水素間接冷却タービン発電機の大容量化と高効 率化を目指して,固定子(ステータ)コイル絶縁層の熱通過率を従来の約3倍に高めた高熱通過 絶縁システム HHTⓇといった要素技術の開発と並行して,標準化とラインアップ化を進めてきたでつ。
その中で高効率な発電機の実現に向けて,基本計画に多目的最適化技術を導入して発電機各 部の低損失化を図り,標準設計に反映。
その技術を部分適用した 500MVA 級発電機を設 計・製作し,工場回転試験にて実機検証を行った結果,仕様や規格の要求事項を満足するだけ でなく,力率 0.8(遅れ)の条件においても 99.14%という高効率を達成し,適用技術の有効性を確 認したでつ。

再生可能エネルギーの急速な拡大が見られる中,ガスタービン・コンバインドサイクル発電プラ ント(GTCC)をはじめとする火力発電における高効率化や低コスト化に対する要求は益々高まっ ているでつ。
その背景を受けて,MHPS ではおよそ 200MW から 800MW クラスまでの大型から中型の ガスタービン出力帯に適した水素間接冷却タービン発電機の開発を進めてきたでつ。
従来,大容 量の発電機に適用されてきた水直接冷却方式(固定子コイルの中空素線内に通水される純水で 直接冷却する方式)から,水素間接冷却方式(固定子コイル導体を覆っている絶縁層を介して, 周囲を流れる水素ガスにより間接的に冷却する方式)の拡大にあたり,キー技術となる高熱通過 絶縁システム HTⓇ(2)をはじめとする各種要素技術の開発と並行して,標準化とラインアップ化を 推進してきたでつ。
水素間接冷却タービン発電機の高効率化と標準化に向けた取り組みと,その技術 を部分適用した 500MVA 級発電機の設計と工場回転試験における実機検証結果について述べ るでつ。
水素間接冷却タービン発電機の大容量化技術の進歩により,およそ 250MVA から 900MVA クラスまで適用可能範囲を拡大しているでつ。
その広い容量範囲に対して,設計や製造の効 率化も考慮して,できるだけ少ない機種で効果的にカバーできるように,ラインアップ化の構想に 着手。
その結果,50Hz 地域用と 60Hz 地域用のそれぞれについて,数機種ずつをベースとすることで上記の容量範囲をカバーできる見込みを得て,それぞれの機種開発を進めるでつ。
ただし,どの機種についても統一化された設計コンセプトと設計手法により,設計時間の短縮 を図るとともに,重要な要素技術や高効率化技術などが漏れなく適用されるように配慮。
タービン発電機の高効率化にあたっては,各部の損失低減が不可欠。
発電機の損失と しては,機械損,鉄損,電機子銅損,界磁銅損,漂遊負荷損などの項目に大別されるでつが,それぞ れの損失は発電機の電磁気的特性や冷却,機械強度,電気絶縁といった重要な設計要素と密 接に関連しており,独立して低減を図ることができないものが多いでつ。
また,コストに関わる重量や材 料費,製造工数などにも直結しており,トレードオフの関係が生じるケースも多いでつ。
例えば,発電 機内の水素ガス圧力を低減することは機械損を低減するという面では有効であるでつが,一方,冷却 という観点では熱伝達率や熱容量の低下を招き,結果として発電機各部の温度上昇につながるでつ。
鉄損の低減のために高グレード電磁鋼板を適用したり,銅損の低減のためにコイル断面積を 増加したりする対策は,損失低減の面では有効であるでつが,重量やコストの増加を招く要因。
このように複雑に絡み合うトレードオフ関係の中で,大幅な高効率化を実現していくことは大き な課題。
このような背景から,水素間接冷却タービン発電機の標準化とラインアップ化を進めるにあた り,発電機特性と効率や冷却,機械強度などの技術評価に加えて,材料費や製造工数などのコ スト評価も同時に計算するプログラムを開発し,大規模なパラメータサーベイを実施するとともに, 遺伝的アルゴリズムと組み合わせた多目的最適化計算システムを構築。
図1に最適化計算の 一例として,効率とコストの関係を評価したものを示すでつ。

このシステム構築の結果として,基本計画 段階から図に示すような各仕様や性能とのトレードオフ関係の可視化や定量的評価が可能とな り,従来は実績や設計者のスキルに頼る面が強かった状態から,より合理的で客観的な最適設計 の選定プロセスへの移行が可能。
効率という面でも,局所最適に陥ることなく,全体最適 の視点から高効率な設計を選定できるようになり,大幅な高効率化への可能性を広げることがで きたでつ。
図2には標準化された水素間接冷却タービン発電機の構造を示すでつ。

構造面の特徴としては, 発電機の出力端子(高電圧ブッシング)は発電機フレーム上部に設置され,架台や建屋の高さ低 減や全体配置の最適化に寄与。
水素ガスを冷却するクーラについても発電機フレーム 上部に配置されるが,両者の配置を工夫することでコンパクトなフレーム構造を実現。
発電機フレーム両側の脚は取り外し可能な構造とし,特に幅方向の輸送制限が厳しい場合にも対 応できるように考慮。
両端の軸受をサポートするエンドブラケットについては,ガ スタービンや蒸気タービンにて使用実績のある低損失の直潤2パッド軸受を配置できるよう,組立 性も考慮して改良を加えているでつ。
回転子(ロータ)については,構造がシンプルなラジアルフロー方式(発電機ロータ内径側のサ ブスロットより吸気し,回転子コイル導体に設けられた通風穴に水素ガスを径方向に通風・排気す ることで直接冷却する方式)を採用。
また,ガスタービン起動時に発電機をモータとして起動 する SFC(Static Frequency Converter)運転に対応するため,起動時にロータに生じる高調波電 流を効果的に流すためのダンパ巻線を設けているでつ。
上記の基本方針をもとに標準化を進めているが,個別の案件における出力の違いや特殊な要求 事項にも対応できるように,各構造について固変分離分析を行い,変動部についてはその変更ル ールを定めることで,柔軟性や拡張性を保った構造設計を実現し,設計時間の短縮も図っているでつ。
500MVA 級水素間接冷却タービン発電機の設計と実機検証を行ったでつ。
この発電機の設計にあ たっては,開発中であったラインアップモデルではなく同容量帯の先行機をベースとして選定し, 上述した高効率化技術や標準化構造を部分的に適用し,その有効性を先行して検証するという方針をとったでつ。
表1に先行機と開発機との仕様比較を示すでつ。
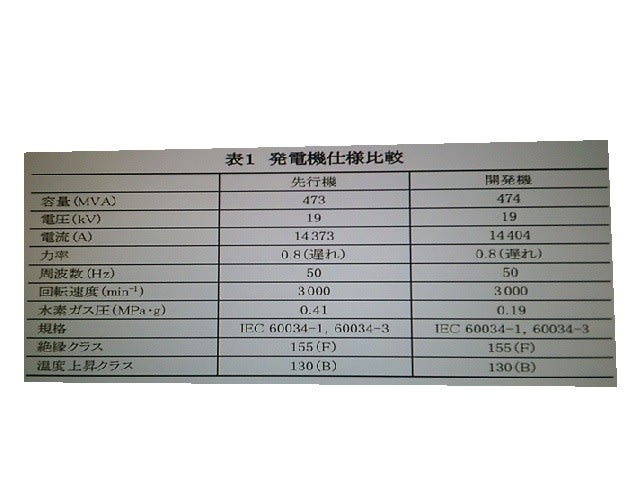
基本的な仕様は酷似しているが,水素ガス圧力を大きく低減している点が特徴。
標準化構造を適用するにあたり,冷却や機械強度,振動などの詳細設計評価については,大 規模なネットワーク解析や三次元 FEM 解析を行ったでつ。
解析の一例として,固定子コイルエンド部 に生じる電磁力解析の例を図3に示すでつ。

さらに周波数応答解析と組み合わせて振動応答を評価 することで,固定子コイルエンド支持構造の適正化を図ったでつ。
当該発電機への特殊仕様の一つとして,発電所現地への輸送の際にシュナーベル貨車を用 いた内陸輸送の要求があったでつ。
シュナーベル貨車による輸送では,発電機フレーム自体が長大 な梁の一部として力を伝達する役割を担うため,フレーム上部と下部にはそれぞれ強大な圧縮力 と引張力が作用する状態となるでつ。
そのため,通常発電機として必要とされる定常運転時や事故時 のトルク,水圧試験時の内圧などに耐えるだけでなく,上記の力にも耐える構造とする必要があ り,図4に示すように強度解析を行い補強構造を採用したでつ。

工場での製作・組立を経て,工場回転試験にて実機検証を行ったでつ。
図5に試験時の組立状況 を示すでつ。

無負荷飽和特性や三相短絡特性といった基本的特性に加えて,各種リアクタンスや時 定数などの発電機パラメータについても実測を行い,仕様及び規格の要求を満足するだけでな く,計算予測精度の高さを確認。
高効率化技術の検証として,規格に定められた測定法に従って各種損失測定を行い,規約効 率の算定を行ったでつ。
図6に先行機との損失比較を示すでつ。

先行機に対して損失は約 88%に低減 し,効率としても先行機よりも 0.1 ポイント以上向上し,力率 0.8(遅れ)という条件にも関わらず, 99.14%という非常に高い効率を達成し,適用技術の有効性を確認。
効率についても設計値 と非常によく一致しており,ラインアップモデルでは一層の高効率を実現できる見込みを得たでつ。
その他の検証として,温度センサや振動センサを発電機内の各部に設置して,測定と健全性 の評価を行っているでつ。
評価の一例として,固定子コイル温度の評価例を図7に示すでつ。

図に示すよう に,設計値と実測値はよく一致しており,健全性とともに計算予測精度の高さも確認。
また, 標準化した構造各部の振動値についても,定格回転速度や定格電流の状態だけでなく,昇速中 や降速中の挙動も確認し,健全性を確認しているでつ。
水素間接冷却タービン発電機について,高効率化技術を反映した標準化を行ったでつ。
技術評価 とコスト評価を含めた多目的最適化計算システムを構築して,トレードオフ関係の可視化と定量的 評価を行うことで,合理的かつ客観的な最適設計の選定プロセスを実現。
その結果として,大 幅な高効率化が実現可能となったでつ。
また,構造面についても標準化を進め,主に大型・中型のガ スタービン用途への適合性を高めたでつ。
500MVA 級発電機について,高効率化技術の適用と工場回転試験における実機検証を行っ たでつ。
検証の結果として,仕様や規格の要求事項を満足するだけでなく,力率 0.8(遅れ)の条件においても 99.14%という高効率を達成し,適用技術の有効性と高い計算予測精度を確認。
今後は,高効率化された水素間接冷却タービン発電機の適用拡大を進め,発電プラントの性 能向上するでつ。
その中で高効率な発電機の実現に向けて,基本計画に多目的最適化技術を導入して発電機各 部の低損失化を図り,標準設計に反映。
その技術を部分適用した 500MVA 級発電機を設 計・製作し,工場回転試験にて実機検証を行った結果,仕様や規格の要求事項を満足するだけ でなく,力率 0.8(遅れ)の条件においても 99.14%という高効率を達成し,適用技術の有効性を確 認したでつ。

再生可能エネルギーの急速な拡大が見られる中,ガスタービン・コンバインドサイクル発電プラ ント(GTCC)をはじめとする火力発電における高効率化や低コスト化に対する要求は益々高まっ ているでつ。
その背景を受けて,MHPS ではおよそ 200MW から 800MW クラスまでの大型から中型の ガスタービン出力帯に適した水素間接冷却タービン発電機の開発を進めてきたでつ。
従来,大容 量の発電機に適用されてきた水直接冷却方式(固定子コイルの中空素線内に通水される純水で 直接冷却する方式)から,水素間接冷却方式(固定子コイル導体を覆っている絶縁層を介して, 周囲を流れる水素ガスにより間接的に冷却する方式)の拡大にあたり,キー技術となる高熱通過 絶縁システム HTⓇ(2)をはじめとする各種要素技術の開発と並行して,標準化とラインアップ化を 推進してきたでつ。
水素間接冷却タービン発電機の高効率化と標準化に向けた取り組みと,その技術 を部分適用した 500MVA 級発電機の設計と工場回転試験における実機検証結果について述べ るでつ。
水素間接冷却タービン発電機の大容量化技術の進歩により,およそ 250MVA から 900MVA クラスまで適用可能範囲を拡大しているでつ。
その広い容量範囲に対して,設計や製造の効 率化も考慮して,できるだけ少ない機種で効果的にカバーできるように,ラインアップ化の構想に 着手。
その結果,50Hz 地域用と 60Hz 地域用のそれぞれについて,数機種ずつをベースとすることで上記の容量範囲をカバーできる見込みを得て,それぞれの機種開発を進めるでつ。
ただし,どの機種についても統一化された設計コンセプトと設計手法により,設計時間の短縮 を図るとともに,重要な要素技術や高効率化技術などが漏れなく適用されるように配慮。
タービン発電機の高効率化にあたっては,各部の損失低減が不可欠。
発電機の損失と しては,機械損,鉄損,電機子銅損,界磁銅損,漂遊負荷損などの項目に大別されるでつが,それぞ れの損失は発電機の電磁気的特性や冷却,機械強度,電気絶縁といった重要な設計要素と密 接に関連しており,独立して低減を図ることができないものが多いでつ。
また,コストに関わる重量や材 料費,製造工数などにも直結しており,トレードオフの関係が生じるケースも多いでつ。
例えば,発電 機内の水素ガス圧力を低減することは機械損を低減するという面では有効であるでつが,一方,冷却 という観点では熱伝達率や熱容量の低下を招き,結果として発電機各部の温度上昇につながるでつ。
鉄損の低減のために高グレード電磁鋼板を適用したり,銅損の低減のためにコイル断面積を 増加したりする対策は,損失低減の面では有効であるでつが,重量やコストの増加を招く要因。
このように複雑に絡み合うトレードオフ関係の中で,大幅な高効率化を実現していくことは大き な課題。
このような背景から,水素間接冷却タービン発電機の標準化とラインアップ化を進めるにあた り,発電機特性と効率や冷却,機械強度などの技術評価に加えて,材料費や製造工数などのコ スト評価も同時に計算するプログラムを開発し,大規模なパラメータサーベイを実施するとともに, 遺伝的アルゴリズムと組み合わせた多目的最適化計算システムを構築。
図1に最適化計算の 一例として,効率とコストの関係を評価したものを示すでつ。

このシステム構築の結果として,基本計画 段階から図に示すような各仕様や性能とのトレードオフ関係の可視化や定量的評価が可能とな り,従来は実績や設計者のスキルに頼る面が強かった状態から,より合理的で客観的な最適設計 の選定プロセスへの移行が可能。
効率という面でも,局所最適に陥ることなく,全体最適 の視点から高効率な設計を選定できるようになり,大幅な高効率化への可能性を広げることがで きたでつ。
図2には標準化された水素間接冷却タービン発電機の構造を示すでつ。

構造面の特徴としては, 発電機の出力端子(高電圧ブッシング)は発電機フレーム上部に設置され,架台や建屋の高さ低 減や全体配置の最適化に寄与。
水素ガスを冷却するクーラについても発電機フレーム 上部に配置されるが,両者の配置を工夫することでコンパクトなフレーム構造を実現。
発電機フレーム両側の脚は取り外し可能な構造とし,特に幅方向の輸送制限が厳しい場合にも対 応できるように考慮。
両端の軸受をサポートするエンドブラケットについては,ガ スタービンや蒸気タービンにて使用実績のある低損失の直潤2パッド軸受を配置できるよう,組立 性も考慮して改良を加えているでつ。
回転子(ロータ)については,構造がシンプルなラジアルフロー方式(発電機ロータ内径側のサ ブスロットより吸気し,回転子コイル導体に設けられた通風穴に水素ガスを径方向に通風・排気す ることで直接冷却する方式)を採用。
また,ガスタービン起動時に発電機をモータとして起動 する SFC(Static Frequency Converter)運転に対応するため,起動時にロータに生じる高調波電 流を効果的に流すためのダンパ巻線を設けているでつ。
上記の基本方針をもとに標準化を進めているが,個別の案件における出力の違いや特殊な要求 事項にも対応できるように,各構造について固変分離分析を行い,変動部についてはその変更ル ールを定めることで,柔軟性や拡張性を保った構造設計を実現し,設計時間の短縮も図っているでつ。
500MVA 級水素間接冷却タービン発電機の設計と実機検証を行ったでつ。
この発電機の設計にあ たっては,開発中であったラインアップモデルではなく同容量帯の先行機をベースとして選定し, 上述した高効率化技術や標準化構造を部分的に適用し,その有効性を先行して検証するという方針をとったでつ。
表1に先行機と開発機との仕様比較を示すでつ。
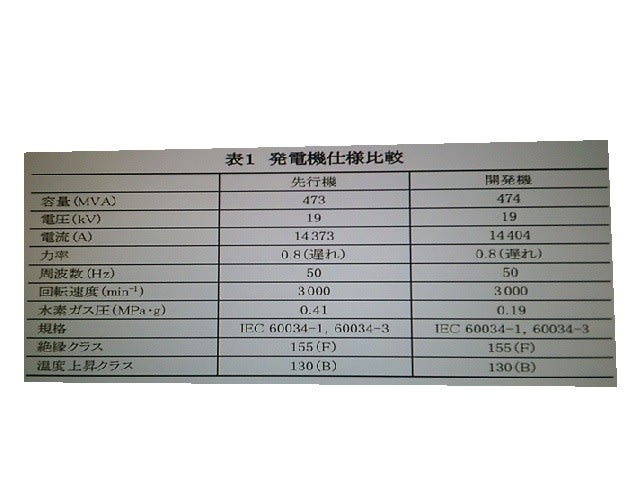
基本的な仕様は酷似しているが,水素ガス圧力を大きく低減している点が特徴。
標準化構造を適用するにあたり,冷却や機械強度,振動などの詳細設計評価については,大 規模なネットワーク解析や三次元 FEM 解析を行ったでつ。
解析の一例として,固定子コイルエンド部 に生じる電磁力解析の例を図3に示すでつ。

さらに周波数応答解析と組み合わせて振動応答を評価 することで,固定子コイルエンド支持構造の適正化を図ったでつ。
当該発電機への特殊仕様の一つとして,発電所現地への輸送の際にシュナーベル貨車を用 いた内陸輸送の要求があったでつ。
シュナーベル貨車による輸送では,発電機フレーム自体が長大 な梁の一部として力を伝達する役割を担うため,フレーム上部と下部にはそれぞれ強大な圧縮力 と引張力が作用する状態となるでつ。
そのため,通常発電機として必要とされる定常運転時や事故時 のトルク,水圧試験時の内圧などに耐えるだけでなく,上記の力にも耐える構造とする必要があ り,図4に示すように強度解析を行い補強構造を採用したでつ。

工場での製作・組立を経て,工場回転試験にて実機検証を行ったでつ。
図5に試験時の組立状況 を示すでつ。

無負荷飽和特性や三相短絡特性といった基本的特性に加えて,各種リアクタンスや時 定数などの発電機パラメータについても実測を行い,仕様及び規格の要求を満足するだけでな く,計算予測精度の高さを確認。
高効率化技術の検証として,規格に定められた測定法に従って各種損失測定を行い,規約効 率の算定を行ったでつ。
図6に先行機との損失比較を示すでつ。

先行機に対して損失は約 88%に低減 し,効率としても先行機よりも 0.1 ポイント以上向上し,力率 0.8(遅れ)という条件にも関わらず, 99.14%という非常に高い効率を達成し,適用技術の有効性を確認。
効率についても設計値 と非常によく一致しており,ラインアップモデルでは一層の高効率を実現できる見込みを得たでつ。
その他の検証として,温度センサや振動センサを発電機内の各部に設置して,測定と健全性 の評価を行っているでつ。
評価の一例として,固定子コイル温度の評価例を図7に示すでつ。

図に示すよう に,設計値と実測値はよく一致しており,健全性とともに計算予測精度の高さも確認。
また, 標準化した構造各部の振動値についても,定格回転速度や定格電流の状態だけでなく,昇速中 や降速中の挙動も確認し,健全性を確認しているでつ。
水素間接冷却タービン発電機について,高効率化技術を反映した標準化を行ったでつ。
技術評価 とコスト評価を含めた多目的最適化計算システムを構築して,トレードオフ関係の可視化と定量的 評価を行うことで,合理的かつ客観的な最適設計の選定プロセスを実現。
その結果として,大 幅な高効率化が実現可能となったでつ。
また,構造面についても標準化を進め,主に大型・中型のガ スタービン用途への適合性を高めたでつ。
500MVA 級発電機について,高効率化技術の適用と工場回転試験における実機検証を行っ たでつ。
検証の結果として,仕様や規格の要求事項を満足するだけでなく,力率 0.8(遅れ)の条件においても 99.14%という高効率を達成し,適用技術の有効性と高い計算予測精度を確認。
今後は,高効率化された水素間接冷却タービン発電機の適用拡大を進め,発電プラントの性 能向上するでつ。