31日(土)の作業、積層法による型取りの続き
いよいよ2011年も押し迫ってまいりました、年内完成できるのか、いよいよ時間が無い
FRP製のバックアップジャケットを作ります、手順は3回(型取り1)の後半をご参照下さい
チョップドストランドマットを切りだし、揉んでやわらかくする(グラスマット揉み)、このときガラス繊維が空中に飛散するため防塵マスク装着と換気を必ず行う
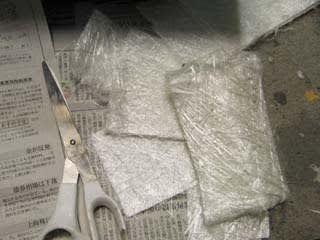
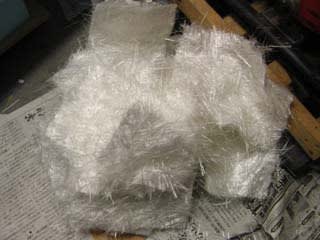
硬化剤を混合したゲルをシリコーンゴムに刷毛で塗る
表面にグラスマットの目が出ても問題ないので、グラスマットを即、貼りこむ
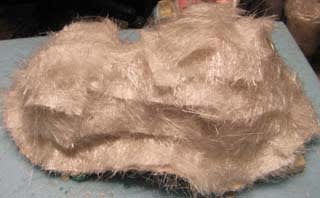
硬化剤を混合した生ポリを刷毛で押さえながら含浸させる
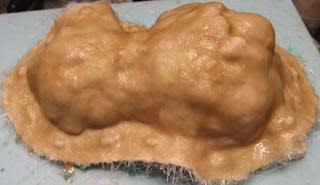
縁の強化のため、ポリ硬化前に縁にグラスマットを貼り重ねる
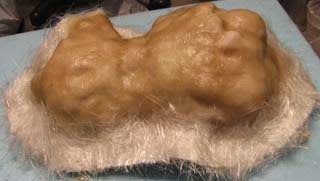
1回目の含浸に使った、生ポリの余りを使って含浸させる
硬化待ち
急いで硬化させるため、促進剤を混入した生ポリを更に上から塗る
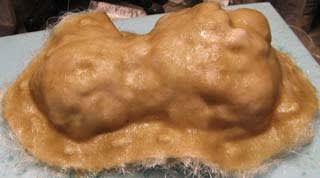
促進剤(ナフテン酸コバルト)
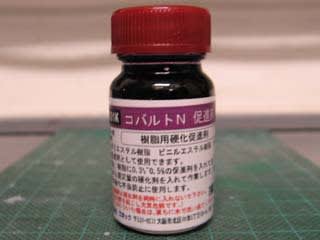
発火の危険があるため、取扱注意
使い方は、次回説明します
今回の作業時間 1.5hours(待ち時間なし)
次回を読む
大カッパを複製する 6回(型の仕上げ、FRP成型)
前回を読む
大カッパを複製する 4回(型取り2)
1回から読む
大カッパを複製する 1回(原型)
シリコーンゴム型取り関連の記事
ブログ記事一覧 「ワンフェス出店のお手伝い 河童ガレージキット生産」編
シリコーンゴムによる型取り(流木を型取りする 1回)
ブログ記事一覧 「手首をなんとかする」編
いよいよ2011年も押し迫ってまいりました、年内完成できるのか、いよいよ時間が無い
FRP製のバックアップジャケットを作ります、手順は3回(型取り1)の後半をご参照下さい
チョップドストランドマットを切りだし、揉んでやわらかくする(グラスマット揉み)、このときガラス繊維が空中に飛散するため防塵マスク装着と換気を必ず行う
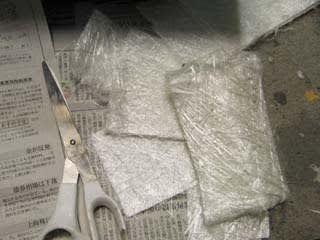
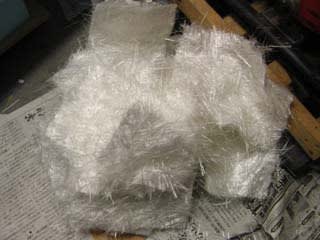
硬化剤を混合したゲルをシリコーンゴムに刷毛で塗る
表面にグラスマットの目が出ても問題ないので、グラスマットを即、貼りこむ
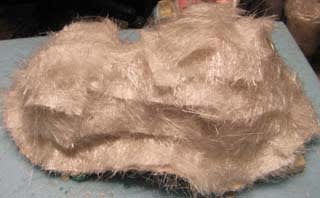
硬化剤を混合した生ポリを刷毛で押さえながら含浸させる
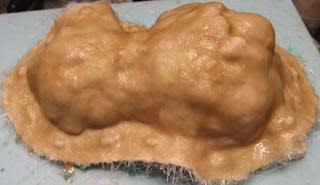
縁の強化のため、ポリ硬化前に縁にグラスマットを貼り重ねる
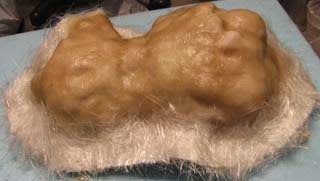
1回目の含浸に使った、生ポリの余りを使って含浸させる
硬化待ち
急いで硬化させるため、促進剤を混入した生ポリを更に上から塗る
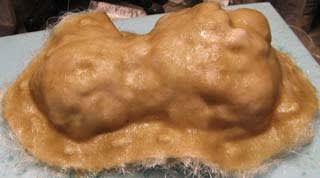
促進剤(ナフテン酸コバルト)
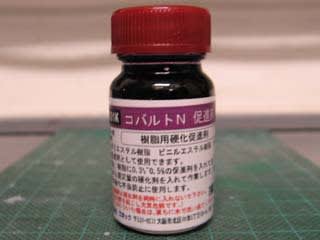
発火の危険があるため、取扱注意
使い方は、次回説明します
今回の作業時間 1.5hours(待ち時間なし)
次回を読む
大カッパを複製する 6回(型の仕上げ、FRP成型)
前回を読む
大カッパを複製する 4回(型取り2)
1回から読む
大カッパを複製する 1回(原型)
シリコーンゴム型取り関連の記事
ブログ記事一覧 「ワンフェス出店のお手伝い 河童ガレージキット生産」編
シリコーンゴムによる型取り(流木を型取りする 1回)
ブログ記事一覧 「手首をなんとかする」編