油土に塗る

PVA(ポリビニールアルコール)
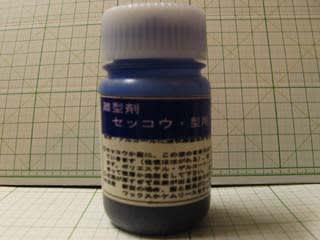
PVAが乾いたら、壁にする油土を盛り付ける

腹部
中子を取付けた状態で油土に埋め、頭部と同様に注型用ランナー、空気抜きの穴を作る
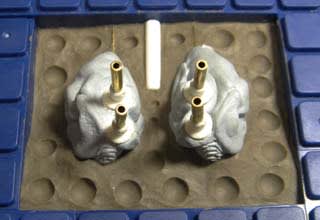
胸部
中子を取付けた状態で油土に埋める、頭部、腹部の取り付け穴は3mm真鍮線を差込んでおく
頭部と同様に注型用ランナー、空気抜きの穴を作る

肢(先端側)
アンダーゲート法でまとめて型取りする
頭部と同様に注型用ランナー、空気抜きの穴を作る

取付穴成型用ピンは切出す作業時間がないので3mプラ丸棒で代用する、注型開始までには真鍮丸棒を切り出しておく
肢(胴体側)
肢(先端側)と同様に、アンダーゲート法でまとめて型取りする
頭部と同様に注型用ランナー、空気抜きの穴を作る

取付穴成型用ピンは切出す作業時間がないので3mプラ丸棒で代用する、注型開始までには真鍮丸棒を切り出しておく
肢(先端側)の取付部のピンが油土に埋め込まれていないことに注目

肢(最前部)
その1で、先端までキャストが流れない失敗が多かったので、注型失敗に備え他とは別で型を作る

空気抜き穴をなるべく少なくするためこういう配置にした
型取り準備完了
ここまで11 hours
この後シリコーンゴムを流しますが、その前に必要量を計算します
必要量=体積×シリコーンゴムの比重
体積=型枠の底面積×型枠の深さ-成型品体積
この数値の中で不確定要素が多いのが型枠の深さと成型品体積
量が不足すると問題が発生するので、多めに見積もっておきます、そのため成型品体積は無視することにして、型枠の深さはだいたいで計算する
今回の必要量は2.2kg
在庫分では不足するので買い足しに行きましたが、本日の営業時間は21時まででした、「しまった」とか思いましたが、後の祭り、仕方ないので在庫分だけで進めます
3分割になるここを真っ先に進めます

ここまで1hours
今回ここまで
今回の作業時間 合計12hours
次回を読む
ワンフェス出展のお手伝い2012年夏その3 キャストキット生産 第5回(型取り2)
前回を読む
ワンフェス出展のお手伝い2012年夏その3 キャストキット生産 第3回(中子の製作3)
1回から読む
ワンフェス出展のお手伝い2012年夏その3 キャストキット生産 第1回(中子の製作1)
シリコーンゴム型取り関連の記事
ブログ記事一覧 「ワンフェス出店のお手伝い2012夏その1」 編
ブログ記事一覧 「ワンフェス出店のお手伝い 河童ガレージキット生産」編
シリコーンゴムによる型取り(流木を型取りする 1回)
ブログ記事一覧 「手首をなんとかする」編