ガスタービン複合発電は,再生可能エネルギーと共存する最もクリーンで経済的な火力発電設 備として,長期的な市場拡大が予想されるでつ。
現在,更なる高性能化を図るために 1700℃級ガ スタービンの技術開発を国家プロジェクトとして実施しており,開発した最新技術の一部は世界初の
1600℃級 J 形ガスタービンや次期高効率ガスタービンの開発に適用。
次世代 1700℃級ガスタービンへの適用を目指した技術の事例も含めた開発状況を報告するでつ。
温室効果ガスの排出を抑制するために革新的な技術開発が重要となってて,天然ガス利用 の高度化として超高温ガスタービンを用いた高効率火力発電技術の実用化を目指して,
1700℃級 ガスタービンの実用化に必要な要素技術開発を国家プロジェクトとして実施。
超高温ガス タービン実現のための技術開発ロードマップを図1に示すでつ。
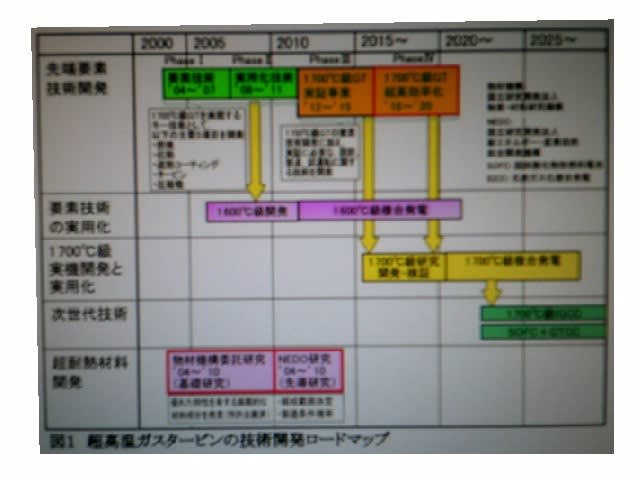
これまで,1700℃級ガスタービンの6要素(遮蔽コーティング,冷却技術,燃焼器,タービン,圧 縮機,耐熱材料)の技術開発を目指した PhaseⅠ(2004~2007 年)と,
実用化を目指した Phase Ⅱ,Ⅲ(2008~2015 年)で技術開発を行ってきたでつ。
本プロジェクトで得られた成果は,1600℃級J 形ガスタービンや次期高効率ガスタービンの開発に反映。
現在も PhaseⅣとして,図2に 示すように,実機開発と製造・試運転に向け開発要素を 13 項目に増やし,技術開発を継続して実施中。
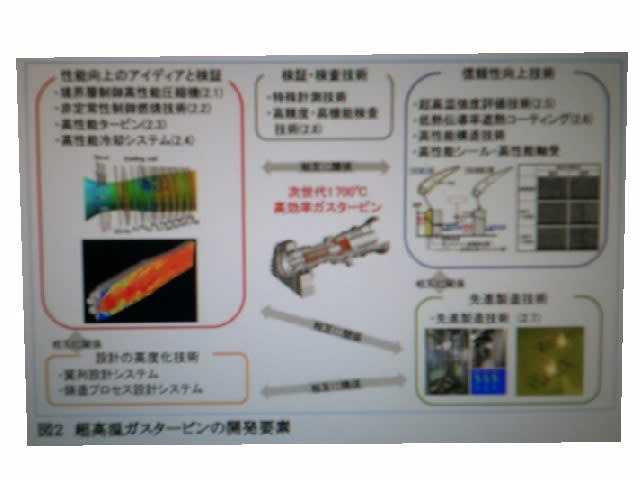
このうち,幾つかの事例(図2で示す8項目)について,開発の状況とこ れまでに得られた成果を報告するでつ。
境界層制御高性能圧縮機の開発 でつなぁ~
タービン入口温度の上昇によるサイクル効率向上のため,圧縮機には現状より圧力比を増加 することが求められるでつ。
これを,従来機並みの段数,軸長で実現するためには圧縮機翼列の高負 荷化が必要となり,効率の低下,サージマージンの低下,
起動安定性の低下に繋がる懸念があるでつ。
このため,実機形状の細部までを模擬した高精度の数値流動解析手法を開発し,圧力比の 増加に伴う境界層の発達を増大させるメカニズムの
把握とこれを制御するための改良設計案の検 討を進めているでつ。
さらに,実機のスケールモデル圧縮機を製作し,改良設計案の性能検証をする とともに数値流動解析の精度評価をして実機設計にフィードバックすることで,
より信頼性の高い 圧縮機の開発につなげているでつ。
図3は,圧縮機前方8段を模擬した試験装置による低サイクル(低回転)条件での圧縮機不安 定(サージ)点を検証した結果。
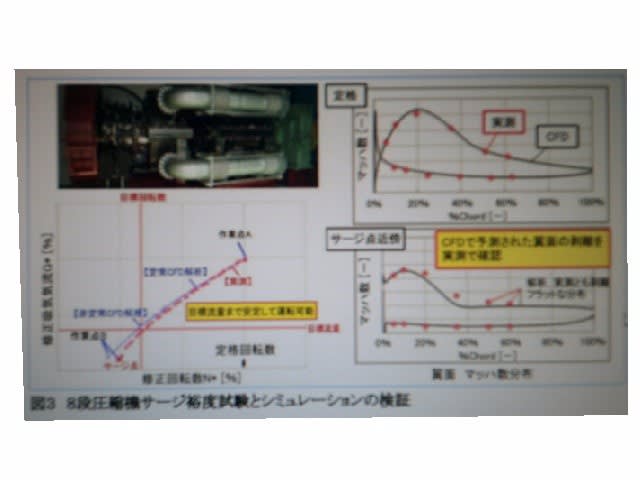
翼の失速箇所の形状変更により目標流量を予測どおり満 足することを示すでつ。
図4は起動時に発生する旋回失速の失速セル数とその圧力変動振幅を検証したもので,予測どおり安定した起動特性を得ることができたでつ。

これらの技術を活用して,さらに高性能・高信頼性のガスタービン圧縮機の開発を進めているでつ。
ガスタービン開発の競争が激化しており,ガスタービン高効率化のため,燃焼温度の高温化に 取り組んでいるでつ。
それに伴い,温度上昇とともに増大する NOx 排出量の低減が急務。
低 NOx 化に対しては希薄予混合燃焼方式が有効であるでつが,予混合燃焼では火炎位置が安 定せず,発熱変動等に起因した燃焼振動が発生する傾向があるでつ。
そのため,予混合燃焼器の開 発では,予混合ガスの希薄化,均一化による低 NOx 化に加え,燃焼振動の抑制も大きな設計課題。
これらの課題の対策のためには,実燃焼器内部の火炎の詳細な位置を把握し, 燃焼器設計に反映する必要があるでつが,高温高圧下の計測は困難であり,
これまで実機条件下の 燃焼器内部の状況は不明。
そこで,光学計測と大規模非定常数値解析による火炎位置 評価技術を開発。
図5に光学計測技術の概要を示すでつ。

本計測技術では,燃焼器壁面に設置した光学プローブに より火炎からの発光を集光し,光電子増倍管で検出することで
局所的な火炎の発熱量を推定することができるでつ。
さらに,プローブを複数設置することで燃焼器軸方向の発熱量の分布が計測可能。
今回,耐圧・耐熱性を持ったプローブを開発することで実機条件・実スケール燃焼器を 対象に火炎分布を特定することができたでつ。
それと平行して,Large Eddy Simulation(LES)を採用した大規模非定常数値解析技術を開発 。
本解析技術では,非定常解析の適用により高精度に火炎を予測することが可能となったこれらの技術により,図6の比較結果のように計測,
解析の二面から実機条件の火炎位置評価 が可能。
従来の定常解析結果は下流側でピークを示しているのに対し,今回開発した大 規模非定常解析手法では上流側でピークを示し,
計測値と良い一致を示し,精度良く予測でき ていることが検証できたでつ。
これらの技術は,低 NOx 燃焼器の開発に現在活用中。
排気ディフューザ(図7)は,タービン翼下流に位置し,タービン翼出口流速を減速させ圧力を 大気圧まで回復させる役割を有するでつ。

これにより,排気ディフューザの上流に位置するタービン最 終段動翼の出口静圧は大気圧よりも低い圧力となり,実質的なタービン圧力比(膨張比)及び出力が
増加することでタービン効率を向上させる効果があるでつ。
そこで,更なる排気ディフュー ザ性能向上のため,先進大規模解析技術を適用したタービン・ディフューザ一体最適化により改良コンセプトを検討し,
排気ディフューザ要素試験により定格負荷条件での性能向上効果を検証 (図8)。

だけど,特に流れの旋回成分(スワール角)が大きくなる低負荷条件では,ディフューザ内筒 (ID)に大規模な剥離が生じるために排気ディフューザ性能が大きく低下(図8)。
この課題に 対し,流動解析と試験による流れ場の分析結果から,この大規模剥離には,ストラット間流路の内 筒壁面(ID 壁面)近傍に現れる渦構造が関係していることを
明らかにしたでつ(図9)。
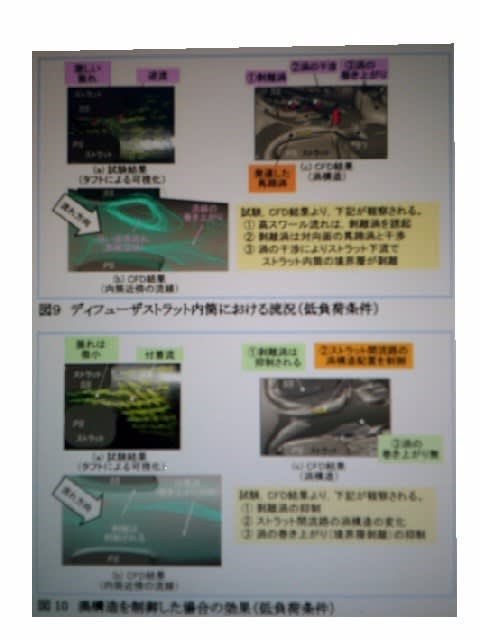
更にこの大規 模剥離は,同じ部分負荷条件であっても,ストラット間流路の渦構造を制御することにより効果的 に抑制できることを,流動解析及び試験で検証(図10)。
タービン翼前縁部にはシャワーヘッドフィルム孔と呼ばれる冷却構造があり,比較的多くの冷却 空気流量が使われており,空気流量削減の余地があるでつ。
当該部の局所冷却効率を 計測することで,冷却構造に応じて,より適切な冷却構造を採用し,冷却空気流量低減や性能向 上が可能。
そこで,実機ガスタービンの燃焼器及び一段静翼を模擬した試験リグ(図 11)を用いて,静翼 前縁部周りのフィルム効率分布を取得(図 12)。

今後,本計測結果を元に更なる冷却空気流 量の削減検討を進めていく予定。
1700℃級ガスタービンではメタル温度の上昇により,高温強度の観点から,既に適用されてい る DS 材(一方向凝固材:Directionally Soldified)や,
新たに SC 材(単結晶材:Single Crystal)の適 用が必要。
これらの材料は,鋳造時に結晶が特定の方向に成長している材料であり,強度 評価においては異方性を考慮する必要があるでつ。
一方,メタル温度の上昇とともに冷却が強化さ れ,特に冷却孔等の応力集中部では,高い応力が発生することから,信頼性が高く,なお且つ合 理的な熱疲労評価手法が求められるでつ。
これに対し,熱応力場での応力集中を模擬した試験片で の熱疲労試験(図 13)により,き裂発生寿命に対する結晶成長方向の影響や冷却孔の形状の影 響を確認しており(5),
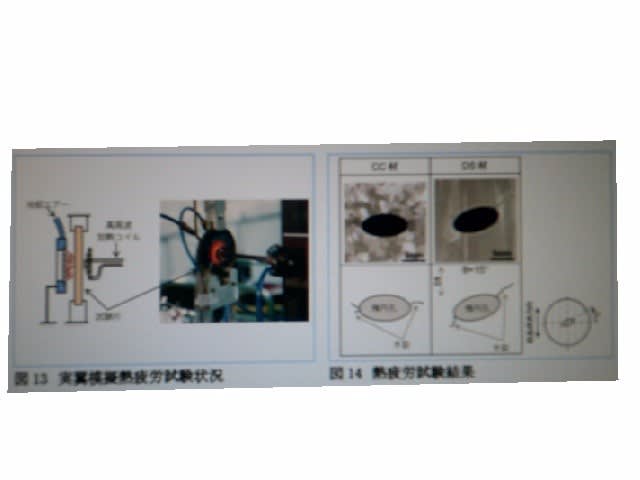
これらを熱疲労寿命評価手法へ反映する予定(図 14)。
そのほか,メタル温度が高い場合,材料強度の変化は避けられないため,このような高温下で も長時間の信頼性が要求されるでつ。
これに対しては,実機で高温長時間使用された場合を想定し た劣化模擬材での材料強度の確認や,運転後の劣化状態を定量的に評価する手法の開発を行っているでつ。
1700℃級ガスタービンの開発を目指して,材料開発・溶射プロセスパラメータの最適化・実翼 施工プログラム開発・実機検証を一貫して行い,
先進遮熱コーティング(以下 TBC, Thermal Barrier Coating)の開発し,更なる高性能化を実施。
これまで,電子構造に基づく材料計 算システムを用いて,低熱伝導で高温安定性に優れる候補材を机上検討し,その組成の焼結体 を試作・評価。
その結果,熱伝導率と高温安定性に優れる材料系を抽出したでつ。(図 15)。
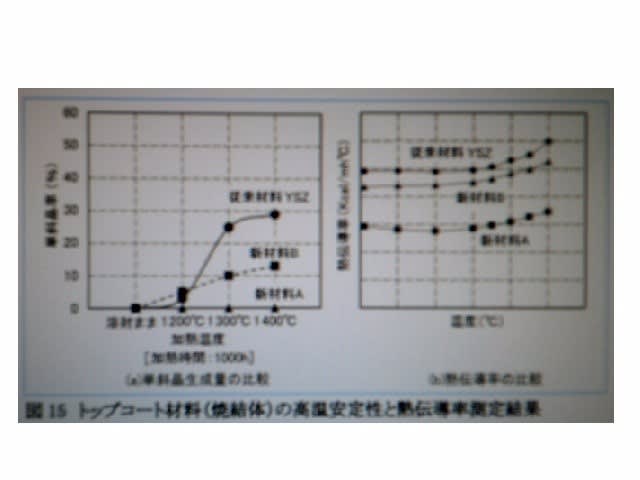
産業用ガスタービンに用いられる TBC は,一般的に溶射法によって成膜されるため,新規材 料を用いる場合,溶射プロセスパラメータの最適化が必要。
そこで,溶射中の粒子状態量 計測や付着状態のその場観察を行なうとともに,成膜した TBC の熱伝導率・剥離耐久性・耐エロ ージョン性・耐酸化性等の皮膜性能評価に供し,
相関性を把握するとともに,さらに,プロセス改良に反映することで,目標の皮膜性能を満足させたでつ。
なお,タービン高温部品は複雑な3次元形 状であるため,翼面全面を試験片と同様な理想的かつ均質な皮膜とするのは容易ではないでつ。
そ のため,事前に CAD を用いたロボットシミュレーションを行うことで,理想的な施工プログラムを得 た後に,実翼施工プログラムに反映し,切断調査により確認する手法を採用。
これにより,短 期間で,かつ良好な皮膜を実翼に施工する技術を開発。
開発した先進 TBC は実証発電設 備で長期検証し,試験片と同等の高い遮熱性と信頼性を有することを確認。
高温部材の溶接補修技術は、 運転中に損傷を受けたタービン翼は,補修を行いながら設計寿命まで継続使用されており, 新開発の単結晶合金であるMGA1700 の補修技術の確立が不可欠。
そこで,溶接補修 部を単結晶化できる溶接条件を検討するツールとして,数値シミュレーションを用いて溶接ビード形状を予測し,ビード内で単結晶組織が形成される領域を可視化する手法を検討。
溶接手法は,母材との希釈を制御し易い LMD(Laser Metal Deposition,レーザ粉体肉盛溶接; 図 17)を用い,解析は汎用熱流体解析ソフト(Flow-3D)にて行ったでつ。
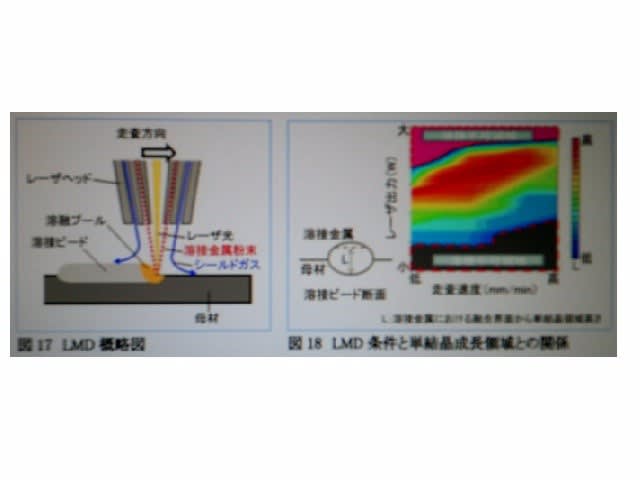
溶接材料には,MGA1700 合金母材と同一成分の粉末を用いたでつ。
溶接金属を母材と同じ結晶方位の単結晶組織とするには,溶融部境界における凝固時温 度勾配Gと凝固速度Rを適切に制御し G/R を大きくする必要。
そこで,解析により,母材 との融合界面で生成した単結晶組織が正常に成長できる領域を G/R 値の大きさから予測。
各溶接条件における健全成長領域の高さの予測結果を図 18 に示すでつ。
図中で,右下部の 施工条件域は溶接入熱過少のため,また左上部の施工条件域は溶接入熱過多のため,溶接 施工ができなかった領域。
溶接金属が母材と同じ結晶方位の単結晶組織となる領域を 大きくするには,レーザ出力を大きく,かつ溶接速度を小さくする傾向に制御すれば良いことが明らかとなったでつ。
解析により求めた適正条件を用いて LMD 施工を行った場合のビード断面組織を図 19 に示 すでつ。
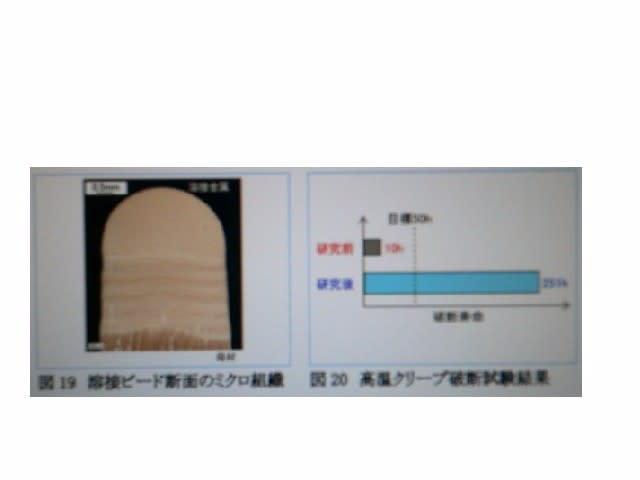
溶接金属部分は健全な単結晶組織を呈しており,良好な結果が得られていることが確認。
高温部材の 3D 積層造形技術 ガスタービン高温部品(動翼,静翼,分割環)の冷却空気量削減による母機性能向上を狙いとし,
現工法では不可能な複雑冷却構造の 3D 金属積層造形技術を開発。
課題の一 つである造形物の材料強度を確保するため,材料組成の調整と造形・熱処理プロセスの適正化に取り組み,
高温環境での 3D 金属積層造形物の要求強度を確保(図 20)
今後は,複 雑冷却構造の高精度造形技術の開発に取り組む計画。
タービン翼材料及び鋳造技術 物質・材料研究機構(NIMS)と共同で単結晶翼向けの超耐熱材料開発を行い,クリープ強度と熱疲労強度の
どちらも良好な特性を有する単結晶合金である MGA1700 を開発 (図 21)。

本合金は高価なレニウムを含有せず,高強度を実現した画期的な合金。
また,上記材料開発に加え,方向凝固翼(一方向凝固翼と単結晶翼の総称)の鋳造プロセ スに関する各種鋳造シミュレーション技術を開発(図 22)。
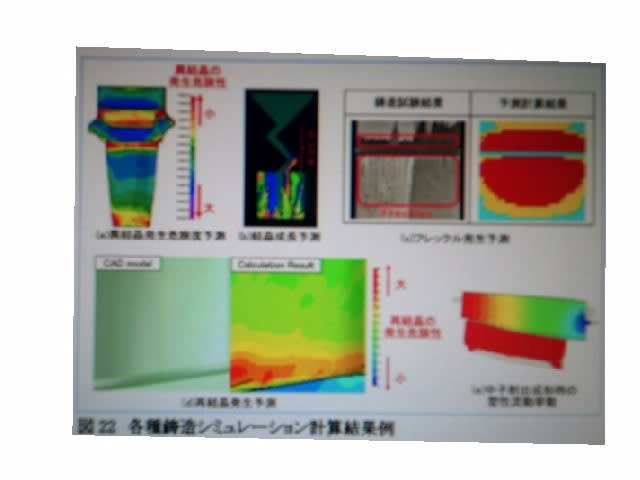
これらシミュレーション技術を駆 使することで,鋳造欠陥の予測だけでなく,中子射出成形時の塑性流動挙動等,各プロセスを 事前予測可能となり,
鋳造プロセス全体の条件最適化及び鋳物品質の向上を実現。
ワイヤレスセンシングにおける無線給電技術 高速回転中の動翼を振動計測するために歪みデータを無線で送信。
この計測・送信に 必要な電力を無線で受電できるモジュールを開発(図 23)。

前面のアンテナから高周波電 力を受け同じモジュール内の歪み計測アンプとデータ送信機へ直流電圧を供給。
電池交 換が不要となり連続計測が可能。
高周波送電のため電磁誘導型より長距離でも送電でき ることが特長。
翼内表面の欠陥検出技術 ガスタービン翼の欠陥検査において,冷却通路面側などの見えない位置の欠陥検出技術は,タービン翼の信頼性確保の観点で重要な技術。
このため,翼外表面側から翼内 表面の欠陥を精度良く検査する手法として,超音波ビームの集束性を向上させたマトリクスアレ イ UT プローブを開発(図 24)。
実翼の検査では,三次元走査スキャナにUTプローブを装 着し,翼面を走査させることで内表面側の欠陥検査を迅速に行うことが可能(図 25)。
国立研究開発法人新エネルギー・産業技術総合開発機構(NEDO) の助成事業として実施中の高効率ガスタービン技術実証事業(1700℃級ガスタービンの超高効 率化)の一部であり,
実用化に必要な要素技術の開発と実証を目指した実機適用技術の開発を 実施中。
性能向上に関する各要素技術や,高温・高圧の過酷な条件での信頼性,製造や 検査に関する技術を開発。
技術検討や検証を経て,有効性が確認された最新技術の一 部は 1600℃級J形ガスタービンや次期高効率ガスタービンの開発に適用。
同時に,得ら れた長期運用データを研究内容に反映することにより,開発した技術の信頼性向上を図っているでつ。
これらの最新の複合発電技術の普及を通じて,火力発電所の CO2 削減に大きく貢献するでつなぁ~
現在,更なる高性能化を図るために 1700℃級ガ スタービンの技術開発を国家プロジェクトとして実施しており,開発した最新技術の一部は世界初の
1600℃級 J 形ガスタービンや次期高効率ガスタービンの開発に適用。
次世代 1700℃級ガスタービンへの適用を目指した技術の事例も含めた開発状況を報告するでつ。
温室効果ガスの排出を抑制するために革新的な技術開発が重要となってて,天然ガス利用 の高度化として超高温ガスタービンを用いた高効率火力発電技術の実用化を目指して,
1700℃級 ガスタービンの実用化に必要な要素技術開発を国家プロジェクトとして実施。
超高温ガス タービン実現のための技術開発ロードマップを図1に示すでつ。
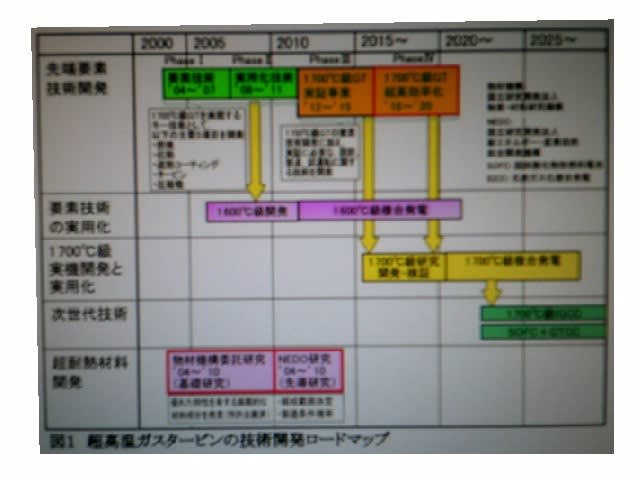
これまで,1700℃級ガスタービンの6要素(遮蔽コーティング,冷却技術,燃焼器,タービン,圧 縮機,耐熱材料)の技術開発を目指した PhaseⅠ(2004~2007 年)と,
実用化を目指した Phase Ⅱ,Ⅲ(2008~2015 年)で技術開発を行ってきたでつ。
本プロジェクトで得られた成果は,1600℃級J 形ガスタービンや次期高効率ガスタービンの開発に反映。
現在も PhaseⅣとして,図2に 示すように,実機開発と製造・試運転に向け開発要素を 13 項目に増やし,技術開発を継続して実施中。
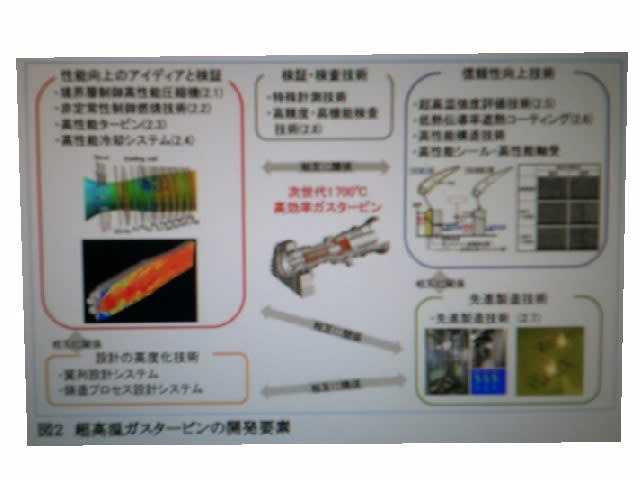
このうち,幾つかの事例(図2で示す8項目)について,開発の状況とこ れまでに得られた成果を報告するでつ。
境界層制御高性能圧縮機の開発 でつなぁ~
タービン入口温度の上昇によるサイクル効率向上のため,圧縮機には現状より圧力比を増加 することが求められるでつ。
これを,従来機並みの段数,軸長で実現するためには圧縮機翼列の高負 荷化が必要となり,効率の低下,サージマージンの低下,
起動安定性の低下に繋がる懸念があるでつ。
このため,実機形状の細部までを模擬した高精度の数値流動解析手法を開発し,圧力比の 増加に伴う境界層の発達を増大させるメカニズムの
把握とこれを制御するための改良設計案の検 討を進めているでつ。
さらに,実機のスケールモデル圧縮機を製作し,改良設計案の性能検証をする とともに数値流動解析の精度評価をして実機設計にフィードバックすることで,
より信頼性の高い 圧縮機の開発につなげているでつ。
図3は,圧縮機前方8段を模擬した試験装置による低サイクル(低回転)条件での圧縮機不安 定(サージ)点を検証した結果。
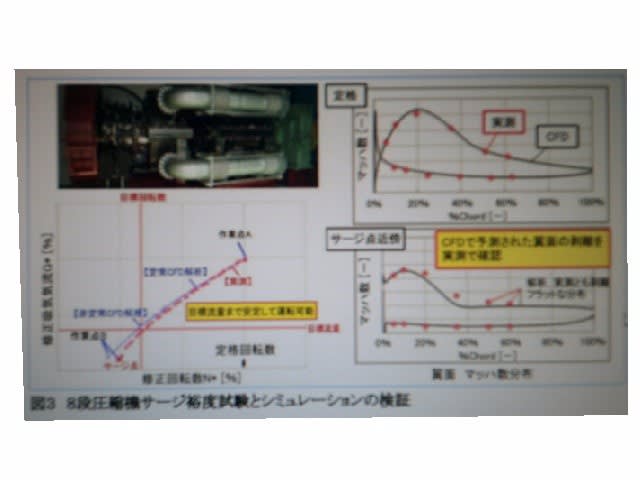
翼の失速箇所の形状変更により目標流量を予測どおり満 足することを示すでつ。
図4は起動時に発生する旋回失速の失速セル数とその圧力変動振幅を検証したもので,予測どおり安定した起動特性を得ることができたでつ。

これらの技術を活用して,さらに高性能・高信頼性のガスタービン圧縮機の開発を進めているでつ。
ガスタービン開発の競争が激化しており,ガスタービン高効率化のため,燃焼温度の高温化に 取り組んでいるでつ。
それに伴い,温度上昇とともに増大する NOx 排出量の低減が急務。
低 NOx 化に対しては希薄予混合燃焼方式が有効であるでつが,予混合燃焼では火炎位置が安 定せず,発熱変動等に起因した燃焼振動が発生する傾向があるでつ。
そのため,予混合燃焼器の開 発では,予混合ガスの希薄化,均一化による低 NOx 化に加え,燃焼振動の抑制も大きな設計課題。
これらの課題の対策のためには,実燃焼器内部の火炎の詳細な位置を把握し, 燃焼器設計に反映する必要があるでつが,高温高圧下の計測は困難であり,
これまで実機条件下の 燃焼器内部の状況は不明。
そこで,光学計測と大規模非定常数値解析による火炎位置 評価技術を開発。
図5に光学計測技術の概要を示すでつ。

本計測技術では,燃焼器壁面に設置した光学プローブに より火炎からの発光を集光し,光電子増倍管で検出することで
局所的な火炎の発熱量を推定することができるでつ。
さらに,プローブを複数設置することで燃焼器軸方向の発熱量の分布が計測可能。
今回,耐圧・耐熱性を持ったプローブを開発することで実機条件・実スケール燃焼器を 対象に火炎分布を特定することができたでつ。
それと平行して,Large Eddy Simulation(LES)を採用した大規模非定常数値解析技術を開発 。
本解析技術では,非定常解析の適用により高精度に火炎を予測することが可能となったこれらの技術により,図6の比較結果のように計測,
解析の二面から実機条件の火炎位置評価 が可能。
従来の定常解析結果は下流側でピークを示しているのに対し,今回開発した大 規模非定常解析手法では上流側でピークを示し,
計測値と良い一致を示し,精度良く予測でき ていることが検証できたでつ。
これらの技術は,低 NOx 燃焼器の開発に現在活用中。
排気ディフューザ(図7)は,タービン翼下流に位置し,タービン翼出口流速を減速させ圧力を 大気圧まで回復させる役割を有するでつ。

これにより,排気ディフューザの上流に位置するタービン最 終段動翼の出口静圧は大気圧よりも低い圧力となり,実質的なタービン圧力比(膨張比)及び出力が
増加することでタービン効率を向上させる効果があるでつ。
そこで,更なる排気ディフュー ザ性能向上のため,先進大規模解析技術を適用したタービン・ディフューザ一体最適化により改良コンセプトを検討し,
排気ディフューザ要素試験により定格負荷条件での性能向上効果を検証 (図8)。

だけど,特に流れの旋回成分(スワール角)が大きくなる低負荷条件では,ディフューザ内筒 (ID)に大規模な剥離が生じるために排気ディフューザ性能が大きく低下(図8)。
この課題に 対し,流動解析と試験による流れ場の分析結果から,この大規模剥離には,ストラット間流路の内 筒壁面(ID 壁面)近傍に現れる渦構造が関係していることを
明らかにしたでつ(図9)。
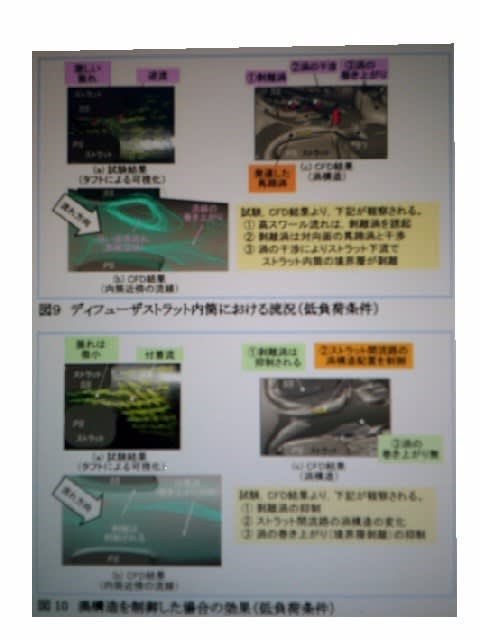
更にこの大規 模剥離は,同じ部分負荷条件であっても,ストラット間流路の渦構造を制御することにより効果的 に抑制できることを,流動解析及び試験で検証(図10)。
タービン翼前縁部にはシャワーヘッドフィルム孔と呼ばれる冷却構造があり,比較的多くの冷却 空気流量が使われており,空気流量削減の余地があるでつ。
当該部の局所冷却効率を 計測することで,冷却構造に応じて,より適切な冷却構造を採用し,冷却空気流量低減や性能向 上が可能。
そこで,実機ガスタービンの燃焼器及び一段静翼を模擬した試験リグ(図 11)を用いて,静翼 前縁部周りのフィルム効率分布を取得(図 12)。

今後,本計測結果を元に更なる冷却空気流 量の削減検討を進めていく予定。
1700℃級ガスタービンではメタル温度の上昇により,高温強度の観点から,既に適用されてい る DS 材(一方向凝固材:Directionally Soldified)や,
新たに SC 材(単結晶材:Single Crystal)の適 用が必要。
これらの材料は,鋳造時に結晶が特定の方向に成長している材料であり,強度 評価においては異方性を考慮する必要があるでつ。
一方,メタル温度の上昇とともに冷却が強化さ れ,特に冷却孔等の応力集中部では,高い応力が発生することから,信頼性が高く,なお且つ合 理的な熱疲労評価手法が求められるでつ。
これに対し,熱応力場での応力集中を模擬した試験片で の熱疲労試験(図 13)により,き裂発生寿命に対する結晶成長方向の影響や冷却孔の形状の影 響を確認しており(5),
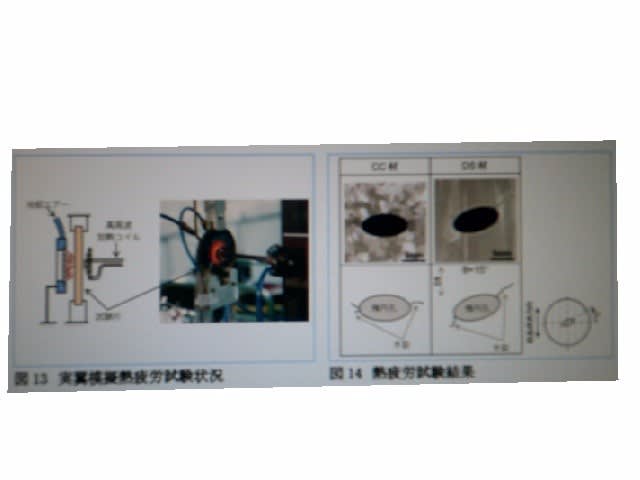
これらを熱疲労寿命評価手法へ反映する予定(図 14)。
そのほか,メタル温度が高い場合,材料強度の変化は避けられないため,このような高温下で も長時間の信頼性が要求されるでつ。
これに対しては,実機で高温長時間使用された場合を想定し た劣化模擬材での材料強度の確認や,運転後の劣化状態を定量的に評価する手法の開発を行っているでつ。
1700℃級ガスタービンの開発を目指して,材料開発・溶射プロセスパラメータの最適化・実翼 施工プログラム開発・実機検証を一貫して行い,
先進遮熱コーティング(以下 TBC, Thermal Barrier Coating)の開発し,更なる高性能化を実施。
これまで,電子構造に基づく材料計 算システムを用いて,低熱伝導で高温安定性に優れる候補材を机上検討し,その組成の焼結体 を試作・評価。
その結果,熱伝導率と高温安定性に優れる材料系を抽出したでつ。(図 15)。
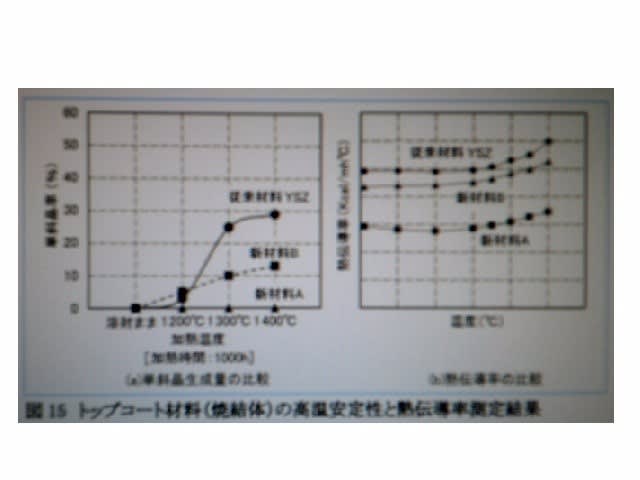
産業用ガスタービンに用いられる TBC は,一般的に溶射法によって成膜されるため,新規材 料を用いる場合,溶射プロセスパラメータの最適化が必要。
そこで,溶射中の粒子状態量 計測や付着状態のその場観察を行なうとともに,成膜した TBC の熱伝導率・剥離耐久性・耐エロ ージョン性・耐酸化性等の皮膜性能評価に供し,
相関性を把握するとともに,さらに,プロセス改良に反映することで,目標の皮膜性能を満足させたでつ。
なお,タービン高温部品は複雑な3次元形 状であるため,翼面全面を試験片と同様な理想的かつ均質な皮膜とするのは容易ではないでつ。
そ のため,事前に CAD を用いたロボットシミュレーションを行うことで,理想的な施工プログラムを得 た後に,実翼施工プログラムに反映し,切断調査により確認する手法を採用。
これにより,短 期間で,かつ良好な皮膜を実翼に施工する技術を開発。
開発した先進 TBC は実証発電設 備で長期検証し,試験片と同等の高い遮熱性と信頼性を有することを確認。
高温部材の溶接補修技術は、 運転中に損傷を受けたタービン翼は,補修を行いながら設計寿命まで継続使用されており, 新開発の単結晶合金であるMGA1700 の補修技術の確立が不可欠。
そこで,溶接補修 部を単結晶化できる溶接条件を検討するツールとして,数値シミュレーションを用いて溶接ビード形状を予測し,ビード内で単結晶組織が形成される領域を可視化する手法を検討。
溶接手法は,母材との希釈を制御し易い LMD(Laser Metal Deposition,レーザ粉体肉盛溶接; 図 17)を用い,解析は汎用熱流体解析ソフト(Flow-3D)にて行ったでつ。
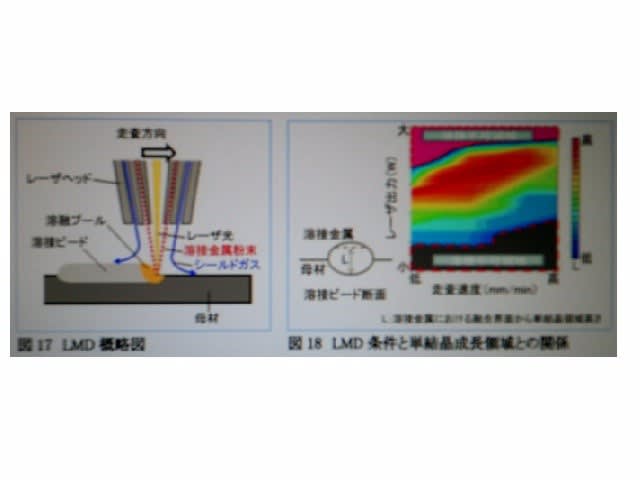
溶接材料には,MGA1700 合金母材と同一成分の粉末を用いたでつ。
溶接金属を母材と同じ結晶方位の単結晶組織とするには,溶融部境界における凝固時温 度勾配Gと凝固速度Rを適切に制御し G/R を大きくする必要。
そこで,解析により,母材 との融合界面で生成した単結晶組織が正常に成長できる領域を G/R 値の大きさから予測。
各溶接条件における健全成長領域の高さの予測結果を図 18 に示すでつ。
図中で,右下部の 施工条件域は溶接入熱過少のため,また左上部の施工条件域は溶接入熱過多のため,溶接 施工ができなかった領域。
溶接金属が母材と同じ結晶方位の単結晶組織となる領域を 大きくするには,レーザ出力を大きく,かつ溶接速度を小さくする傾向に制御すれば良いことが明らかとなったでつ。
解析により求めた適正条件を用いて LMD 施工を行った場合のビード断面組織を図 19 に示 すでつ。
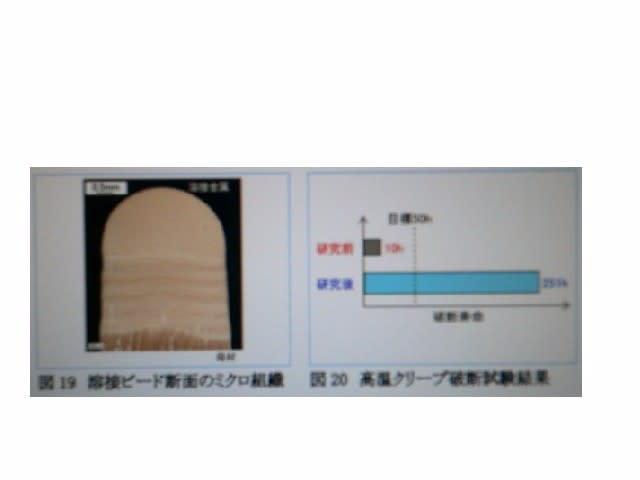
溶接金属部分は健全な単結晶組織を呈しており,良好な結果が得られていることが確認。
高温部材の 3D 積層造形技術 ガスタービン高温部品(動翼,静翼,分割環)の冷却空気量削減による母機性能向上を狙いとし,
現工法では不可能な複雑冷却構造の 3D 金属積層造形技術を開発。
課題の一 つである造形物の材料強度を確保するため,材料組成の調整と造形・熱処理プロセスの適正化に取り組み,
高温環境での 3D 金属積層造形物の要求強度を確保(図 20)
今後は,複 雑冷却構造の高精度造形技術の開発に取り組む計画。
タービン翼材料及び鋳造技術 物質・材料研究機構(NIMS)と共同で単結晶翼向けの超耐熱材料開発を行い,クリープ強度と熱疲労強度の
どちらも良好な特性を有する単結晶合金である MGA1700 を開発 (図 21)。

本合金は高価なレニウムを含有せず,高強度を実現した画期的な合金。
また,上記材料開発に加え,方向凝固翼(一方向凝固翼と単結晶翼の総称)の鋳造プロセ スに関する各種鋳造シミュレーション技術を開発(図 22)。
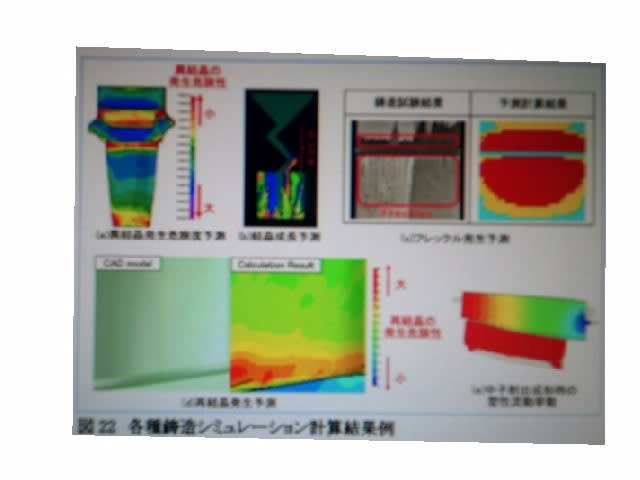
これらシミュレーション技術を駆 使することで,鋳造欠陥の予測だけでなく,中子射出成形時の塑性流動挙動等,各プロセスを 事前予測可能となり,
鋳造プロセス全体の条件最適化及び鋳物品質の向上を実現。
ワイヤレスセンシングにおける無線給電技術 高速回転中の動翼を振動計測するために歪みデータを無線で送信。
この計測・送信に 必要な電力を無線で受電できるモジュールを開発(図 23)。

前面のアンテナから高周波電 力を受け同じモジュール内の歪み計測アンプとデータ送信機へ直流電圧を供給。
電池交 換が不要となり連続計測が可能。
高周波送電のため電磁誘導型より長距離でも送電でき ることが特長。
翼内表面の欠陥検出技術 ガスタービン翼の欠陥検査において,冷却通路面側などの見えない位置の欠陥検出技術は,タービン翼の信頼性確保の観点で重要な技術。
このため,翼外表面側から翼内 表面の欠陥を精度良く検査する手法として,超音波ビームの集束性を向上させたマトリクスアレ イ UT プローブを開発(図 24)。
実翼の検査では,三次元走査スキャナにUTプローブを装 着し,翼面を走査させることで内表面側の欠陥検査を迅速に行うことが可能(図 25)。
国立研究開発法人新エネルギー・産業技術総合開発機構(NEDO) の助成事業として実施中の高効率ガスタービン技術実証事業(1700℃級ガスタービンの超高効 率化)の一部であり,
実用化に必要な要素技術の開発と実証を目指した実機適用技術の開発を 実施中。
性能向上に関する各要素技術や,高温・高圧の過酷な条件での信頼性,製造や 検査に関する技術を開発。
技術検討や検証を経て,有効性が確認された最新技術の一 部は 1600℃級J形ガスタービンや次期高効率ガスタービンの開発に適用。
同時に,得ら れた長期運用データを研究内容に反映することにより,開発した技術の信頼性向上を図っているでつ。
これらの最新の複合発電技術の普及を通じて,火力発電所の CO2 削減に大きく貢献するでつなぁ~