エレキベース1号、2号の詳細を書くつもりが、その前に3号、4号、5号がほぼ出来てしまいました。
1号2号の詳細はまた後程。

3号です。
テーマは「普通」
いきなり5弦ベースをセットネックで作ったりしてやや勇み足でしたので、よくあるような物をやってみようということです。
主なスペックは、
国産鬼胡桃1Pボディー、国産真樺1Pネック、EMGジャズベースピックアップ。
普通のトラスロッド、チタンブリッジ、純チタンナット、チタンノブ、鬼目ナットと六角レンチボルトのボルトオンネック。
カーボン製ネックの補強材。
普通を目指すものの、少しは独自性を目指してます。



4号です。
国産栗の1Pボディー、ウォールナットの1Pネック、突板貼りマッチングヘッド。
ピックアップ、マシンヘッド、ブリッジはguykerというメーカーの物で、中国ネットサイトで買ったものを試してます。
片効きのトラスロッド、カーボンのネック補強材入り。
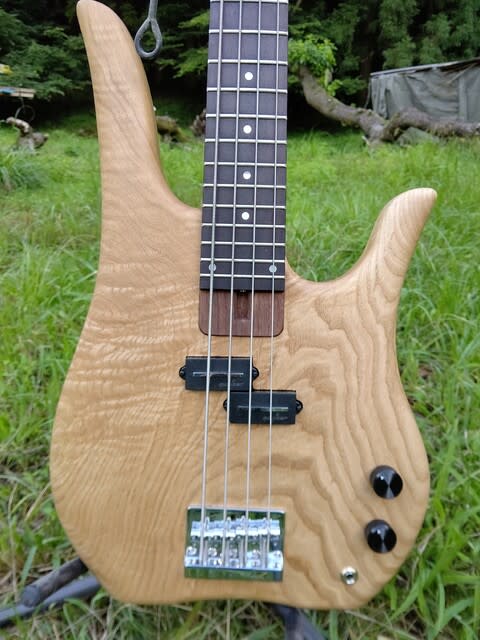

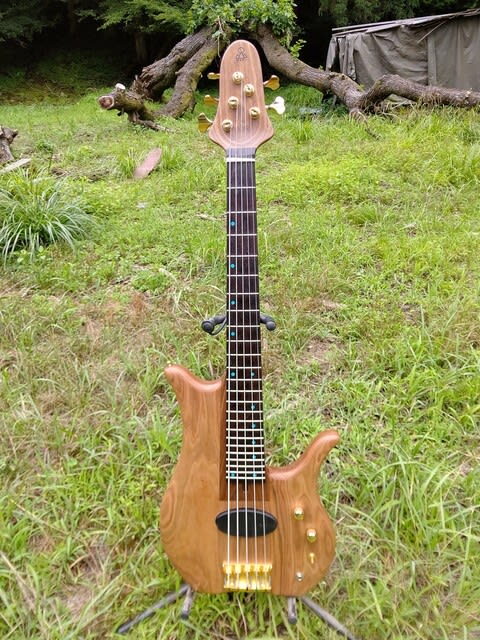
そして5号。これは力作。
国産の鬼胡桃2Pボディー、国産の槐(エンジュ)ネック。
30インチショートスケール、5弦で24フレット、チタンのネック補強材入り。
EADGCのHI-C仕様にしていますが、LowB仕様に変更も可能です。
シングルカッタウェイ、セットネック。

ネック材を指板よりも20mm程巾広にしてボディーとの接着面を増やす手の込んだ工作をしています。
前からの写真をよく見てもらうと、ネック材とボディー材の色の違いからそれがわかります。
Delanoというちょっと高価なピックアップ、シリーズ/スプリット/パラレル切り替えスイッチ。

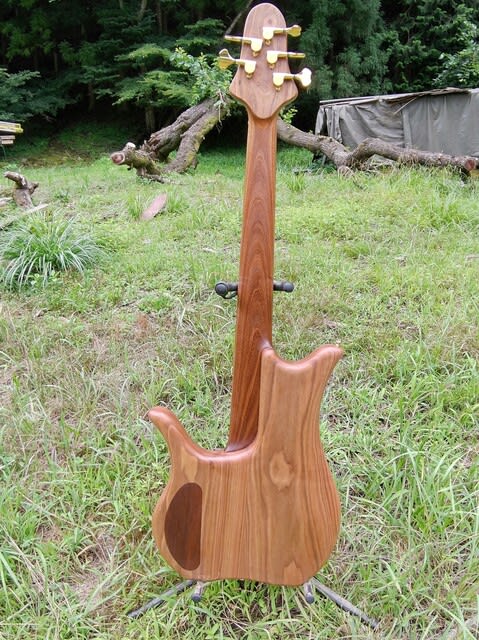
30インチのベースはよくある34インチより10cm弦長が短く低音の出音が懸念されましたが、ネックが半分ボディーに着いているシングルカッタウェイの効果なのか、なかなかしっかり低音も出て、高音もまたきれいに出ました。
生音も良いので、高級ピックアップのおかげだけではないと思います。
槐は国産材では最高のトーンウッドではないかと思っています。叩いたときの響きが素晴らしい。
ああでも他の製作者には知られたくない…
実はこれらの楽器はやっと弦を張ったところで、このましばらく置いてネックが安定してから最終調整をした後に、ちゃんとした楽器になります。
1号2号の詳細はまた後程。

3号です。
テーマは「普通」
いきなり5弦ベースをセットネックで作ったりしてやや勇み足でしたので、よくあるような物をやってみようということです。
主なスペックは、
国産鬼胡桃1Pボディー、国産真樺1Pネック、EMGジャズベースピックアップ。
普通のトラスロッド、チタンブリッジ、純チタンナット、チタンノブ、鬼目ナットと六角レンチボルトのボルトオンネック。
カーボン製ネックの補強材。
普通を目指すものの、少しは独自性を目指してます。



4号です。
国産栗の1Pボディー、ウォールナットの1Pネック、突板貼りマッチングヘッド。
ピックアップ、マシンヘッド、ブリッジはguykerというメーカーの物で、中国ネットサイトで買ったものを試してます。
片効きのトラスロッド、カーボンのネック補強材入り。
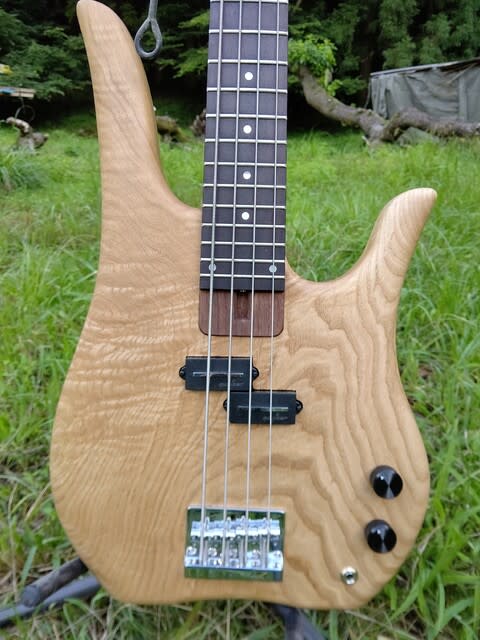

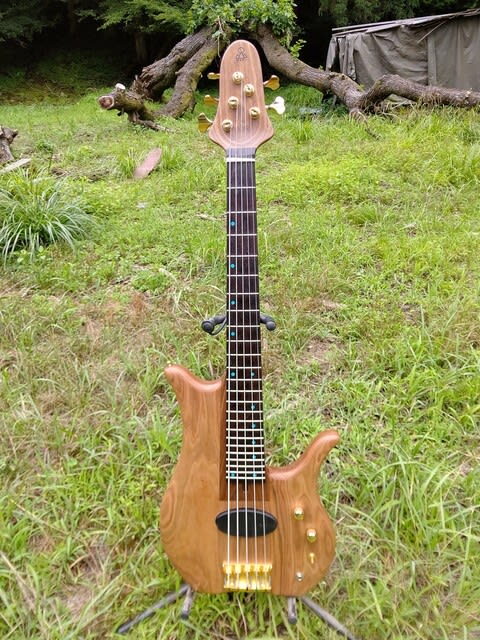
そして5号。これは力作。
国産の鬼胡桃2Pボディー、国産の槐(エンジュ)ネック。
30インチショートスケール、5弦で24フレット、チタンのネック補強材入り。
EADGCのHI-C仕様にしていますが、LowB仕様に変更も可能です。
シングルカッタウェイ、セットネック。

ネック材を指板よりも20mm程巾広にしてボディーとの接着面を増やす手の込んだ工作をしています。
前からの写真をよく見てもらうと、ネック材とボディー材の色の違いからそれがわかります。
Delanoというちょっと高価なピックアップ、シリーズ/スプリット/パラレル切り替えスイッチ。

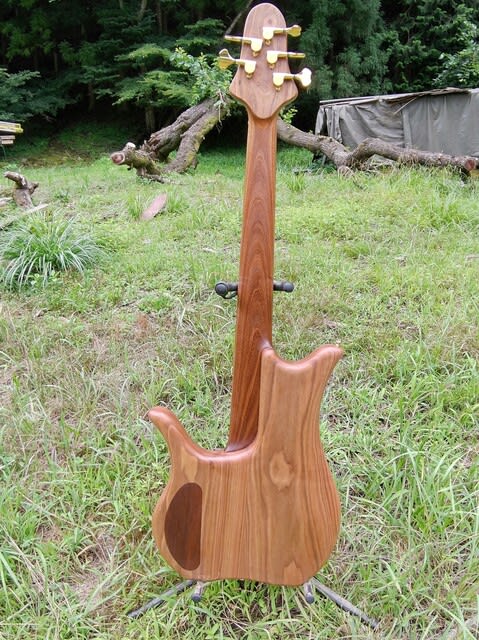
30インチのベースはよくある34インチより10cm弦長が短く低音の出音が懸念されましたが、ネックが半分ボディーに着いているシングルカッタウェイの効果なのか、なかなかしっかり低音も出て、高音もまたきれいに出ました。
生音も良いので、高級ピックアップのおかげだけではないと思います。
槐は国産材では最高のトーンウッドではないかと思っています。叩いたときの響きが素晴らしい。
ああでも他の製作者には知られたくない…
実はこれらの楽器はやっと弦を張ったところで、このましばらく置いてネックが安定してから最終調整をした後に、ちゃんとした楽器になります。