車両製造の過去と現在(2事例)
私事ながら、最近、私より10ほど年上の方だが、元日産の生産技術というか製品品質評価畑で活動した方と知り合え、今まで謎だった知見とかが解消される部分もありがたい巡り会いだと感じている。
私の物事の見方は、昔から何故だろうか、現代最新型でも昔と異なる作業手順と取るがその理由は何故だろうかと、その技術テクノロジーにも感心は持つが、それよりも量産手法とその理由と云うべきものに想像を巡らすことが多い。
そんな中の一部ではあるが、今回の新たな巡り会いにより、氷解したと思える事柄を以下の幾つか紹介してみたい。
1.モノコックボデーの初期に発生したという応力集中時の異音(ボデーきしみ音)
過去の損保調査員時代の10程先輩の他社知人(既に故人)とは、同じトヨタ系列のディーラー出身であり、相手はトヨタ販売チャネル最後発と云えるトヨタオート(現在ネッツだが近い将来その名も消えるだろう)創設の頃、この業界に入ったと云うところで、昔のディーラー話に花が咲くことも多かった。
そん中で聞いた、初代スプリンター(KE15 1968-1970初代カローラの姉妹車種で2ドアのスポーティ風モデル)は、既にモノコックボデー(フレームレス)を採用していたが、ボデープラットフォームやメカニカルコンポーネントとしては、初代カローラ(KE1# 1966-1970)にほぼ準じた車両だ。これ以前にトヨタでは、初代パブリカ(1961-1969)とかで、既にモノコックボデーは経験済であったが、当時の初代スプリンター(その他の車種でもあったろう)で、納車したばかりの新しい車両で、路面の段差を乗り越えたりという、云うなればボデーに曲げや捻れという応力を受けた際、「ギシッ」とかいう云うなればキシミ音が出るという不具合のことを聞いたことがあった。これは、その後10年程を経て、系列は異なれど同じくトヨタ系列ディーラーに関わることになった筆者には、当時の新車でも、ボデーがたわんだり剛性が低いなと思う局面はあれども、キシミ音までがでるということはなかったので、ちょっと驚いたものだった。

そこで、聞いたのは、それどうやって直すのと云うことだ。その答えは、異音が生じる付近のパネル合わせのスポット溶接部位にマイナスドライバーを打ち込んで、ある程度隙間をつくってやるという、何ともアラっぽい対処法だったことだった。
と云うことで、冒頭述べた元日産の製品品質管理担当に聞くと、日産の場合はブルーバード2台目(410 1963-1967)が最初のモノコックボデー車だったが、その音の出る原因は、ボデー組立ラインにおけるスポット溶接が未だロボット化されておらず、多くの工員が手操作で作業を行っていたことに原因はあるとのこおtだった。
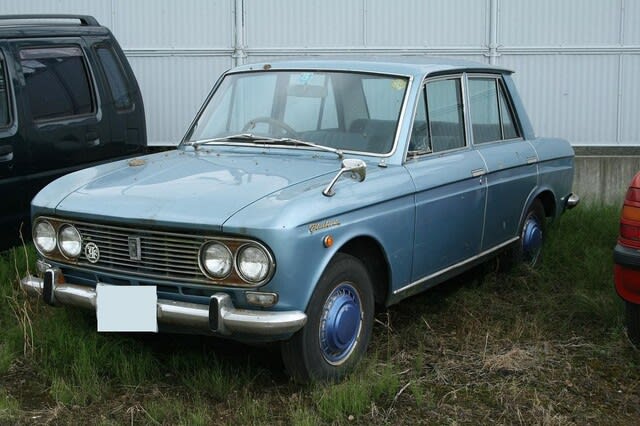
スポット溶接とは、2枚なり3枚程度までの鋼板を合わせ面を合わせ、そこを銅製の電極で上下を挟んで、加圧しつつ、大電流(鋼板で7千Aとかメーカー設置の装置の場合で補修用はその半減ほど)を流し、通電直線部の鋼と鋼が接触する部位がもっとも抵抗値が大きいのでここで発熱溶融しつつ、一定の保持時間を与えることで1点のスポット溶接は完了する。この溶接の利点は、溶接混として、ナゲットと呼ばれる円形の凹みは生じるが、トリミングとかウェザーストリップなどで隠れる部位が溶接箇所になることもあるが、溶接後にバリ取りサンダーリングやパテ埋め成形などの後処理が不要なことがある。ただし、1点当たりの溶接強度は十分とは云えず、特に点であるので、そこに捻りの応力が働くと弱いので、ある程度の間隔を開けて連続してスポット打点を繰り返す必用があるということだ。

ここである程度の間隔を開けてと記したのは、スポット打点と次のスポット打点が近すぎると、その旧スポット打点を通じて電流が流れる(これお無効分流と呼ぶ)現象が起き、あまり接近したスポット打点では、返って溶接強度を出すことができないという点に問題がある。このため、各スポット打点の間隔は20~25mm程度(強度負荷の低い部位ではもっと間隔が広い場合もあり)離して打設する様に作業者に指導していたのだった。しかし、人が手作業でやるスポット打設は、一々計測しながら打設する訳でもなく、打設間隔が長くなったり短くなったり、ある場合は省略して比較的長いスパンで打設が打ち漏らされたりという不具合が生じることが、今回のキシミ音の原因だと判ったとのことおだ。
その後、ボデー組立ラインはロボットによる自動化がなされ、新しい車両を量産開始する時点で、作業車がロボットにスポット打点位置を記憶させる作業(これおティーチングと呼んでいる)をするだけで、ロボットは疲れることも、忘れることもなく、寸分違わず同じ位置にスポットを繰り返すのだ。後年、損保調査員になってから知るが、同じ工場で作られた同型車種では、異なる固体の車種間でも、スポット打点は、寸分違わず一致するので、組み合わせ部品の合わせ作業において、このことを利用する場合もあることを知る。
なお、雑事ではあるが、ラリー車を作るなどとして、ロールゲージを室内に組むのも、ボデー剛性を高める意味もあるのだが、ボデー補強の一番として、スポットの増し打ちというものがあることを、この項のさごの話題として若干触れてみたい。
スポット増し打ちとは、先に述べた様にスポット溶接は無効分流という特性のため、あまり接近した打点では、本来溶接したいヶ所に十分な電流が流れず、従って発熱量も低く十分な溶接強度が出ないということだ。したがって、現状のスポット間隔の中央だとか、その間隔内を3分割して2点割増追加打点をスポット溶接機で行うことは不可能なのだ。この場合は、次の様な手法により、スポット打点11点と同等以上の溶接強度を得ている。
この手法は、俗にプラグ溶接と呼ばれる手法で、溶接部位のパネルが2枚合わせならその1枚に、3枚合わせならその2枚に、8Φ程度のスポット切り離し用の平面エンドミル歯先のドリルキリ(俗称スポットカッター)で残り1枚をなるべく痛めない様に穴開け加工する。そして、MIG溶接機(半自動と呼ばれる溶接ワイヤが自動供給される溶接機で、シールドガスに炭酸ガスかアルゴンとの混合ガス(アルタンと呼ぶ)を使用する溶接機)で、穴を塞ぐ様に溶接トーチを穴の外周をなぞる様に円を描いて動かす。あまり溶接電流が強かったり、トーチの動かし方が遅かったりすると、溶け込みすぎて裏板が溶け落ちて穴が空く、また溶接電流が弱いとか、トーチの動かしが遅すぎると、溶け込み不良で十分な溶接強度が出ない。溶接外観とか裏板の除隊を観察しつつ、適度な溶接電流(もしくは適度な溶接ワイヤー径もある)と適度なトーチの動かし速度を習得する必用がある。なお、このプラグ溶接は、溶接部表面はある程度半径に盛り上がるので、事後サンダーリングで擦り落とし、場合のよってはポリパテで仕上げる作業が追加となる。
2.日産アリアの樹脂バンパーをボデー(鋼板&アルミ板)と一緒に塗装ラインで塗り作業していることについて
これは当ブログ「日産アリアプロダクション 2021-11-14」でも記したことなのだが、従来の1液型熱硬化塗料は130-140℃で30分-40分の加温乾燥時間で完結するが、樹脂バンパーはブレンドは各車ある様だが、機材としてはPPが主成分のものだろう。これの熱変形に耐える許容温度は80℃程度と知見されるが、乾燥温度を140から80℃程度に低下させているのは間違いないだろうということを、件の人物に質問してみたところ、やはり乾燥温度の低下にあり、その要請はバンパーだけの問題ではなく、プラント内でもっともエネルギー消費(云うなればCO2対策の一環)の大きい部署として、塗装ラインがあり、これへの対策がバックグラウンドとしてあると云う説明だった。
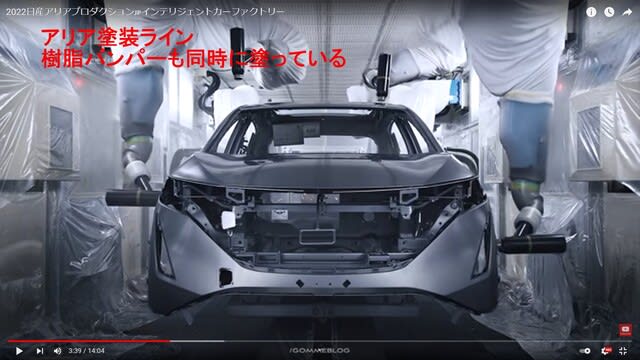
ここで使用の塗料は、関ぺ、日ペ、その他の熱硬化型塗料だが、その重合温度(架橋反応温度)を従来より低下させる特性のものにしているだろう。なお、バンパーなどの樹脂部品は、従来はボデーの熱硬化型とは別の部署で、2液ウレタン型塗料で別に施工しており、新車時から色味が一致しないとか、使用過程で退色が不整合で色味の差異が目立つなどの弊害があり、高級車などでは。色味を合わせた選択仕様までを行っていたのだが、これは製品歩留まりを向上させる意味でも大きな前進と云えるだろう。
ただし。これは筆者の知見から来る想像も交えるが、熱硬化温度を低下させた新塗料は、従来より塗料の製品出荷から可使期間が大幅に縮む可能性があると予見される。これは、重合型接着剤でも同様なのだが、熱とか硬化剤の混合による化学変化だが、元来そのその重合反応を停めるブロック剤因子が含まれており、そのブロックを解くために熱を上げたり硬化剤を混合したりする訳だが、期間と共に徐々にブロック剤の効果は薄れていくものなのだ。従って、熱重合温度を下げると云うことは、よりブロック剤の因子が臨界点に近づくことを暗示しており、たぶん塗料製造後の使用可能期間は大幅に圧縮されると思える。定かではないが、従来型の130℃1液熱硬化で3ヶ月程だと聞いているが、もしかすると環境温度によっては1ヶ月程になる場合すらありそうに想像する。
ついでに、このアリアもそうだが、下塗りはカチオンED(電着)で水性エポキシ熱硬化型で、デッピング後に1ベーク(加温)だが、その後、中塗り、カラーベース、トップコートクリアーと水性塗料をウェットオンウェット(未乾燥状態で塗り重ねる)で塗り、最後に1ベーク(加温)という3C1B(3コート1ベーク)が現代の超高級でない一般的な車両の標準となっていることは知っておきたい。
なお、アリアでは、塗膜表面のゴミ、ブツの異常の検出と、パネル表面の歪みの検査を、機械的センシングで行っている様子が判る。従来この様な検査は、直管式蛍光灯が多数並んだ部屋で、その映り込む蛍光灯の姿だとか明るい照度環境で、人が目視でなで回す様に角度を変え目視検査していたものだ。
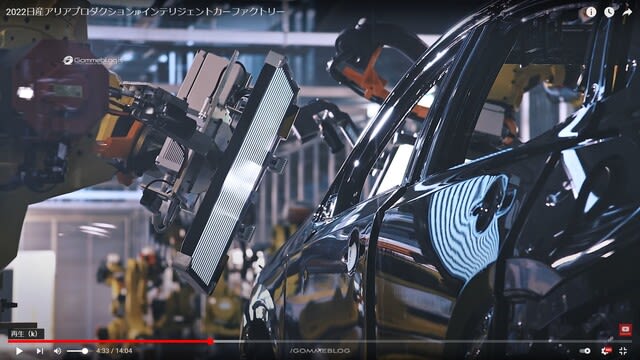
日産アリアプロダクション
2021-11-14 | 車と乗り物、販売・整備・板金・保険
https://blog.goo.ne.jp/wiseman410/e/8f0167c8cdf333fb111b670eafdbf45e
私事ながら、最近、私より10ほど年上の方だが、元日産の生産技術というか製品品質評価畑で活動した方と知り合え、今まで謎だった知見とかが解消される部分もありがたい巡り会いだと感じている。
私の物事の見方は、昔から何故だろうか、現代最新型でも昔と異なる作業手順と取るがその理由は何故だろうかと、その技術テクノロジーにも感心は持つが、それよりも量産手法とその理由と云うべきものに想像を巡らすことが多い。
そんな中の一部ではあるが、今回の新たな巡り会いにより、氷解したと思える事柄を以下の幾つか紹介してみたい。
1.モノコックボデーの初期に発生したという応力集中時の異音(ボデーきしみ音)
過去の損保調査員時代の10程先輩の他社知人(既に故人)とは、同じトヨタ系列のディーラー出身であり、相手はトヨタ販売チャネル最後発と云えるトヨタオート(現在ネッツだが近い将来その名も消えるだろう)創設の頃、この業界に入ったと云うところで、昔のディーラー話に花が咲くことも多かった。
そん中で聞いた、初代スプリンター(KE15 1968-1970初代カローラの姉妹車種で2ドアのスポーティ風モデル)は、既にモノコックボデー(フレームレス)を採用していたが、ボデープラットフォームやメカニカルコンポーネントとしては、初代カローラ(KE1# 1966-1970)にほぼ準じた車両だ。これ以前にトヨタでは、初代パブリカ(1961-1969)とかで、既にモノコックボデーは経験済であったが、当時の初代スプリンター(その他の車種でもあったろう)で、納車したばかりの新しい車両で、路面の段差を乗り越えたりという、云うなればボデーに曲げや捻れという応力を受けた際、「ギシッ」とかいう云うなればキシミ音が出るという不具合のことを聞いたことがあった。これは、その後10年程を経て、系列は異なれど同じくトヨタ系列ディーラーに関わることになった筆者には、当時の新車でも、ボデーがたわんだり剛性が低いなと思う局面はあれども、キシミ音までがでるということはなかったので、ちょっと驚いたものだった。

そこで、聞いたのは、それどうやって直すのと云うことだ。その答えは、異音が生じる付近のパネル合わせのスポット溶接部位にマイナスドライバーを打ち込んで、ある程度隙間をつくってやるという、何ともアラっぽい対処法だったことだった。
と云うことで、冒頭述べた元日産の製品品質管理担当に聞くと、日産の場合はブルーバード2台目(410 1963-1967)が最初のモノコックボデー車だったが、その音の出る原因は、ボデー組立ラインにおけるスポット溶接が未だロボット化されておらず、多くの工員が手操作で作業を行っていたことに原因はあるとのこおtだった。
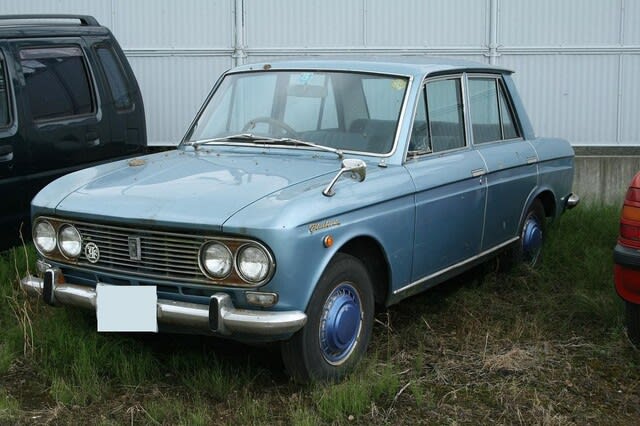
スポット溶接とは、2枚なり3枚程度までの鋼板を合わせ面を合わせ、そこを銅製の電極で上下を挟んで、加圧しつつ、大電流(鋼板で7千Aとかメーカー設置の装置の場合で補修用はその半減ほど)を流し、通電直線部の鋼と鋼が接触する部位がもっとも抵抗値が大きいのでここで発熱溶融しつつ、一定の保持時間を与えることで1点のスポット溶接は完了する。この溶接の利点は、溶接混として、ナゲットと呼ばれる円形の凹みは生じるが、トリミングとかウェザーストリップなどで隠れる部位が溶接箇所になることもあるが、溶接後にバリ取りサンダーリングやパテ埋め成形などの後処理が不要なことがある。ただし、1点当たりの溶接強度は十分とは云えず、特に点であるので、そこに捻りの応力が働くと弱いので、ある程度の間隔を開けて連続してスポット打点を繰り返す必用があるということだ。

ここである程度の間隔を開けてと記したのは、スポット打点と次のスポット打点が近すぎると、その旧スポット打点を通じて電流が流れる(これお無効分流と呼ぶ)現象が起き、あまり接近したスポット打点では、返って溶接強度を出すことができないという点に問題がある。このため、各スポット打点の間隔は20~25mm程度(強度負荷の低い部位ではもっと間隔が広い場合もあり)離して打設する様に作業者に指導していたのだった。しかし、人が手作業でやるスポット打設は、一々計測しながら打設する訳でもなく、打設間隔が長くなったり短くなったり、ある場合は省略して比較的長いスパンで打設が打ち漏らされたりという不具合が生じることが、今回のキシミ音の原因だと判ったとのことおだ。
その後、ボデー組立ラインはロボットによる自動化がなされ、新しい車両を量産開始する時点で、作業車がロボットにスポット打点位置を記憶させる作業(これおティーチングと呼んでいる)をするだけで、ロボットは疲れることも、忘れることもなく、寸分違わず同じ位置にスポットを繰り返すのだ。後年、損保調査員になってから知るが、同じ工場で作られた同型車種では、異なる固体の車種間でも、スポット打点は、寸分違わず一致するので、組み合わせ部品の合わせ作業において、このことを利用する場合もあることを知る。
なお、雑事ではあるが、ラリー車を作るなどとして、ロールゲージを室内に組むのも、ボデー剛性を高める意味もあるのだが、ボデー補強の一番として、スポットの増し打ちというものがあることを、この項のさごの話題として若干触れてみたい。
スポット増し打ちとは、先に述べた様にスポット溶接は無効分流という特性のため、あまり接近した打点では、本来溶接したいヶ所に十分な電流が流れず、従って発熱量も低く十分な溶接強度が出ないということだ。したがって、現状のスポット間隔の中央だとか、その間隔内を3分割して2点割増追加打点をスポット溶接機で行うことは不可能なのだ。この場合は、次の様な手法により、スポット打点11点と同等以上の溶接強度を得ている。
この手法は、俗にプラグ溶接と呼ばれる手法で、溶接部位のパネルが2枚合わせならその1枚に、3枚合わせならその2枚に、8Φ程度のスポット切り離し用の平面エンドミル歯先のドリルキリ(俗称スポットカッター)で残り1枚をなるべく痛めない様に穴開け加工する。そして、MIG溶接機(半自動と呼ばれる溶接ワイヤが自動供給される溶接機で、シールドガスに炭酸ガスかアルゴンとの混合ガス(アルタンと呼ぶ)を使用する溶接機)で、穴を塞ぐ様に溶接トーチを穴の外周をなぞる様に円を描いて動かす。あまり溶接電流が強かったり、トーチの動かし方が遅かったりすると、溶け込みすぎて裏板が溶け落ちて穴が空く、また溶接電流が弱いとか、トーチの動かしが遅すぎると、溶け込み不良で十分な溶接強度が出ない。溶接外観とか裏板の除隊を観察しつつ、適度な溶接電流(もしくは適度な溶接ワイヤー径もある)と適度なトーチの動かし速度を習得する必用がある。なお、このプラグ溶接は、溶接部表面はある程度半径に盛り上がるので、事後サンダーリングで擦り落とし、場合のよってはポリパテで仕上げる作業が追加となる。
2.日産アリアの樹脂バンパーをボデー(鋼板&アルミ板)と一緒に塗装ラインで塗り作業していることについて
これは当ブログ「日産アリアプロダクション 2021-11-14」でも記したことなのだが、従来の1液型熱硬化塗料は130-140℃で30分-40分の加温乾燥時間で完結するが、樹脂バンパーはブレンドは各車ある様だが、機材としてはPPが主成分のものだろう。これの熱変形に耐える許容温度は80℃程度と知見されるが、乾燥温度を140から80℃程度に低下させているのは間違いないだろうということを、件の人物に質問してみたところ、やはり乾燥温度の低下にあり、その要請はバンパーだけの問題ではなく、プラント内でもっともエネルギー消費(云うなればCO2対策の一環)の大きい部署として、塗装ラインがあり、これへの対策がバックグラウンドとしてあると云う説明だった。
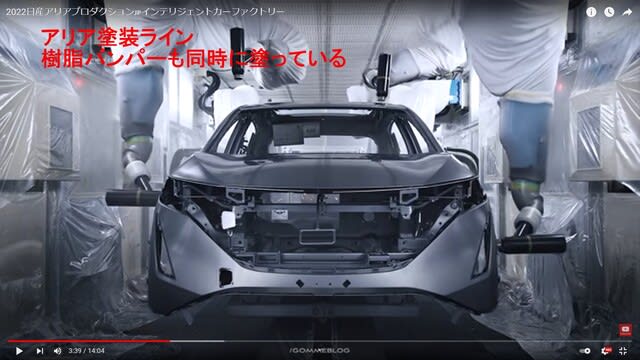
ここで使用の塗料は、関ぺ、日ペ、その他の熱硬化型塗料だが、その重合温度(架橋反応温度)を従来より低下させる特性のものにしているだろう。なお、バンパーなどの樹脂部品は、従来はボデーの熱硬化型とは別の部署で、2液ウレタン型塗料で別に施工しており、新車時から色味が一致しないとか、使用過程で退色が不整合で色味の差異が目立つなどの弊害があり、高級車などでは。色味を合わせた選択仕様までを行っていたのだが、これは製品歩留まりを向上させる意味でも大きな前進と云えるだろう。
ただし。これは筆者の知見から来る想像も交えるが、熱硬化温度を低下させた新塗料は、従来より塗料の製品出荷から可使期間が大幅に縮む可能性があると予見される。これは、重合型接着剤でも同様なのだが、熱とか硬化剤の混合による化学変化だが、元来そのその重合反応を停めるブロック剤因子が含まれており、そのブロックを解くために熱を上げたり硬化剤を混合したりする訳だが、期間と共に徐々にブロック剤の効果は薄れていくものなのだ。従って、熱重合温度を下げると云うことは、よりブロック剤の因子が臨界点に近づくことを暗示しており、たぶん塗料製造後の使用可能期間は大幅に圧縮されると思える。定かではないが、従来型の130℃1液熱硬化で3ヶ月程だと聞いているが、もしかすると環境温度によっては1ヶ月程になる場合すらありそうに想像する。
ついでに、このアリアもそうだが、下塗りはカチオンED(電着)で水性エポキシ熱硬化型で、デッピング後に1ベーク(加温)だが、その後、中塗り、カラーベース、トップコートクリアーと水性塗料をウェットオンウェット(未乾燥状態で塗り重ねる)で塗り、最後に1ベーク(加温)という3C1B(3コート1ベーク)が現代の超高級でない一般的な車両の標準となっていることは知っておきたい。
なお、アリアでは、塗膜表面のゴミ、ブツの異常の検出と、パネル表面の歪みの検査を、機械的センシングで行っている様子が判る。従来この様な検査は、直管式蛍光灯が多数並んだ部屋で、その映り込む蛍光灯の姿だとか明るい照度環境で、人が目視でなで回す様に角度を変え目視検査していたものだ。
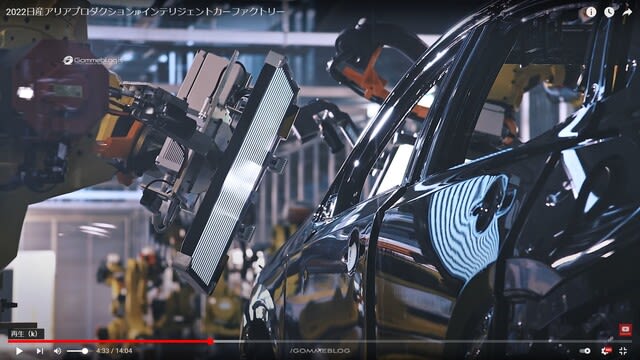
日産アリアプロダクション
2021-11-14 | 車と乗り物、販売・整備・板金・保険
https://blog.goo.ne.jp/wiseman410/e/8f0167c8cdf333fb111b670eafdbf45e