国家プロジェクト(国プロ)の支援を受けて 2008 年 から 700℃級 A-USC 蒸気タービン開発を行ってきたでつ。
主要な開発項目は,700℃ 10 万時間で 100MPa以上の高温クリープ強度を持ち,10 トン以上の大型鍛造ロータを製造可能とする
Ni基材料の開発や,Ni基と高Cr鋼の異材溶接ロータ製造技術。
これらを検証するため,最終的に,実機大のタービン回転試験を行ったでつ。
この試験条件は 700℃以上の温度場で異材溶接ロー タを持つ蒸気タービンを3600rpmで長時間回転するものでつ。
蒸気タービンは,1908 年国産初の陸用蒸気タービン(500kW)を製造してから,現在 累計出力 360GW を超える迄に至るでつ。
蒸気タービンが現代においても継続してニーズが高い理由 は,長期間にわたって安定した電力を供給してきた実績に基づくことが大きいでつ。
また,蒸気条件の 向上や,設計手法にいち早く最新の解析技術を採用し,高効率化及び高信頼性に伴う最新技術を実製品に適用することで,
蒸気タービンは進化し続け,電力エネルギー需要の期待に応え続け てきている点も大きいでつ。
近年では,環境問題を踏まえて,単機出力容量の増大化,高効率化のニ ーズがより一層高くなってきたでつ。
図1に石炭火力プラントの蒸気条件の変遷について示すでつ。

石炭火力の蒸気条件は,亜臨界 圧,超臨界圧,そして 600℃級超々臨界圧発電(USC)と経てきたでつ。
これら各年代で採用されてき た最高の蒸気条件は,時代ごとに発展してきている蒸気タービンの高効率化技術適用との相乗 効果を伴い
プラント全体の高効率化達成に寄与してきているでつ。
この蒸気条件向上の延長として, 600℃級 USC から更に温度を 100℃上げた 700℃級 A-USC(Advanced Ultra Super Critical)の
実用化ニーズが世界的に高まってきているでつ。
A-USC が実現できれば,タービン効率は 50%を 超え,プラント効率も 46%HHV(高位発熱量基準)以上が見込まれるでつ。
この効率向上量を燃料費 換算すると,USC に比べて年間 16~20 億円程度低減できるでつ(2017 年1月時点の石炭価格 60~ 80$/tonより試算)。
CO2も世界平均値より25%~27%の削減に寄与するでつ。
また,A-USCは既設 石炭火力とシステム構成が同じなので,経年火力のリプレースとしての利用も容易。
日本では,2008 年より経済産業省の補助事業として国プロが進められてきたでつ。
以下,A-USC タービン開発の内容を記載するでつ。
現在商用化が検討されている先進 12Cr 鋼の適用限界は 630℃レベルであって,それ以上の蒸気温度を達成するには,Ni基合金の採用が見込まれるでつ。
だけど,Ni 基合金の特性には,温度 変化に対する組織変化の感受性が強いという製造上の課題があるでつ。
そのため,大型素材の製造 ほど,表面と内部の温度勾配がつきやすくなるので,成分元素の濃度分布が不均一になる偏析を生じる問題があるでつ。
試験片レベルや小さな素材で如何に高い強度特性が得られても,大型素 材にわたり設計者の目標を満足する強度を確保することは難しいでつ。
そのため,蒸気タービンロー タなどに適用できる数トン規模の Ni 基合金開発とその長期信頼性の検証が,A-USC 開発にとって最も大きな課題となるでつ。
また,高価な Ni 基合金を使用する量を抑えた設計が必要であって,特 に大型鍛造の製造が難しいロータにおいては,Ni基合金による溶接ロータ製造も大きな課題でつ。
図2に開発マスタースケジュールを示すでつ。
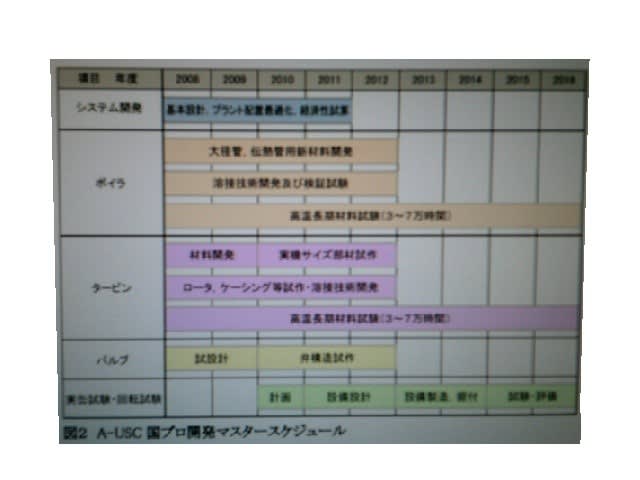
2008 年から 2012 年の間に,ボイラ,タービン,弁に 係る材料・要素技術開発が行われたでつ。
それら要素技術開発の信頼性を検証するために,2013年から2016年の間に,ボイラ実缶試験,タービン回転試験を行い評価したでつ。
表1に開発してきたNi基合金について示すでつ。

これらの材料は,国プロ開発時の目標10 万時間 100MPa 以上の高温クリープ強度が達成される見込みであり,FENIX700及 び LTES700Rでは
10 トン級の大型鍛造ロータの試作に成功。
また,これら材料はΦ1000 程度の大型鍛造ロータ試作で,非破壊検査による検出寸法が2mm 程度以下の結果を得たでつ。
一 方,USC141や USC800は,高温強度に優れるのみならず,製造加工性に優れており,翼,ボ ルト材のみならず,ボイラ配管等の適用も見込まれているでつ。
これら各材料の長時間クリープ強度 は,実際に 10 万時間以上継続して試験が続けられる予定であり,長時間の信頼性を検証中。
またタービン設計に必要な材料機械特性を習得し,回転試験用のタービンロータ設計に反映してるでつ。
Ni 基合金について,鍛造ロータ製造限界とコスト低減化のため,Ni 基合金と Cr 鋼による異材 溶接ロータ製造技術は A-USC を実現するためのキーテクノロジーのひとつ。
図3に溶接ロ ータの施工例を示すでつ。
既に高 Cr 鋼などの溶接ロータ製造実績を持ち,その技術を Ni 基 合金にも展開。
溶接手法は実績のある TIG 溶接を採用し,実物大のモックアップ溶接を行い,継手性能(組織,機械特性など)を検証した後に回転試験用溶接ロータの施工を行ったでつ。
溶接ロータの製造の信頼性検証を行うために非破壊検査も重要技術。
Ni 基合金は超音 波透過性が劣るでつ。
しかしながら,LTES700Rの結晶粒度は細かく,素材の MDDS(最小検出欠陥 径:Minimum Detectable defect Size)は2以下を得たでつ。
また,溶接部の超音波透過特性を評価し, 溶接境界の散乱波ノイズを低減したセンサを開発。
図3に溶接部の非破壊検査結果を示すでつ。

素材及び溶接部においても非破壊検査で問題は無く,健全性が確認したでつ。
タービン翼構造やロータ翼溝構造は複雑であり,かつ組立製造上の加工公差が厳しいでつ。
Ni 基 合金のような難削材の切削で,従来並みの加工公差を保つには,製造面の技術向上が必要。
タービンの製作施工事例として鍛造翼の切削加工例を表2に示すでつ。
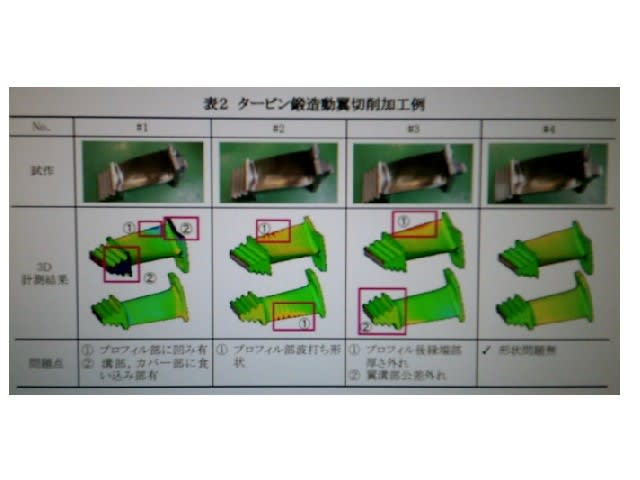
Ni基合金は硬く粘い性質 を持つ難削材であり,かつ熱伝導率が低切削熱が切削のか所に集中するため,
工具損傷が 部分的に著しく早く発生する問題があったでつ。
施工当初は,工具チップの選定や切削油の管理などに苦労したでつ。
現在は,これらの課題をクリアし,従来の製造と同様の加工精度が得られているでつ。
また,回転試験ロータには部分負荷運転に対応する調速段翼を計画。
近年,再生可能エネ ルギーが多く採用されるので,例え A-USC での性能向上を達成しても,
部分負荷運転も考慮して おくべきと考えたから。
図4に調速段翼の製造例を示すでつ。
調速段翼構造は,3本の翼が一体構造で翼根部はフォーク構造を有しており,製造上
最も難しく複雑な構造をしているでつ。

そのため,この調速段翼構造の製造試作は,難削材製造・加工・組立技術向上に大いに役立ったでつ。
タービンコンポーネントの信頼性を検証するため高温場回転試験を行ったでつ。
高温場回転試験 ロータの製造及び検証内容を図5に示すでつ。

主な試験目的は,Ni基合金の実機大タービンの製造性の確認や高温回転試験を経た後の各種部材の余寿命評価を行い,特に溶接継手部の信頼 性を検証することででつ。
試設計した二段再熱蒸気タービン構造に基づき, LTES700R の共材溶接,LTES700R と MTR10A の異材溶接部を含み,翼形状の製造性が比較的 困難である調速段と
IP6段,7段を模擬したロータを回転試験用ロータ構造に採用(図6)。

調速段翼については,先に述べたとおり,複雑な翼構造の製造性や組立性が Ni 基合金で成 立することを確認。
また,IP 翼については,鍛造翼の製造性を確認。
異材継手は,実機 での採用を想定し,IP 段落間に備えているでつ。
タービン回転試験設備及びロータ構造及び設備計画構造を図7に示すでつ。
この設備の特徴は, ヒータの放射により 700℃以上の温度場が模擬され,駆動モータによって
真空中 3600rpm の定格 回転で長時間試験するものでつ。
試験中,最も応力が高い部位はタービン翼溝部であり,実際の運用上はこの箇所が700℃の雰囲気に曝されることは無いでつ。
それゆえ,実際の運用に比べて, 本試験は寿命評価の加速試験となるでつ。
当初は、調速段翼周りを約 730℃に保ち 1500 時間試験を行うことで、10万時間のクリープ加速 試験を計画。
だけど、実際は風損により IP段落間の継手温度が上昇したため、設備及びロータ改造を行い、最終的に 3600rpmの定格回転数で 1051時間試験。
試験中,軸振動,軸伸 び,ヒータパネル雰囲気温度,ロータ温度などを 24hr/日監視。
図8に試験ロータと,試験中 の調速段翼の写真を示すでつ。
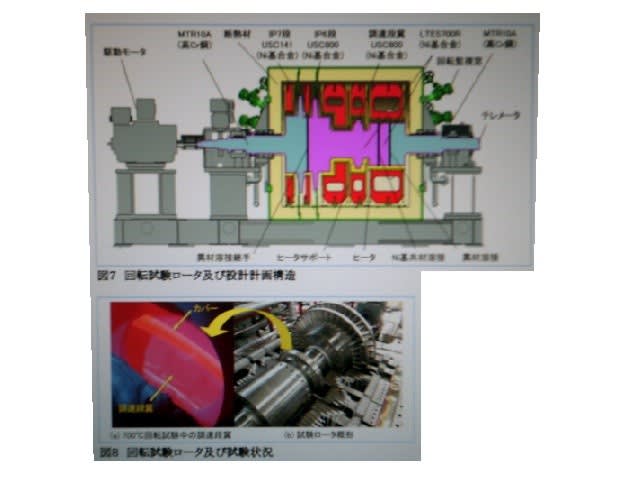
回転試験中,調速段部は700℃以上,異材継手部は 600℃程度の温 度場を保ったでつ。
1051 時間の連続回転試験で,異材継手部で 16 万時間,調速段翼で1万時間相当のクリープ損傷を達成。
回転試験後,目視点検,非破壊検査,ロータ振れ計測などを行い 試験前後と比較した結果,特に問題は無く健全性が確認。
現在,ロータを解体して試験片を抽出し,余寿命評価を行っているでつ。
2008 年より9年間実施してきた A-USC タービン開発は,経済産業省及び国立研究開発法人 新エネルギー・産業技術総合開発機構(NEDO)の
助成事業によるもので計画通り完了。
これまでの技術開発により,700℃級蒸気タービンの実機製造の見通しはついたでつ。
また,タービンのみ ならず並行してボイラも実缶試験が終了。
ボイラ実缶試験は 700℃で1万3千時間を経過し,抜管後,試験サンプルを抽出して,信頼性検証を行っているでつ。
ボイラもタービンも素材及び溶接継 手のクリープ試験は,10 万時間を超えたものもあり,長時間信頼性検証が確立しつつあるでつ。
USC の実用化を日本で確立したことと同様,A-USC の実用化により地球温暖化抑制に貢献していくでつ。
ガスタービン同様、スチームタービンの高温化でコンバイドサイクルの効率向上にもつながるでつなぁ~
主要な開発項目は,700℃ 10 万時間で 100MPa以上の高温クリープ強度を持ち,10 トン以上の大型鍛造ロータを製造可能とする
Ni基材料の開発や,Ni基と高Cr鋼の異材溶接ロータ製造技術。
これらを検証するため,最終的に,実機大のタービン回転試験を行ったでつ。
この試験条件は 700℃以上の温度場で異材溶接ロー タを持つ蒸気タービンを3600rpmで長時間回転するものでつ。
蒸気タービンは,1908 年国産初の陸用蒸気タービン(500kW)を製造してから,現在 累計出力 360GW を超える迄に至るでつ。
蒸気タービンが現代においても継続してニーズが高い理由 は,長期間にわたって安定した電力を供給してきた実績に基づくことが大きいでつ。
また,蒸気条件の 向上や,設計手法にいち早く最新の解析技術を採用し,高効率化及び高信頼性に伴う最新技術を実製品に適用することで,
蒸気タービンは進化し続け,電力エネルギー需要の期待に応え続け てきている点も大きいでつ。
近年では,環境問題を踏まえて,単機出力容量の増大化,高効率化のニ ーズがより一層高くなってきたでつ。
図1に石炭火力プラントの蒸気条件の変遷について示すでつ。

石炭火力の蒸気条件は,亜臨界 圧,超臨界圧,そして 600℃級超々臨界圧発電(USC)と経てきたでつ。
これら各年代で採用されてき た最高の蒸気条件は,時代ごとに発展してきている蒸気タービンの高効率化技術適用との相乗 効果を伴い
プラント全体の高効率化達成に寄与してきているでつ。
この蒸気条件向上の延長として, 600℃級 USC から更に温度を 100℃上げた 700℃級 A-USC(Advanced Ultra Super Critical)の
実用化ニーズが世界的に高まってきているでつ。
A-USC が実現できれば,タービン効率は 50%を 超え,プラント効率も 46%HHV(高位発熱量基準)以上が見込まれるでつ。
この効率向上量を燃料費 換算すると,USC に比べて年間 16~20 億円程度低減できるでつ(2017 年1月時点の石炭価格 60~ 80$/tonより試算)。
CO2も世界平均値より25%~27%の削減に寄与するでつ。
また,A-USCは既設 石炭火力とシステム構成が同じなので,経年火力のリプレースとしての利用も容易。
日本では,2008 年より経済産業省の補助事業として国プロが進められてきたでつ。
以下,A-USC タービン開発の内容を記載するでつ。
現在商用化が検討されている先進 12Cr 鋼の適用限界は 630℃レベルであって,それ以上の蒸気温度を達成するには,Ni基合金の採用が見込まれるでつ。
だけど,Ni 基合金の特性には,温度 変化に対する組織変化の感受性が強いという製造上の課題があるでつ。
そのため,大型素材の製造 ほど,表面と内部の温度勾配がつきやすくなるので,成分元素の濃度分布が不均一になる偏析を生じる問題があるでつ。
試験片レベルや小さな素材で如何に高い強度特性が得られても,大型素 材にわたり設計者の目標を満足する強度を確保することは難しいでつ。
そのため,蒸気タービンロー タなどに適用できる数トン規模の Ni 基合金開発とその長期信頼性の検証が,A-USC 開発にとって最も大きな課題となるでつ。
また,高価な Ni 基合金を使用する量を抑えた設計が必要であって,特 に大型鍛造の製造が難しいロータにおいては,Ni基合金による溶接ロータ製造も大きな課題でつ。
図2に開発マスタースケジュールを示すでつ。
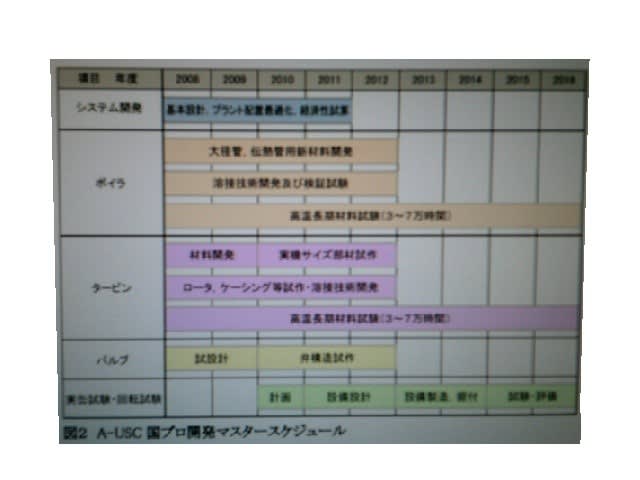
2008 年から 2012 年の間に,ボイラ,タービン,弁に 係る材料・要素技術開発が行われたでつ。
それら要素技術開発の信頼性を検証するために,2013年から2016年の間に,ボイラ実缶試験,タービン回転試験を行い評価したでつ。
表1に開発してきたNi基合金について示すでつ。

これらの材料は,国プロ開発時の目標10 万時間 100MPa 以上の高温クリープ強度が達成される見込みであり,FENIX700及 び LTES700Rでは
10 トン級の大型鍛造ロータの試作に成功。
また,これら材料はΦ1000 程度の大型鍛造ロータ試作で,非破壊検査による検出寸法が2mm 程度以下の結果を得たでつ。
一 方,USC141や USC800は,高温強度に優れるのみならず,製造加工性に優れており,翼,ボ ルト材のみならず,ボイラ配管等の適用も見込まれているでつ。
これら各材料の長時間クリープ強度 は,実際に 10 万時間以上継続して試験が続けられる予定であり,長時間の信頼性を検証中。
またタービン設計に必要な材料機械特性を習得し,回転試験用のタービンロータ設計に反映してるでつ。
Ni 基合金について,鍛造ロータ製造限界とコスト低減化のため,Ni 基合金と Cr 鋼による異材 溶接ロータ製造技術は A-USC を実現するためのキーテクノロジーのひとつ。
図3に溶接ロ ータの施工例を示すでつ。
既に高 Cr 鋼などの溶接ロータ製造実績を持ち,その技術を Ni 基 合金にも展開。
溶接手法は実績のある TIG 溶接を採用し,実物大のモックアップ溶接を行い,継手性能(組織,機械特性など)を検証した後に回転試験用溶接ロータの施工を行ったでつ。
溶接ロータの製造の信頼性検証を行うために非破壊検査も重要技術。
Ni 基合金は超音 波透過性が劣るでつ。
しかしながら,LTES700Rの結晶粒度は細かく,素材の MDDS(最小検出欠陥 径:Minimum Detectable defect Size)は2以下を得たでつ。
また,溶接部の超音波透過特性を評価し, 溶接境界の散乱波ノイズを低減したセンサを開発。
図3に溶接部の非破壊検査結果を示すでつ。

素材及び溶接部においても非破壊検査で問題は無く,健全性が確認したでつ。
タービン翼構造やロータ翼溝構造は複雑であり,かつ組立製造上の加工公差が厳しいでつ。
Ni 基 合金のような難削材の切削で,従来並みの加工公差を保つには,製造面の技術向上が必要。
タービンの製作施工事例として鍛造翼の切削加工例を表2に示すでつ。
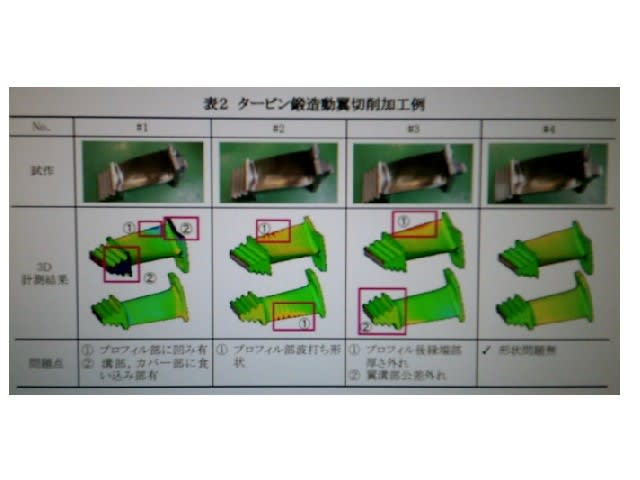
Ni基合金は硬く粘い性質 を持つ難削材であり,かつ熱伝導率が低切削熱が切削のか所に集中するため,
工具損傷が 部分的に著しく早く発生する問題があったでつ。
施工当初は,工具チップの選定や切削油の管理などに苦労したでつ。
現在は,これらの課題をクリアし,従来の製造と同様の加工精度が得られているでつ。
また,回転試験ロータには部分負荷運転に対応する調速段翼を計画。
近年,再生可能エネ ルギーが多く採用されるので,例え A-USC での性能向上を達成しても,
部分負荷運転も考慮して おくべきと考えたから。
図4に調速段翼の製造例を示すでつ。
調速段翼構造は,3本の翼が一体構造で翼根部はフォーク構造を有しており,製造上
最も難しく複雑な構造をしているでつ。

そのため,この調速段翼構造の製造試作は,難削材製造・加工・組立技術向上に大いに役立ったでつ。
タービンコンポーネントの信頼性を検証するため高温場回転試験を行ったでつ。
高温場回転試験 ロータの製造及び検証内容を図5に示すでつ。

主な試験目的は,Ni基合金の実機大タービンの製造性の確認や高温回転試験を経た後の各種部材の余寿命評価を行い,特に溶接継手部の信頼 性を検証することででつ。
試設計した二段再熱蒸気タービン構造に基づき, LTES700R の共材溶接,LTES700R と MTR10A の異材溶接部を含み,翼形状の製造性が比較的 困難である調速段と
IP6段,7段を模擬したロータを回転試験用ロータ構造に採用(図6)。

調速段翼については,先に述べたとおり,複雑な翼構造の製造性や組立性が Ni 基合金で成 立することを確認。
また,IP 翼については,鍛造翼の製造性を確認。
異材継手は,実機 での採用を想定し,IP 段落間に備えているでつ。
タービン回転試験設備及びロータ構造及び設備計画構造を図7に示すでつ。
この設備の特徴は, ヒータの放射により 700℃以上の温度場が模擬され,駆動モータによって
真空中 3600rpm の定格 回転で長時間試験するものでつ。
試験中,最も応力が高い部位はタービン翼溝部であり,実際の運用上はこの箇所が700℃の雰囲気に曝されることは無いでつ。
それゆえ,実際の運用に比べて, 本試験は寿命評価の加速試験となるでつ。
当初は、調速段翼周りを約 730℃に保ち 1500 時間試験を行うことで、10万時間のクリープ加速 試験を計画。
だけど、実際は風損により IP段落間の継手温度が上昇したため、設備及びロータ改造を行い、最終的に 3600rpmの定格回転数で 1051時間試験。
試験中,軸振動,軸伸 び,ヒータパネル雰囲気温度,ロータ温度などを 24hr/日監視。
図8に試験ロータと,試験中 の調速段翼の写真を示すでつ。
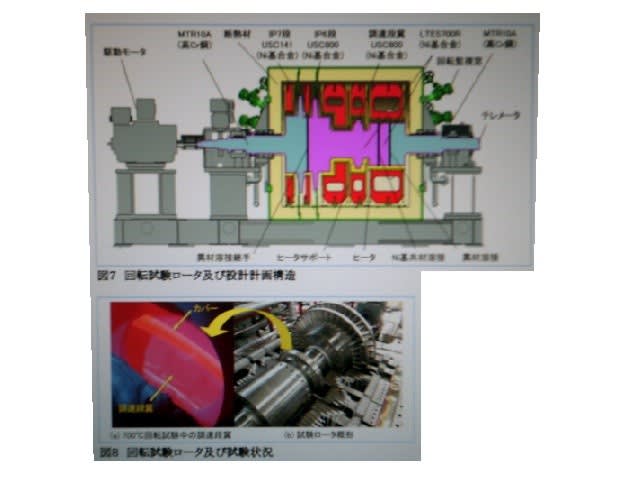
回転試験中,調速段部は700℃以上,異材継手部は 600℃程度の温 度場を保ったでつ。
1051 時間の連続回転試験で,異材継手部で 16 万時間,調速段翼で1万時間相当のクリープ損傷を達成。
回転試験後,目視点検,非破壊検査,ロータ振れ計測などを行い 試験前後と比較した結果,特に問題は無く健全性が確認。
現在,ロータを解体して試験片を抽出し,余寿命評価を行っているでつ。
2008 年より9年間実施してきた A-USC タービン開発は,経済産業省及び国立研究開発法人 新エネルギー・産業技術総合開発機構(NEDO)の
助成事業によるもので計画通り完了。
これまでの技術開発により,700℃級蒸気タービンの実機製造の見通しはついたでつ。
また,タービンのみ ならず並行してボイラも実缶試験が終了。
ボイラ実缶試験は 700℃で1万3千時間を経過し,抜管後,試験サンプルを抽出して,信頼性検証を行っているでつ。
ボイラもタービンも素材及び溶接継 手のクリープ試験は,10 万時間を超えたものもあり,長時間信頼性検証が確立しつつあるでつ。
USC の実用化を日本で確立したことと同様,A-USC の実用化により地球温暖化抑制に貢献していくでつ。
ガスタービン同様、スチームタービンの高温化でコンバイドサイクルの効率向上にもつながるでつなぁ~