ガスタービンコンバインドサイクル発電は,再生可能エネルギーと共存する最もクリーンで経済 的な火力発電設備として,長期的な市場拡大が予想されているでつ。
更なる高効率化を実現するた めには,タービン部材の特性向上と高度化した翼設計に基づく複雑な構造を実現するための製 造技術の開発が不可欠。
ガスタービンの高温化実現に向けた材料・製造技術と して,合金開発・鋳造技術,コーティング技術,溶接補修技術および冷却孔加工技術に関する開発状況を報告するでつ。

世界的なエネルギー需要は中国,インドなどのアジアを中心に近年著しく増加してて,2035 年の世界エネルギー消費は
2010 年時と比して約 1.5 倍に増加すると予測されているでつ。
エネルギ ー自給率が 10%に満たない我が国においてはエネルギーの有効活用ならびに環境負荷の低減 が急務。
とりわけ,現在日本の電源構成の約9割を火力発電が占めてて,その発電効率 向上への取り組みが求められているでつ。
発電効率は主機であるガスタービンの高温化に依存すると ころが大きく,1980 年代初頭から,高 温・高効率化および大容量化の開発を進めてきたでつ。
図1(1)にタービン入口温度の上昇と適用材料・技術の推移を示すでつ。

1984 年にタービン入口ガス 温度が 1100℃級のD形ガスタービンを開発し,以降,1989 年には 1350℃級のF形,
1997 年には 1500℃級のG形を,更に,2011 年には 1600℃級のJ形ガスタービンを開発)。
J形ガスタービ ンの開発においては先進遮熱コーティングや冷却・空力技術等,2004 年度から開始された国家プロジェクト研究である“1700℃級ガスタービン要素技術開発”に
おける開発成果も活用されてい るでつ(図2)。

ガスタービンの高温化においては,高温化に耐えうる新規材料の開発ならびに,タービン部材 の特性向上と高度化した翼設計に基づく
複雑な構造を実現するための製造技術の開発が不可欠。
その取り組みについて③以降に示すでつ!
タービン翼材料開発は高温環境下での使用に耐えうる高強度ニッケル基超合金としてこれまで MGA1400,MGA1400DS ならびに MGA2400 を開発し,製品に適用。
タービン翼向 けの超合金は,鋳造方法により普通鋳造合金,一方向凝固合金,単結晶合金に分類されるでつが,
これらの合金は普通鋳造合金(MGA1400,MGA2400)および一方向凝固合金(MGA1400DS)と して使用されているでつ。
単結晶合金は材料強度上不利となる結晶粒界を含まず,また粒界強化を 考慮せずに合金組成の最適化が行えることから
,最も高強度な合金となっているでつ。
但し,鋳造時 に生じる鋳造欠陥等による強度低下の影響が大きいことから,製造技術の確立が重要
。
特 に産業用ガスタービンのタービン翼は航空機エンジン用のタービン翼に比べ体格が大きいため に,より製造が難しくなっているでつ。
総合研究所では 1700℃級ガスタービンの実現を目指し,これまで物質・材料 研究機構(NIMS)と共同で単結晶翼向けの超耐熱材料開発研究を実施。
材料開発にあ たっては,材料の高温強度特性を確保するだけでなく,欠陥の無い良好な単結晶組織が得られ る鋳造技術の開発が不可欠。
また素材コスト,鋳造コスト等の経済性も同時に満足する必要。
さらに,高温強度特性については,クリープ強度,熱疲労強度,耐酸化性といった材料 特性を全て確保する必要があり,
特にクリープ強度と熱疲労強度を両立させることは技術的にハードルが高い課題。
NIMS にて開発された合金設計プログラムを活用して組成決定した 試作合金の評価を行うとともに,熱疲労強度を中心に特性予測データベースの充足を行ったでつ。
これら取り組みを通して,クリープ強度と熱疲労強度のどちらについても良好な特性を有する単結 晶合金である MGA1700 を開発(図3)。

高強度単結晶合金は一般的に高価な元素であるレ ニウム等のレアメタルを含有しているが,本合金はレニウムを含有せず高強度を実現した画期的な合金。
鋳造技術 上記材料開発に加え,方向凝固翼(一方向凝固翼と単結晶翼の総称)において発生しうる各 種鋳造欠陥(図4)を予測して,
鋳造条件最適化及び品質の向上を図るための鋳造シミュレーション 技術を開発(図5)。
(a) 異結晶発生危険度予測 異結晶は鋳物底部で発生させた結晶が下部から上部へ向けて一方向に成長する過程にお いて,
凝固途中で新たな結晶核が発生,成長するもので,鋳物各部位の凝固時温度勾配と結 晶成長速度のバランスが崩れた時に発生するので,
凝固伝熱解析によりこれらパラメータを評 価する事で発生傾向を予測できるでつ。
(b) 結晶成長予測 単結晶翼の鋳造においては鋳型底部の結晶生成・成長とセレクタでの結晶選択を正常に進 行させるため,
より厳密な条件設定が必要であるが,当該部の結晶成長状況についても同時 に計算予測可能。
(c) フレックル発生予測 方向凝固翼における鋳造欠陥であるフレックルは凝固時に生じる局所的な濃度分布に起因する溶湯の比重差により対流が発生し,
健全な結晶成長を阻害する事で発生するもので,凝 固中の溶湯密度変化,溶湯対流の障害となるデンドライトの間隔等を評価し,その発生危険度 を予測できるでつ。
(d) 再結晶発生予測 鋳物の凝固・冷却時に発生したひずみが限界値を超えて残留した場合,
これに起因して後 工程の熱処理時に再結晶が発生し,当該部の強度が低下するでつ。
そこで,鋳型,鋳物,その他 鋳型支持構造物を解析対象として,鋳造時の FEM 弾塑性解析を実施し,
算出した鋳造後の 残留塑性ひずみから再結晶発生危険度を予測する技術を開発。
これらシミュレーション技術を駆使して,鋳型形状設計,鋳造条件を決定し,MGA1700 合金を
用いた大型単結晶翼の試作を行ったでつ(図6)。
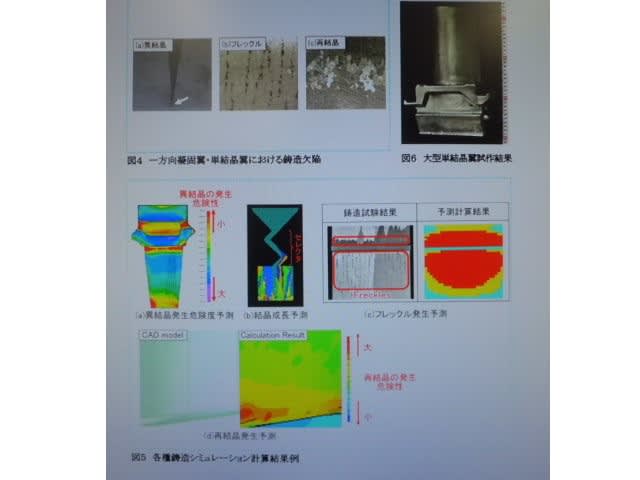
試作翼に顕著な結晶の倒れや,鋳造欠陥の発生 は認められず,健全な単結晶翼が鋳造できる事を確認。
遮熱コーティング技術は、 図1に示したように,ガスタービン入口温度は超合金の耐熱温度の上昇に比べはるかに速い速 度で上昇しているでつ。
これまで,冷却技術とコーティング技術の向上によって,この急速な高温化に 対応してきており,最新の 1600℃級J形ガスタービンには,
上述の通り国家プロジェクト研究で開発された先進遮熱コーティング(以下 TBC, Thermal Barrier Coating)が採用いるでつ。
以下に その先進 TBC の材料開発と施工技術について記載するでつ。
先進 TBC 材料開発は、材料組成の開発にあたっては,総合研究所で開発された,電子構造に基づく 材料計算システムを用いて,
低熱伝導で高温安定性に優れる候補材を選定した。選定された材 料組成で焼結体を作製し,熱伝導率と高温安定性を測定したところ,熱伝導率については従来 材である YSZ(イットリア部分安定化ジルコニア)よりも低く,高温安定性については,高温環境で も有害な単斜晶の発生を抑制できる候補材を見出すことに成功したでつ(図7)。
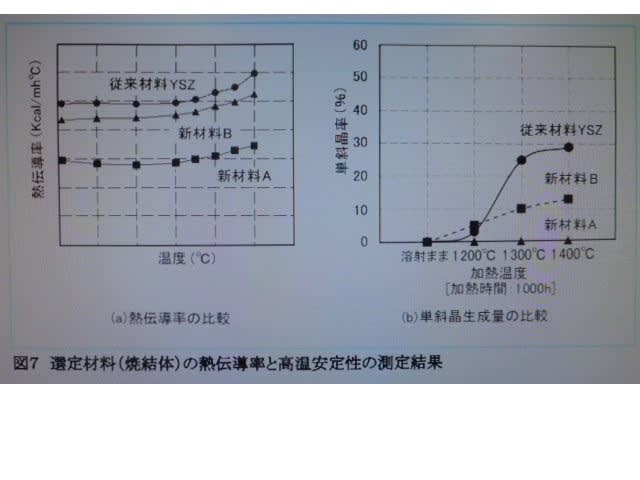
TBC は溶射によって施工され,皮膜中にミクロな気孔を導入することで焼結体よりもさらに熱伝 導率の低いコーティングを形成。
だけど過剰な気孔の導入は,高温・高流速の実機環境下で は,早期にはく離を生じさせたり,エロージョンによる減耗を招き,遮熱効果そのものを喪失させる 可能性があるでつ。
従って,材料組成の開発に次いで,溶射条件の最適化を含めた成膜技術の開発 が重要。
皮膜としての熱サイクル耐久性は,図8(a)に示すレーザ熱サイクル試験によって 評価し,このとき温度計測を併せて実施することで熱伝導率の評価も行うでつ。
また,実機環境を模擬 した高温・高流速下でエローダントを皮膜に衝突させることが出来る高温エロージョン試験装置 (図8(b))を開発し,皮膜のエロージョン特性を評価しているでつ。

これらの評価装置を用いながら,次 節で述べる溶射条件を最適化しつつ皮膜としての材料開発を行い,要求される信頼性・遮熱性を満足する皮膜を得ることができたどでつ。
施工技術は前述の通り,溶射条件を変えると皮膜のミクロ組織は変化し,それに伴って皮膜の遮熱性・信 頼性は大きく変わる。
そのため,各溶射条件に対してプラズマフレームがどのように変化し,溶射 粒子がどのように基材に衝突・偏平化していくかを高速度カメラで観察し,
粒子が過度に飛散し 皮膜中に欠陥を生じることが無いように,溶射条件の最適化を実施(図9)。

こうして決定した溶射条件で施工された皮膜は,試験片のような単純形状であれば良好な性能 を示すでつが,タービン翼は端壁を有し3次元的な曲率を持つため,
全面を試験片と同様な理想的か つ均質な皮膜とするのは容易ではないでつ。
そのためには,溶射ガンを持つロボットアームとタービン 翼を固定しているターンテーブルを同期させながら干渉を避けて,試験片と同様の条件で施工し
なければならないでつ。
このような複雑なロボットプログラミングを組むために,CAD を用いたロボットシ ミュレーション技術が用いられているでつ(図 10)。

このようにして作り込まれたロボットプログラミングを用いて先進 TBC を実翼施工した後,付帯 試験片での熱サイクル試験や実翼切断調査により,
実翼における皮膜の健全性を確認。
この ようにJ形ガスタービン向けの先進 TBC 技術を完成させ,2015 年 10 月までに約 13 万時間の累計 運転時間を経験し良好な運転結果を得ているでつ。
高温部材の溶接補修技術運転中に損傷を受けたタービン翼は,補修を行いながら設計寿命まで継続使用されているでつ。
効率的なガスタービンの運用を行うためには,新たに開発された単結晶合金である MGA1700 に
ついても現行の普通鋳造合金や一方向凝固合金と同様に,補修技術の確立が不可欠。
高温強度に優れる単結晶合金の特性を補修後も確保するためには,補修部も単結晶化する必要が有るでつが,
一般的な補修工法である溶接を適用した場合,溶接金属を単結晶組織とすることが 難しく,異結晶が発生した場合は加工除去等の対策を行わなければならないでつ。
溶接補修部を 単結晶化できる溶接条件を検討するツールとして,数値シミュレーションを用いて溶接ビード形状を予測し,
ビード内で単結晶組織が形成される領域を可視化する手法を検討。
溶接手法は,母材との希釈を制御し易い LMD(Laser Metal Deposition,レーザ粉体肉盛溶 接)を対象とし,
解析は汎用熱流体解析ソフト(Flow-3D)にて行ったでつ。
LMD の概略を図 11 に示すでつ。
溶接材料には,母材に用いられる MGA1700 合金と同一成分の粉末を用いたでつ。
初めに解析 により溶接ビード形状の予測を行い,実際に LMD により形成したビード形状と比較することで解 析の妥当性を調査。
図 12 に解析モデル及び解析結果の一例を示すでつ。
解析では,レーザ照 射位置に溶接材料を供給し,レーザが移動することで溶接ビードが形成されるでつ。
解析結果において青色部は母材が溶融していない領域を,赤色部は完全に溶融した領域を,赤から青に変化する色は部分的に溶融したことを示しているでつ。
図 13 に解析及び LMD の溶接ビード断面の比較を示すでつ。
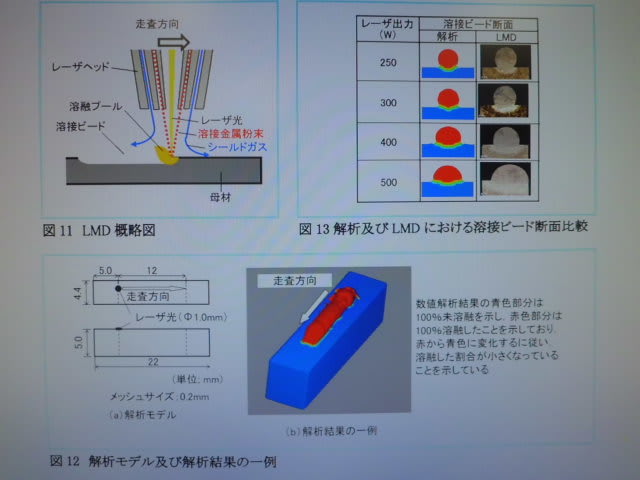
両者は良い一致を示していることが判るでつ。
溶接金属を母材と同じ結晶方位の単結晶組織とするには,溶融部境界における凝固時温度 勾配G(Temperature gradient)と
凝固速度R(Rate of solidification)を適切に制御し G/R を大きく する必要が有るでつ。
そこで,解析により LMD 条件を変化させた場合の各位置におけるG及びRを求め,評価を行ったでつ。
具体的には母材との融合界面で生成した単結晶組織が正常に成長できる領域を G/R 値の大きさから予測。
各溶接条件における健全成長領域の高さを予測した結果を図14 に示すでつ。
図中で,右下部の施工条件域は溶接入熱過少のため,また左上部の施工条件域 は溶接入熱過多のため,溶接施工が出来なかった領域でつ。
溶接金属が母材と同じ結晶方位 の単結晶組織となる領域を大きくするには,レーザ出力を大きく,
かつ溶接速度を小さくする傾向に制御すれば良いことが明らかとなったでつ。 解析により求めた適正条件を用いて LMD 施工を行ったでつ。
溶接ビード断面組織写真を図 15 に示すでつ。
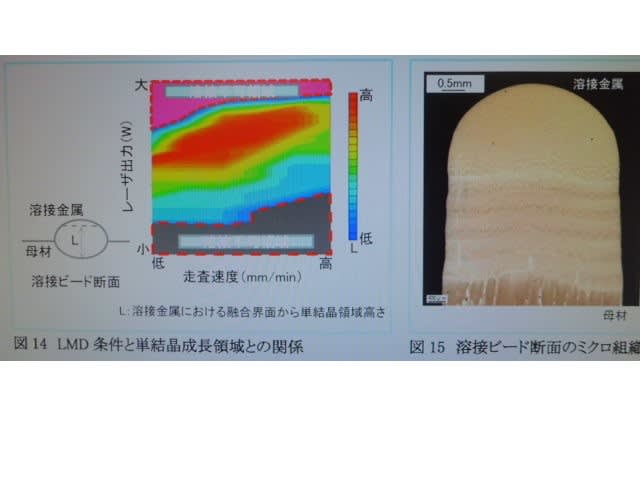
溶接金属部分は健全な単結晶組織を呈しており,良好な結果が得られていることが確認されたでつ。
現行の孔あけ加工はプロセス タービン翼は,高温環境下での使用に耐えるため,高強度ニッケル基超合金の表面に TBC が 施工されているでつ。
タービン翼の冷却孔(形状:丸孔,シェイプト孔)は,現状ニッケル基超合金に放 電加工等により孔あけを行い,溶射にて TBC をコーティングした後,
TBC には機械的孔あけを実 施して製造されてて,ニッケル基超合金と TBC は異なる手法で加工されるでつ。
こりは,放電加工 では,非導電性材料の TBC の加工が困難なため。
今後,ガスタービンコンバインドサイク ルのさらなる高効率化に向け,高温耐久性を向上させるべく
TBCの厚膜化,冷却効率向上のた めの冷却孔小径化が進むことが予想されるでつが,現行プロセスでは,TBC 溶射施工時に冷却孔が
閉塞するなど,製造が困難になると予測されるでつ
。
この課題を解決するため,TBC をコーティングし た後に,TBC とニッケル基超合金を一貫加工できる孔あけ加工法の開発が必要
。
冷却孔の主な形状には丸孔形状とシェイプト孔形状があるでつが,本開発では,レーザを用いた TBC/ニッケル基超合金一貫加工法の要素検証として,
より簡単な形状である丸孔を対象とし,薄 板の試験片(ニッケル基超合金:約1mm)を模擬材として用いて,孔あけ検証試験を実施。
短パルスレーザ/ファイバレーザによる2段階加工は レーザ加工は,非導電性材料である TBC およびニッケル基超合金の両者の加工が可能なため,
TBC/ニッケル基超合金の一貫加工に適した加工方法)。
ファイバレーザのような高出 力レーザを用いたレーザ熱加工は,微小な領域にエネルギーを集光させることで,加工対象を溶 融・蒸発させて加工する手法であり,高速加工に適する反面,エネルギー密度が高いため,加工 対象によっては十分な加工品質を維持する事が困難。
TBC は熱影響を受やすいため,フ ァイバレーザによる熱加工では,加工品質の維持が困難だったでつ。
こりに対して,短パルスレー ザはパルス幅が フェムト秒~ナノ秒 と熱加工で用いられる高出力レーザ(ミリ秒~連続波)に比 べてパルス幅が非常に短く,
熱影響を抑制した高品質な非熱加工が可能な利点を有するが,熱 加工で用いるレーザと比べて出力が低く,十分な加工速度を得ることが困難。
表1に短 パルスレーザとファイバレーザの特徴を示すでつ。
それぞれのレーザ発振器の特長を生かし,TBC 孔 あけに対しては,非熱加工により高品質加工が可能な短パルスレーザを適用し,
ニッケル基超合 金に対しては高速加工が可能なファイバレーザを用いる2段階加工方法を開発(図16)。

2段階加工 方法で用いる光学系には,高速高品質加工に適した独自技術であるプリズム ローテータを用いたでつ。
本開発では2段階加工の有効性を検証するため,より簡単な丸孔形状を対象として,加工試験 を行った。TBC/ニッケル基超合金の2段階加工方法を示すでつ(図 17)。

はじめにステップ1にて, TBC に短パルスレーザを円回転させて照射し加工する。これにより赤くハッチングされたリング状 の部分が除去され,基材のニッケル基超合金が現出。
次にステップ2にて,ニッケル基超合 金にファイバレーザを円回転させて照射し加工することで,ニッケル基超合金の黄色くハッチングされた箇所が除去され,
TBC/ニッケル基超合金の丸孔あけ加工が完了。

ガスタービンの高温化においては,高温化に耐えうる新規材料の開発ならびに,
タービン部材 の特性向上と高度化した翼設計に基づく複雑な構造を実現するための製造技術の開発が不可 欠。
)総合研究所におけるそれら技術開発の取組みを記載したでつ。
開発した材料,製造技術に対して,その有用性,有効性の検証を実施しており,最新 技術の一部は既にガスタービンに適用されているでつ。
高温化していけばいくほど、材料の耐熱性の検証が大事になるでつなぁ~
最近、麺類多いなぁ~とか思いつつ、明太子たっぷり載せた
ご飯が食べたいタケスィがHP更新したでつ!
http://eritakecy1029.jimdo.com/
更なる高効率化を実現するた めには,タービン部材の特性向上と高度化した翼設計に基づく複雑な構造を実現するための製 造技術の開発が不可欠。
ガスタービンの高温化実現に向けた材料・製造技術と して,合金開発・鋳造技術,コーティング技術,溶接補修技術および冷却孔加工技術に関する開発状況を報告するでつ。

世界的なエネルギー需要は中国,インドなどのアジアを中心に近年著しく増加してて,2035 年の世界エネルギー消費は
2010 年時と比して約 1.5 倍に増加すると予測されているでつ。
エネルギ ー自給率が 10%に満たない我が国においてはエネルギーの有効活用ならびに環境負荷の低減 が急務。
とりわけ,現在日本の電源構成の約9割を火力発電が占めてて,その発電効率 向上への取り組みが求められているでつ。
発電効率は主機であるガスタービンの高温化に依存すると ころが大きく,1980 年代初頭から,高 温・高効率化および大容量化の開発を進めてきたでつ。
図1(1)にタービン入口温度の上昇と適用材料・技術の推移を示すでつ。

1984 年にタービン入口ガス 温度が 1100℃級のD形ガスタービンを開発し,以降,1989 年には 1350℃級のF形,
1997 年には 1500℃級のG形を,更に,2011 年には 1600℃級のJ形ガスタービンを開発)。
J形ガスタービ ンの開発においては先進遮熱コーティングや冷却・空力技術等,2004 年度から開始された国家プロジェクト研究である“1700℃級ガスタービン要素技術開発”に
おける開発成果も活用されてい るでつ(図2)。

ガスタービンの高温化においては,高温化に耐えうる新規材料の開発ならびに,タービン部材 の特性向上と高度化した翼設計に基づく
複雑な構造を実現するための製造技術の開発が不可欠。
その取り組みについて③以降に示すでつ!
タービン翼材料開発は高温環境下での使用に耐えうる高強度ニッケル基超合金としてこれまで MGA1400,MGA1400DS ならびに MGA2400 を開発し,製品に適用。
タービン翼向 けの超合金は,鋳造方法により普通鋳造合金,一方向凝固合金,単結晶合金に分類されるでつが,
これらの合金は普通鋳造合金(MGA1400,MGA2400)および一方向凝固合金(MGA1400DS)と して使用されているでつ。
単結晶合金は材料強度上不利となる結晶粒界を含まず,また粒界強化を 考慮せずに合金組成の最適化が行えることから
,最も高強度な合金となっているでつ。
但し,鋳造時 に生じる鋳造欠陥等による強度低下の影響が大きいことから,製造技術の確立が重要
。
特 に産業用ガスタービンのタービン翼は航空機エンジン用のタービン翼に比べ体格が大きいため に,より製造が難しくなっているでつ。
総合研究所では 1700℃級ガスタービンの実現を目指し,これまで物質・材料 研究機構(NIMS)と共同で単結晶翼向けの超耐熱材料開発研究を実施。
材料開発にあ たっては,材料の高温強度特性を確保するだけでなく,欠陥の無い良好な単結晶組織が得られ る鋳造技術の開発が不可欠。
また素材コスト,鋳造コスト等の経済性も同時に満足する必要。
さらに,高温強度特性については,クリープ強度,熱疲労強度,耐酸化性といった材料 特性を全て確保する必要があり,
特にクリープ強度と熱疲労強度を両立させることは技術的にハードルが高い課題。
NIMS にて開発された合金設計プログラムを活用して組成決定した 試作合金の評価を行うとともに,熱疲労強度を中心に特性予測データベースの充足を行ったでつ。
これら取り組みを通して,クリープ強度と熱疲労強度のどちらについても良好な特性を有する単結 晶合金である MGA1700 を開発(図3)。

高強度単結晶合金は一般的に高価な元素であるレ ニウム等のレアメタルを含有しているが,本合金はレニウムを含有せず高強度を実現した画期的な合金。
鋳造技術 上記材料開発に加え,方向凝固翼(一方向凝固翼と単結晶翼の総称)において発生しうる各 種鋳造欠陥(図4)を予測して,
鋳造条件最適化及び品質の向上を図るための鋳造シミュレーション 技術を開発(図5)。
(a) 異結晶発生危険度予測 異結晶は鋳物底部で発生させた結晶が下部から上部へ向けて一方向に成長する過程にお いて,
凝固途中で新たな結晶核が発生,成長するもので,鋳物各部位の凝固時温度勾配と結 晶成長速度のバランスが崩れた時に発生するので,
凝固伝熱解析によりこれらパラメータを評 価する事で発生傾向を予測できるでつ。
(b) 結晶成長予測 単結晶翼の鋳造においては鋳型底部の結晶生成・成長とセレクタでの結晶選択を正常に進 行させるため,
より厳密な条件設定が必要であるが,当該部の結晶成長状況についても同時 に計算予測可能。
(c) フレックル発生予測 方向凝固翼における鋳造欠陥であるフレックルは凝固時に生じる局所的な濃度分布に起因する溶湯の比重差により対流が発生し,
健全な結晶成長を阻害する事で発生するもので,凝 固中の溶湯密度変化,溶湯対流の障害となるデンドライトの間隔等を評価し,その発生危険度 を予測できるでつ。
(d) 再結晶発生予測 鋳物の凝固・冷却時に発生したひずみが限界値を超えて残留した場合,
これに起因して後 工程の熱処理時に再結晶が発生し,当該部の強度が低下するでつ。
そこで,鋳型,鋳物,その他 鋳型支持構造物を解析対象として,鋳造時の FEM 弾塑性解析を実施し,
算出した鋳造後の 残留塑性ひずみから再結晶発生危険度を予測する技術を開発。
これらシミュレーション技術を駆使して,鋳型形状設計,鋳造条件を決定し,MGA1700 合金を
用いた大型単結晶翼の試作を行ったでつ(図6)。
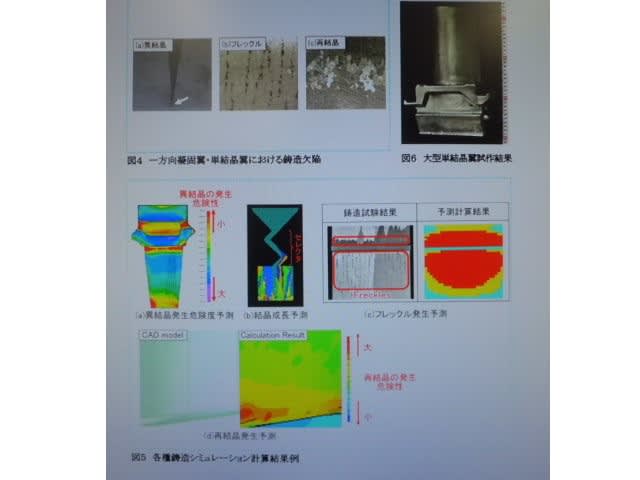
試作翼に顕著な結晶の倒れや,鋳造欠陥の発生 は認められず,健全な単結晶翼が鋳造できる事を確認。
遮熱コーティング技術は、 図1に示したように,ガスタービン入口温度は超合金の耐熱温度の上昇に比べはるかに速い速 度で上昇しているでつ。
これまで,冷却技術とコーティング技術の向上によって,この急速な高温化に 対応してきており,最新の 1600℃級J形ガスタービンには,
上述の通り国家プロジェクト研究で開発された先進遮熱コーティング(以下 TBC, Thermal Barrier Coating)が採用いるでつ。
以下に その先進 TBC の材料開発と施工技術について記載するでつ。
先進 TBC 材料開発は、材料組成の開発にあたっては,総合研究所で開発された,電子構造に基づく 材料計算システムを用いて,
低熱伝導で高温安定性に優れる候補材を選定した。選定された材 料組成で焼結体を作製し,熱伝導率と高温安定性を測定したところ,熱伝導率については従来 材である YSZ(イットリア部分安定化ジルコニア)よりも低く,高温安定性については,高温環境で も有害な単斜晶の発生を抑制できる候補材を見出すことに成功したでつ(図7)。
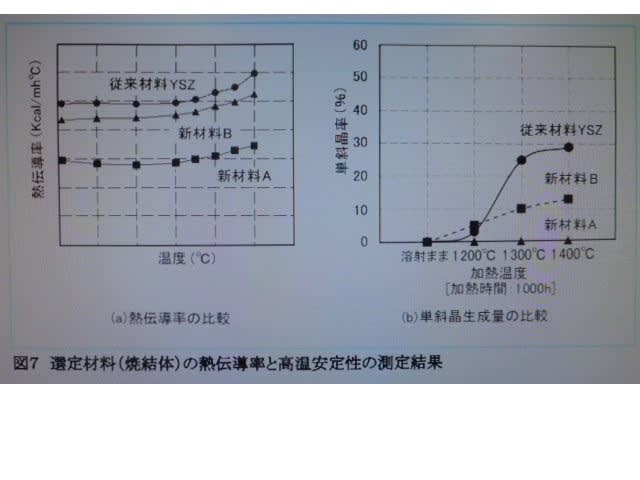
TBC は溶射によって施工され,皮膜中にミクロな気孔を導入することで焼結体よりもさらに熱伝 導率の低いコーティングを形成。
だけど過剰な気孔の導入は,高温・高流速の実機環境下で は,早期にはく離を生じさせたり,エロージョンによる減耗を招き,遮熱効果そのものを喪失させる 可能性があるでつ。
従って,材料組成の開発に次いで,溶射条件の最適化を含めた成膜技術の開発 が重要。
皮膜としての熱サイクル耐久性は,図8(a)に示すレーザ熱サイクル試験によって 評価し,このとき温度計測を併せて実施することで熱伝導率の評価も行うでつ。
また,実機環境を模擬 した高温・高流速下でエローダントを皮膜に衝突させることが出来る高温エロージョン試験装置 (図8(b))を開発し,皮膜のエロージョン特性を評価しているでつ。

これらの評価装置を用いながら,次 節で述べる溶射条件を最適化しつつ皮膜としての材料開発を行い,要求される信頼性・遮熱性を満足する皮膜を得ることができたどでつ。
施工技術は前述の通り,溶射条件を変えると皮膜のミクロ組織は変化し,それに伴って皮膜の遮熱性・信 頼性は大きく変わる。
そのため,各溶射条件に対してプラズマフレームがどのように変化し,溶射 粒子がどのように基材に衝突・偏平化していくかを高速度カメラで観察し,
粒子が過度に飛散し 皮膜中に欠陥を生じることが無いように,溶射条件の最適化を実施(図9)。

こうして決定した溶射条件で施工された皮膜は,試験片のような単純形状であれば良好な性能 を示すでつが,タービン翼は端壁を有し3次元的な曲率を持つため,
全面を試験片と同様な理想的か つ均質な皮膜とするのは容易ではないでつ。
そのためには,溶射ガンを持つロボットアームとタービン 翼を固定しているターンテーブルを同期させながら干渉を避けて,試験片と同様の条件で施工し
なければならないでつ。
このような複雑なロボットプログラミングを組むために,CAD を用いたロボットシ ミュレーション技術が用いられているでつ(図 10)。

このようにして作り込まれたロボットプログラミングを用いて先進 TBC を実翼施工した後,付帯 試験片での熱サイクル試験や実翼切断調査により,
実翼における皮膜の健全性を確認。
この ようにJ形ガスタービン向けの先進 TBC 技術を完成させ,2015 年 10 月までに約 13 万時間の累計 運転時間を経験し良好な運転結果を得ているでつ。
高温部材の溶接補修技術運転中に損傷を受けたタービン翼は,補修を行いながら設計寿命まで継続使用されているでつ。
効率的なガスタービンの運用を行うためには,新たに開発された単結晶合金である MGA1700 に
ついても現行の普通鋳造合金や一方向凝固合金と同様に,補修技術の確立が不可欠。
高温強度に優れる単結晶合金の特性を補修後も確保するためには,補修部も単結晶化する必要が有るでつが,
一般的な補修工法である溶接を適用した場合,溶接金属を単結晶組織とすることが 難しく,異結晶が発生した場合は加工除去等の対策を行わなければならないでつ。
溶接補修部を 単結晶化できる溶接条件を検討するツールとして,数値シミュレーションを用いて溶接ビード形状を予測し,
ビード内で単結晶組織が形成される領域を可視化する手法を検討。
溶接手法は,母材との希釈を制御し易い LMD(Laser Metal Deposition,レーザ粉体肉盛溶 接)を対象とし,
解析は汎用熱流体解析ソフト(Flow-3D)にて行ったでつ。
LMD の概略を図 11 に示すでつ。
溶接材料には,母材に用いられる MGA1700 合金と同一成分の粉末を用いたでつ。
初めに解析 により溶接ビード形状の予測を行い,実際に LMD により形成したビード形状と比較することで解 析の妥当性を調査。
図 12 に解析モデル及び解析結果の一例を示すでつ。
解析では,レーザ照 射位置に溶接材料を供給し,レーザが移動することで溶接ビードが形成されるでつ。
解析結果において青色部は母材が溶融していない領域を,赤色部は完全に溶融した領域を,赤から青に変化する色は部分的に溶融したことを示しているでつ。
図 13 に解析及び LMD の溶接ビード断面の比較を示すでつ。
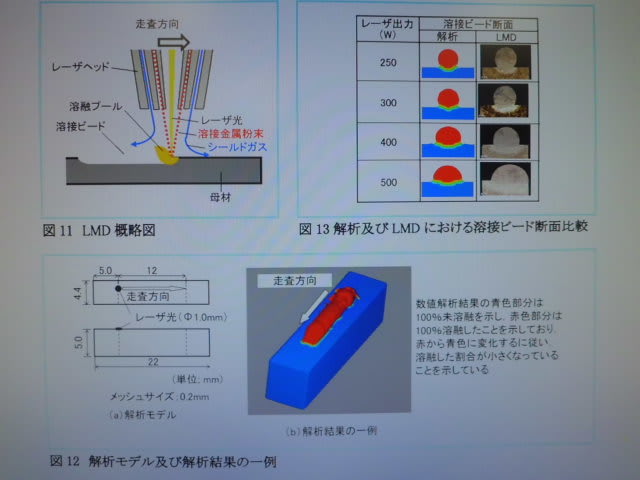
両者は良い一致を示していることが判るでつ。
溶接金属を母材と同じ結晶方位の単結晶組織とするには,溶融部境界における凝固時温度 勾配G(Temperature gradient)と
凝固速度R(Rate of solidification)を適切に制御し G/R を大きく する必要が有るでつ。
そこで,解析により LMD 条件を変化させた場合の各位置におけるG及びRを求め,評価を行ったでつ。
具体的には母材との融合界面で生成した単結晶組織が正常に成長できる領域を G/R 値の大きさから予測。
各溶接条件における健全成長領域の高さを予測した結果を図14 に示すでつ。
図中で,右下部の施工条件域は溶接入熱過少のため,また左上部の施工条件域 は溶接入熱過多のため,溶接施工が出来なかった領域でつ。
溶接金属が母材と同じ結晶方位 の単結晶組織となる領域を大きくするには,レーザ出力を大きく,
かつ溶接速度を小さくする傾向に制御すれば良いことが明らかとなったでつ。 解析により求めた適正条件を用いて LMD 施工を行ったでつ。
溶接ビード断面組織写真を図 15 に示すでつ。
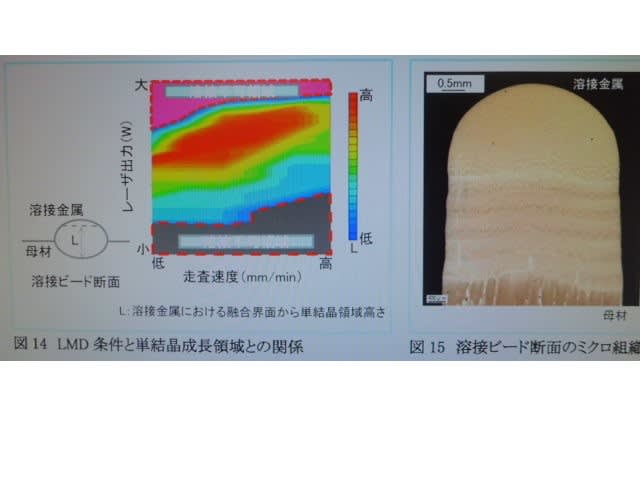
溶接金属部分は健全な単結晶組織を呈しており,良好な結果が得られていることが確認されたでつ。
現行の孔あけ加工はプロセス タービン翼は,高温環境下での使用に耐えるため,高強度ニッケル基超合金の表面に TBC が 施工されているでつ。
タービン翼の冷却孔(形状:丸孔,シェイプト孔)は,現状ニッケル基超合金に放 電加工等により孔あけを行い,溶射にて TBC をコーティングした後,
TBC には機械的孔あけを実 施して製造されてて,ニッケル基超合金と TBC は異なる手法で加工されるでつ。
こりは,放電加工 では,非導電性材料の TBC の加工が困難なため。
今後,ガスタービンコンバインドサイク ルのさらなる高効率化に向け,高温耐久性を向上させるべく
TBCの厚膜化,冷却効率向上のた めの冷却孔小径化が進むことが予想されるでつが,現行プロセスでは,TBC 溶射施工時に冷却孔が
閉塞するなど,製造が困難になると予測されるでつ
。
この課題を解決するため,TBC をコーティングし た後に,TBC とニッケル基超合金を一貫加工できる孔あけ加工法の開発が必要
。
冷却孔の主な形状には丸孔形状とシェイプト孔形状があるでつが,本開発では,レーザを用いた TBC/ニッケル基超合金一貫加工法の要素検証として,
より簡単な形状である丸孔を対象とし,薄 板の試験片(ニッケル基超合金:約1mm)を模擬材として用いて,孔あけ検証試験を実施。
短パルスレーザ/ファイバレーザによる2段階加工は レーザ加工は,非導電性材料である TBC およびニッケル基超合金の両者の加工が可能なため,
TBC/ニッケル基超合金の一貫加工に適した加工方法)。
ファイバレーザのような高出 力レーザを用いたレーザ熱加工は,微小な領域にエネルギーを集光させることで,加工対象を溶 融・蒸発させて加工する手法であり,高速加工に適する反面,エネルギー密度が高いため,加工 対象によっては十分な加工品質を維持する事が困難。
TBC は熱影響を受やすいため,フ ァイバレーザによる熱加工では,加工品質の維持が困難だったでつ。
こりに対して,短パルスレー ザはパルス幅が フェムト秒~ナノ秒 と熱加工で用いられる高出力レーザ(ミリ秒~連続波)に比 べてパルス幅が非常に短く,
熱影響を抑制した高品質な非熱加工が可能な利点を有するが,熱 加工で用いるレーザと比べて出力が低く,十分な加工速度を得ることが困難。
表1に短 パルスレーザとファイバレーザの特徴を示すでつ。
それぞれのレーザ発振器の特長を生かし,TBC 孔 あけに対しては,非熱加工により高品質加工が可能な短パルスレーザを適用し,
ニッケル基超合 金に対しては高速加工が可能なファイバレーザを用いる2段階加工方法を開発(図16)。

2段階加工 方法で用いる光学系には,高速高品質加工に適した独自技術であるプリズム ローテータを用いたでつ。
本開発では2段階加工の有効性を検証するため,より簡単な丸孔形状を対象として,加工試験 を行った。TBC/ニッケル基超合金の2段階加工方法を示すでつ(図 17)。

はじめにステップ1にて, TBC に短パルスレーザを円回転させて照射し加工する。これにより赤くハッチングされたリング状 の部分が除去され,基材のニッケル基超合金が現出。
次にステップ2にて,ニッケル基超合 金にファイバレーザを円回転させて照射し加工することで,ニッケル基超合金の黄色くハッチングされた箇所が除去され,
TBC/ニッケル基超合金の丸孔あけ加工が完了。

ガスタービンの高温化においては,高温化に耐えうる新規材料の開発ならびに,
タービン部材 の特性向上と高度化した翼設計に基づく複雑な構造を実現するための製造技術の開発が不可 欠。
)総合研究所におけるそれら技術開発の取組みを記載したでつ。
開発した材料,製造技術に対して,その有用性,有効性の検証を実施しており,最新 技術の一部は既にガスタービンに適用されているでつ。
高温化していけばいくほど、材料の耐熱性の検証が大事になるでつなぁ~
最近、麺類多いなぁ~とか思いつつ、明太子たっぷり載せた
ご飯が食べたいタケスィがHP更新したでつ!
http://eritakecy1029.jimdo.com/