モノのインターネットと呼ばれるIoTに欠かせない技術として、センシングが注目。
製造業がデータ活用を進めるうえでも、センシングとIoTによる無線データ通信は不可欠な技術。
センシングは、センサーと呼ばれる検知器によって測定対象を計測し、定量的な情報を取得する技術。
こりは…
身の回りには数多くのセンサーが存在して、人間の感覚の代わりとなって働いているでつ。
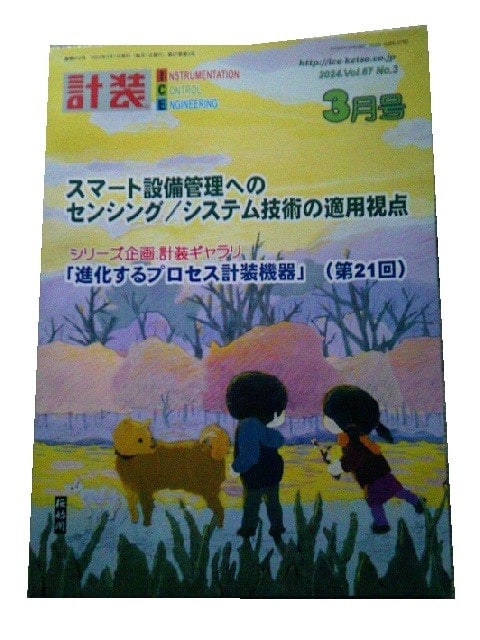
センシング技術は次の2種類に大きく分けられているでつ。
スマートセンシング対象物の近くにセンサーを設置して計測や検知を行う技術。
リモートセンシング対象物に触れることなく定量的な情報を取得する技術。
センシング技術は既にあらゆる分野で導入が進み、取得した情報をもとに機器を制御したり、
情報を分析してより付加価値の高い情報に変換したりして活用されているでつ。
製造業では上述したスマートセンシング技術の活用が効果的とされ、多くの企業が導入を進めているでつ。
センシング技術により、人間の感覚よりも高い精度で情報を取得でき製造業がデータを活用したDXを進めるうえで、
センシングとIoTによる無線データ通信は不可欠な技術。
前述のセンシング取り組み事例のように、実際にセンシング技術を積極的に活用している企業では、生産性や品質の向上、設備保全の効率化が進んでいるでつ。
目視検査での判別が難しい不具合を検知したり、検査を自動化してヒューマンエラーを削減したりすることで、品質向上が可能。
また、設備の加工条件を計測・分析することで、加工時の問題点を発見して品質改善に役立てることができるでつ。
さらに、センシング技術はトレーサビリティを確保するうえでも効果的。
製造条件や品質記録を紙で保管しておくと手間がかかるでつが、センシング技術で取得した情報をデータとして蓄積することで、すぐに必要な情報を検索できるでつ。
多くの製造現場では、設備の稼働状況を把握するために人による巡回・点検作業が行われているでつ。
保全担当者が工場内を巡回し、目視や手書きで点検していると相当な工数がかかってしまうるでつが、センシング技術を活用すれば省人化が可能。
設備にセンサーを取り付けて温度や電流などの情報を取得し、遠隔で監視できる仕組みを構築すれば、保全担当者がトラブルの発生をすぐに検知して対応できるようになるでつ。
さらに、昨今ではAIを用いた予知保全や故障予測も行われて、設備トラブルの発生を未然に防いで被害を最小限に抑えられるようになっているでつ。
センシング技術を活用すれば、作業の進捗状況や設備の稼働状況、製品や部品の所在地といったあらゆる情報をリアルタイムに把握できるようになるでつ。
生産の遅れを素早く検知して対処する、モノの滞留を削減してリードタイムを短縮する、といった形で生産性を向上させることが可能。
また、製造現場の見える化によって改善すべきポイントが明確になる点もメリット。
ポイントを絞った改善活動によって生産効率を高めていくことで、品質・原価・納期の向上につながるでつ。
をあげての積極的なDXの推進により、製造業の現場でもAIや生産管理システムなどの優れたツールの導入が求められているでつ。
それらのツールを有効に活用するにはセンシング技術によるデータ収集が不可欠ですが、製造業のデータ収集には幾つかの課題があり、DXの妨げとなっている状況。
例えば、設備から直接データを収集して生産管理などに活用したいと考えても、既存設備が古くてデータを収集できない。
実際に日本の製造現場では、10~20年以上前の設備が今でも現役で稼働しているケースが多く、そういった設備からデータを
うまく収集できずにIoT化が限定的になっている傾向にあるでつ。
新しい設備であればデータ収集する機能が標準で備わっていることもあるでつが、既存の古い設備からどうやってデータを
収集すればよいのかと悩んでいる方は多い。
また、設備から直接データを収集する方法がブラックボックス化してしまい、設備メーカーでなければ分からないというケースも見受けらるでつ。
特に中小企業の場合は設備のメンテナンスを担える生産技術担当者が少ないため、メーカーやベンダーに一任していて
自社では仕様がよく分からないという状況に陥りやすい傾向にあるでつ。
こういった悩みを抱えている企業におすすめの方法はセンサーの後付け。
昨今では既存設備に後付けして使用できるセンサーが数多くあり、古い設備からであっても必要なデータを収集・活用する仕組みを構築できるでつ。
設備メーカーに都度問い合わせることなくデータ収集を進められるため、自社の思う通りにIoT化やDXを進められるでつ。
製造現場には作業者や設備といったデータ収集の対象が数多く存在し、データの種類も多岐にわたるでつ。
それら全ての膨大なデータを収集しようとすると、膨大なコストがかかるだけでなく、せっかく収集したデータをうまく扱いきれない可能性もあるでつ。
また、データの種類だけでなく粒度にも注意しなければならばいでつ。
例えば、温度を計測する場合に、1℃単位で計測するのか、0.01℃単位で計測するのかではセンサーに求められる精度が大きく異なるでつ。
より詳細なデータを収集しておきたいと考える気持ちはよく分かるでつが、目的に見合わない過剰なデータを収集していても余計なコストがかかるだけ。
このように、センシング技術を活用してデータ収集を行う際には、やみくもにデータを集めるのではなく、自社の目的や用途に
応じて収集するデータの種類や粒度を選定する必要があるでつ。
どういったデータを収集すべきなのか、どの程度の粒度で収集すべきなのか、といったノウハウを持つ企業はまだまだ少ないのが現状。
センシング技術やIoTに精通した外部のベンダーに相談し、PDCAを回しながら少しずつデータ収集に取り組んでいくでつ。
製造業がデータを活用したDXを進めるうえで、センシングとIoTによる無線データ通信は不可欠な技術。
前述のセンシング取り組み事例のように、実際にセンシング技術を積極的に活用している企業では、生産性や品質の向上、設備保全の効率化が進んでいるでつ。
製造業向けIoTシステム」は、設備の機種・年式を問わず、センサーを後付けして既存設備からデータを収集できるでつ。
また、収集したデータは、グラフによる見える化によって分析・改善に役立てることが可能。
製造業がデータ活用を進めるうえでも、センシングとIoTによる無線データ通信は不可欠な技術。
センシングは、センサーと呼ばれる検知器によって測定対象を計測し、定量的な情報を取得する技術。
こりは…
身の回りには数多くのセンサーが存在して、人間の感覚の代わりとなって働いているでつ。
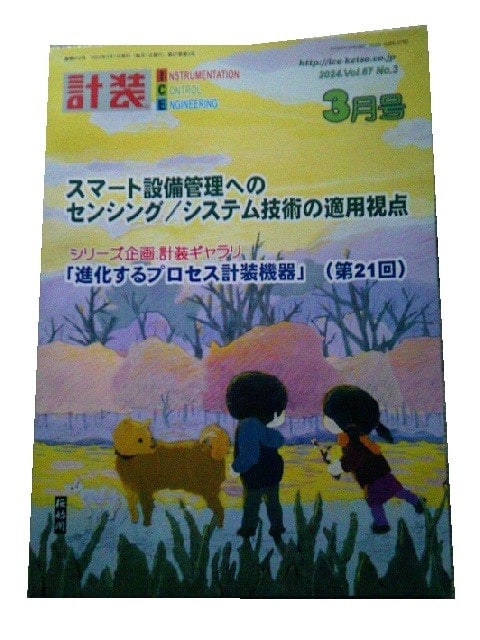
センシング技術は次の2種類に大きく分けられているでつ。
スマートセンシング対象物の近くにセンサーを設置して計測や検知を行う技術。
リモートセンシング対象物に触れることなく定量的な情報を取得する技術。
センシング技術は既にあらゆる分野で導入が進み、取得した情報をもとに機器を制御したり、
情報を分析してより付加価値の高い情報に変換したりして活用されているでつ。
製造業では上述したスマートセンシング技術の活用が効果的とされ、多くの企業が導入を進めているでつ。
センシング技術により、人間の感覚よりも高い精度で情報を取得でき製造業がデータを活用したDXを進めるうえで、
センシングとIoTによる無線データ通信は不可欠な技術。
前述のセンシング取り組み事例のように、実際にセンシング技術を積極的に活用している企業では、生産性や品質の向上、設備保全の効率化が進んでいるでつ。
目視検査での判別が難しい不具合を検知したり、検査を自動化してヒューマンエラーを削減したりすることで、品質向上が可能。
また、設備の加工条件を計測・分析することで、加工時の問題点を発見して品質改善に役立てることができるでつ。
さらに、センシング技術はトレーサビリティを確保するうえでも効果的。
製造条件や品質記録を紙で保管しておくと手間がかかるでつが、センシング技術で取得した情報をデータとして蓄積することで、すぐに必要な情報を検索できるでつ。
多くの製造現場では、設備の稼働状況を把握するために人による巡回・点検作業が行われているでつ。
保全担当者が工場内を巡回し、目視や手書きで点検していると相当な工数がかかってしまうるでつが、センシング技術を活用すれば省人化が可能。
設備にセンサーを取り付けて温度や電流などの情報を取得し、遠隔で監視できる仕組みを構築すれば、保全担当者がトラブルの発生をすぐに検知して対応できるようになるでつ。
さらに、昨今ではAIを用いた予知保全や故障予測も行われて、設備トラブルの発生を未然に防いで被害を最小限に抑えられるようになっているでつ。
センシング技術を活用すれば、作業の進捗状況や設備の稼働状況、製品や部品の所在地といったあらゆる情報をリアルタイムに把握できるようになるでつ。
生産の遅れを素早く検知して対処する、モノの滞留を削減してリードタイムを短縮する、といった形で生産性を向上させることが可能。
また、製造現場の見える化によって改善すべきポイントが明確になる点もメリット。
ポイントを絞った改善活動によって生産効率を高めていくことで、品質・原価・納期の向上につながるでつ。
をあげての積極的なDXの推進により、製造業の現場でもAIや生産管理システムなどの優れたツールの導入が求められているでつ。
それらのツールを有効に活用するにはセンシング技術によるデータ収集が不可欠ですが、製造業のデータ収集には幾つかの課題があり、DXの妨げとなっている状況。
例えば、設備から直接データを収集して生産管理などに活用したいと考えても、既存設備が古くてデータを収集できない。
実際に日本の製造現場では、10~20年以上前の設備が今でも現役で稼働しているケースが多く、そういった設備からデータを
うまく収集できずにIoT化が限定的になっている傾向にあるでつ。
新しい設備であればデータ収集する機能が標準で備わっていることもあるでつが、既存の古い設備からどうやってデータを
収集すればよいのかと悩んでいる方は多い。
また、設備から直接データを収集する方法がブラックボックス化してしまい、設備メーカーでなければ分からないというケースも見受けらるでつ。
特に中小企業の場合は設備のメンテナンスを担える生産技術担当者が少ないため、メーカーやベンダーに一任していて
自社では仕様がよく分からないという状況に陥りやすい傾向にあるでつ。
こういった悩みを抱えている企業におすすめの方法はセンサーの後付け。
昨今では既存設備に後付けして使用できるセンサーが数多くあり、古い設備からであっても必要なデータを収集・活用する仕組みを構築できるでつ。
設備メーカーに都度問い合わせることなくデータ収集を進められるため、自社の思う通りにIoT化やDXを進められるでつ。
製造現場には作業者や設備といったデータ収集の対象が数多く存在し、データの種類も多岐にわたるでつ。
それら全ての膨大なデータを収集しようとすると、膨大なコストがかかるだけでなく、せっかく収集したデータをうまく扱いきれない可能性もあるでつ。
また、データの種類だけでなく粒度にも注意しなければならばいでつ。
例えば、温度を計測する場合に、1℃単位で計測するのか、0.01℃単位で計測するのかではセンサーに求められる精度が大きく異なるでつ。
より詳細なデータを収集しておきたいと考える気持ちはよく分かるでつが、目的に見合わない過剰なデータを収集していても余計なコストがかかるだけ。
このように、センシング技術を活用してデータ収集を行う際には、やみくもにデータを集めるのではなく、自社の目的や用途に
応じて収集するデータの種類や粒度を選定する必要があるでつ。
どういったデータを収集すべきなのか、どの程度の粒度で収集すべきなのか、といったノウハウを持つ企業はまだまだ少ないのが現状。
センシング技術やIoTに精通した外部のベンダーに相談し、PDCAを回しながら少しずつデータ収集に取り組んでいくでつ。
製造業がデータを活用したDXを進めるうえで、センシングとIoTによる無線データ通信は不可欠な技術。
前述のセンシング取り組み事例のように、実際にセンシング技術を積極的に活用している企業では、生産性や品質の向上、設備保全の効率化が進んでいるでつ。
製造業向けIoTシステム」は、設備の機種・年式を問わず、センサーを後付けして既存設備からデータを収集できるでつ。
また、収集したデータは、グラフによる見える化によって分析・改善に役立てることが可能。