ジェットエンジンンの設計技師(4)
作成日;H26.5.5 KTR45051
改定日;R2.12.31
第3話 規制緩和と設計手法の関係
第2話で紹介したV2500エンジン(1987年初飛行のエアバス社のA320に搭載) の日米英独伊の国際共同開発、それとGE90エンジン(1994年初飛行のボーイング社のB777に搭載) の日米仏伊の国際共同開発に、私がChief DesignerやChief Engineerなどとして関与した時期は、まさに民間旅客機の飛行に関わる規制緩和が主としてエンジンの信頼性の向上と関連で積極的に進められた時代でもあった。
私は、2009年にそうした経験と実績を踏まえて「初期品質安定設計法の提案と評価」を書き、博士(工学)の学位を頂いた。丁度40年間の会社勤めの定年退職直後であった。
この論文において、私はこれまでの設計法の評価と発展について分析し、それに基づいて、エンジン開発を取り囲む、技術伝承、開発機種増加、リーダーの指導力低下などの、予測される21世紀の社会環境の変化に対応する設計法として、「初期品質安定設計法」、「E-QAD」(Early Quality Assured Design)というものを提案した。提案の流れは、次の図の通りである。
「第1期の質設計」の時代は、V2500エンジンの設計の期間で、従来から開発設計に適用されていたTQC(Total Quality Control 統合的品質管理) 、SQC(Statistical Quality Control 統計的品質管理) 、QFD(Quality Function Deployment 品質機能展開)などを、より積極的に取り入れることが行われた。それによって信頼性の向上が実現された。
こうした努力が実を結び、1953年に定められた、双発旅客機はエンジン1基停止状態で60分以内に着陸可能な空港に到着することができるルートを飛行しなければならないとするETOPS(イートップス)(Extended-range Twin-engine Operational Performance Standard:双発機による長距離進出運航規準)-60という規制が、それから約30年後の1985年に、ようやく緩和された。双発旅客機はエンジン1基停止状態で120分以内に空港に到着することができるルートを飛行しなければならないというETOPS-120に変更されることになった。そして、その後、180分、207分、240分以内にする ETOPS-180、207、240と、さらに緩和が促進されることになった。
しかし、当初はその認定を得るためには同エンジンの実際の商用運行実績データに基づく信頼性の証明が不可欠であり、認定取得までに要する期間の長さが問題になった。
実際、私がロンドンのヒースロー空港で見かけるB767機は、コックピットの真下に「ETOPS」との表示のある機体と、表示のない機体が並んでいた。表示前の機体は、まだ運行時間数が足りないことを意味しているので、大西洋路線には使えないことを示していいる。
そして、期間短縮のため、開発時の試験や設計プロセスなどに基づいて信頼性を立証し、それによって運行開始当初からの大洋横断飛行などの実施が求められるようになった。
そこで、初期品質に関するロバスト性(robust 強靱・堅牢)が求められ、このためジェットエンジンの開発設計においても、いくつかの産業分野で採用が始まっていた、田口玄一博士によって体系化された技術開発の方法論「タグチメッソド」(Taguchi Methods)の広範囲の適用を行うことにした。広範囲とは、基本設計分野にとどまらずに、詳細設計と加工精度の信頼性を増すために、適用範囲を大幅に広げることだった。それが「第2期の質設計」の時代である。そうした努力が実を結び、Early-ETOPSと呼ばれる考え方が、B777の1994年の初飛行に導入されることとなった。
以上の「第1期の質設計」の時代、そして「第2期の質設計」の時代とも、それぞれの手法の適用の時期や範囲などは、すべて設計リーダーと担当者の判断に委ねられており、その意味では、質設計の暗黙知的な適用の時代とも言えるものであった。
しかし、21世紀に入り、社会環境の変化が顕著になり、質設計を暗黙知的に適用するのでは安全性の継続に問題が生じるとの認識が生まれた。そして、従来の設計プロセスを総合的に見直し、特に初期品質の信頼性の安定に寄与するこれらの手法の適用時期と方法を、より明確に規定すべきとの結論に至った。すなわち、適用時期と方法に関する知識を暗黙知(Tacit knowledge)ではなく形式知(Explicit knowledge)とすることだった。
規制緩和とETOPS(イートップス)(双発エンジン距離延長運用性能規準)
ETOPS(双発エンジン距離延長運用性能規準)について、少し説明を加えることとする。
工業製品に対する規制は常に強化される傾向にあると思われるかも知れないが、必ずしもそうではない。ある時期からは規制緩和が行われることになる。1980年代後半からの航空機がまさにそのときであった。航空機の利便性の向上のために規制緩和が進められることとなったのだが、それはジェットエンジンの信頼性の向上がなければ不可能なことであった。1980年以降、エンジンの設計と製造の信頼性の高まりと並行して、規制緩和による民間航空機の利便性の改善が行われた。国際機関が定めた新たな規制緩和のルールを恒久的にするためには、たった一つの事故も許されない。そのためエンジンの設計・開発・生産の信頼性技術の進歩と定着が強く求められた。そして、その傾向が20世紀の終盤まで続いた。しかし、技術者の世代交代が明らかになった2010年以降は、その形式知化された初期品質安定設計法が正しく行われているとの確証はない。筆者の眼には、多くの初歩的なミスが繰り返されているように思える事案が散見されるようになった。
規制緩和による民間航空機の利便性の改善で重要な意味を持っているのは、双発機のエンジン1基停止を想定して、国際民間航空機関ICAO(International Civil Aviation Organization) が設けたETOPS(イートップス)(Extended-range Twin-engine Operational Performance Standard)というルールである。
双発機は、エンジンが1基停止すれば、残りの1基で飛行しなければならなくなり、そのため、かつて双発旅客機は1基でも空港まで戻ってくることができる範囲ということで、空港から100マイル(約185㎞)以内のルートを飛行することとされていた。それが1953年、米連邦航空規則「FAR 121.161」 によりETOPS-60という規則に変更された。双発旅客機はエンジン1基停止状態の巡航速度で60分以内に、着陸可能な空港(Adequate Airport)に到着することができるルートを飛行しなければならないという形で規制されるようになった。
Sec. 121.161
Airplane limitations: Type of route.
…………
(1) Farther than a flying time from an Adequate Airport (at a one-engine-inoperative cruise speed under standard conditions in still air) of 60 minutes for a two-engine airplane or 180 minutes for a passenger-carrying airplane with more than two engines;
Boeing ETOPS Flight Operations Overview. Sep. 2009 これから計4枚の資料を引用させてもらった。
http://www.captainpilot.com/files/ETOPS/ETOPS%20Flight%20Operations%20Overview.pdf
このETOPS-60の適用を受けた双発旅客機であれば、飛行可能領域は、1時間の片肺飛行で飛行可能な距離を400海里(約740㎞)とすると、上図の緑の陸地部分と白の海洋部分になる。かなりの範囲をカバーできる。しかし、これだと、例えば、下図のように、大西洋横断となると、かなりの回り道のルートを飛行しなければならなかった。
この規定が設けられた1953年以降、航空関連技術は大幅に進歩し、とくに航空エンジンは、ピストンエンジンからジェットエンジンが主力となり、そのジェットエンジンは目覚ましい進歩を遂げた。しかし、この規定は維持され続け、それが投入路線との関連で大きな制約となってくるため、ロッキードL-1011トライスター、ダグラスDC-10の三発旅客機の開発が行われ、双発機では難しい路線などに投入されることとなった。
米ロッキード社は1966年、3発機のL1011トライスター開発計画を発表。1967年には、受注体制が整ったと発表され、1970年には初飛行が行われた。そして1972年から実際の運行が開始された。
日本では全日空に1974年に導入され、グアムや香港などの路線に投入された。
米マクドネル・ダグラス社は1967年、ロッキード社に続いて3発機のDC-10開発計画を発表。 1970年には初飛行が行われた。
そして先行する対抗機、米ロッキード社のL-1011が、搭載エンジンのロールス・ロイス社の経営問題などで混乱している間に、一足早く、1971年に実際の運行が開始された。
日本航空には1976年に導入され、南回り欧州線やアンカレッジ経由ニューヨーク線、東南アジア線などの路線に投入された。
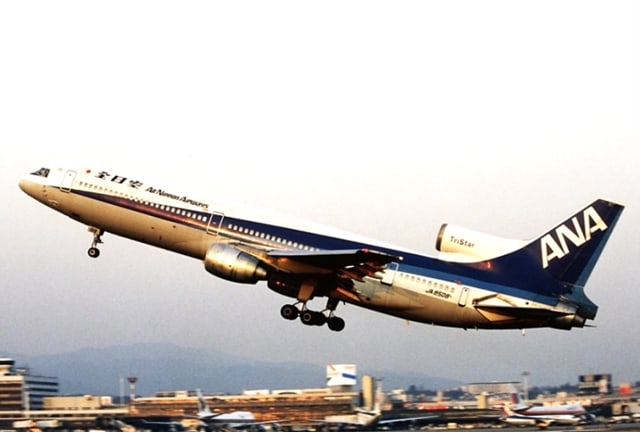
http://page.freett.com/nagoyaairline/japan/jal_dc10_040216.JPG
http://cdn-www.airliners.net/aviation-photos/photos/3/8/7/2020783.jpg
http://ja.wikipedia.org/wiki/DC-10_(航空機)
その後、1985年1月、米連邦航空局「FAA Advisory Circular 120-42」により60分が120分に拡張された。 それは1985年6月に撤回されたが、1988年12月の米連邦航空局「FAA Advisory Circular 120-42A」 により、適格空港(Adequate Airport)までの時間が、双発旅客機の機種によって、75分、120分、180分という規則が適用されることになった。
これらETOPS-120とETOPS-180の2枚の飛行可能範囲を見れば一目瞭然であろう。いずれかの認可を取得すれば、双発旅客機でほとんど世界中を飛行できるのである。現在ではさらに拡大し、北半球運航に支障がなくなる207分、南半球運行に支障がなくなる240分という規則も現れている。そして大西洋・太平洋横断の旅客機も完全に双発機が主流の世界になっている。
現在製造中の民間旅客機の中で双発機ではないのは、エアバス社の2005年初飛行の座席数500席以上の大型旅客機A380と、ボーイング社の1969年初飛行とはいうものの、進化を続けてきている座席数がほぼ同じB747の2機種だけである。
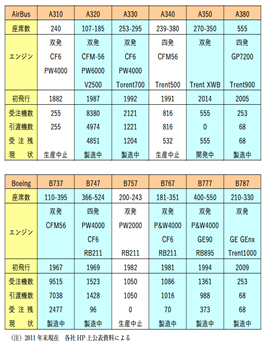
http://www.boeing.com/commercial/products.html http://www.airbus.com/aircraftfamilies/
かつて日本の空を飛び回った三発機は姿を消していった。日本航空で使用されていたボーイング社のB727は1987年に退役した。全日空で使用されていたB727も1990年に退役した。
また日本航空で使用されていたマクドネル・ダグラス社のダグラスDC-10も2005年10月に退役した。マクドネル・ダグラス社自身も1997年にボーイング社に買収され、1998年にはマクドネル・ダグラス社名での航空機販売は終了した。
プロペラ機からジェット機へ、そしてジェット機も三発機、四発機から双発機へと姿を大きく変えてきている。
しかし、エアバス社の大型旅客機A380と、ボーイング社の2機種も2020年に発生したCOVIT-19の世界的な蔓延による国際航空便の大幅な減便で、多くのエアラインから姿を消すことになってしまった。
今回の第4話の内容については、友人の井上利昭氏(元IHI)と前田勲男氏(戦略経営研究所)から多くの資料と助言を頂いた。文末ですが、お礼を申し上げます。
参考・引用元
http://www.i-a-e.com/products/overview.shtml
http://iaenews.com/?page_id=27&album=1&gallery=13
http://www.geaviation.com/engines/commercial/ge90/
http://futurepredictions.com/2011/05/future-predictions-tomorrows-turbine-genx-jet-engine-design-and-ge90-biggest-jet-engine-of-them-all/
http://ja.wikipedia.org/wiki/TQC
http://www.atmarkit.co.jp/aig/04biz/tqc.html
http://www.atmarkit.co.jp/aig/04biz/sqc.html
http://ja.wikipedia.org/wiki/統計的プロセス制御
http://www.icao.int/Pages/default.aspx
http://rgl.faa.gov/Regulatory_and_Guidance_Library/rgFar.nsf/FARSBySectLookup/121.161!OpenDocument#_Section3
Boeing ETOPS Flight Operations Overview. Sep. 2009 これから計4枚の資料を引用させてもらった。
http://www.captainpilot.com/files/ETOPS/ETOPS%20Flight%20Operations%20Overview.pdf
http://www.flightglobal.com/airspace/media/civilaviation1949-2006cutaways/images/8833/lockheed-l-1011-tristar-cutaway.jpg
http://ja.wikipedia.org/wiki/ロッキード_L-1011_トライスター
http://upload.wikimedia.org/wikipedia/commons/2/20/ANA_L-1011_JA8508_itm.jpg
http://page.freett.com/nagoyaairline/japan/jal_dc10_040216.JPG
http://cdn-www.airliners.net/aviation-photos/photos/3/8/7/2020783.jpg
http://ja.wikipedia.org/wiki/DC-10_(航空機)
http://rgl.faa.gov/Regulatory_and_Guidance_Library/rgAdvisoryCircular.nsf/8ce3f88c034ae31a85256981007848e7/2638eaf8b89680a8862569ba00751c8c/$FILE/Pages%201-15.pdf
http://www5a.biglobe.ne.jp/~bluesky/top.htm