その一人が“kagayaki”さん.
家は車で10分,自転車でも10分.走ったら20分といったところ.
ご近所です.
加工関係の会社を経営されていますが,モノ作りが好きなためNCフライスや汎用旋盤を所有されているとのこと.
昔はフライス盤工だったそうですが,旋盤のマニアの匂いがします.
先日お話しした“逆ネジを切った延長パイプ”.
材料の鉄から外形切削したときにピカッとした美しい仕上げにならないといった話しをしたら色々とアドバイスをくれました.

どうも,私の切削速度はかなり遅いみたい.
切削にも理論があり,切削する材質やバイト(刃物)の材質によっても変わってきますが,一般的に切削条件は
次の公式で求められるとされています.
V(切削速度)=π(円周率)×D(直径mm)×N(主軸回転数)÷1000
並び替えると
N(主軸回転数)=1000×V(切削速度)÷π(円周率)×D(直径mm)
これらを元に実際に削ってみて最適な回転数を求めていくのですが,回転を上げると怖いので私は正直ゆっくり目で
回していました.
主軸を高速で回転させると『宇宙戦艦ヤマト』の波動エンジンの“フライホイールを始動”させるときと
同じ音がするんです.
(動画のタイムカウンター『0:10~0:12』あたりです. 宇宙戦艦ヤマトは何度見てもかっこええ.)
それからすると今の自分の回転数を5倍も10倍も上げないといけない.
おまけにバイト(チップ)の温度が“あっちっち”に上がった状態で切削しないといけないらしい.
なまじっか機械や刃物に優しいようにとして来たことが,切削には適していなかったということでした.
また,切削速度を上げると送り速度も上がるので短時間で加工が出来,時間単価を下げれるといった経営者視点での
話しをしていました.
たしか30代半ばのkagayakiさん.
厳しい現実社会で会社を経営しつつ,モノ作りを楽しむ若き獅子といった感じがしました.
ガレージに置いているツールを見る鋭い観察力と時折厳しいツッコミをするところが面白い方です.
興味がある方は事前にお知らせ頂ければセッティングいたします.
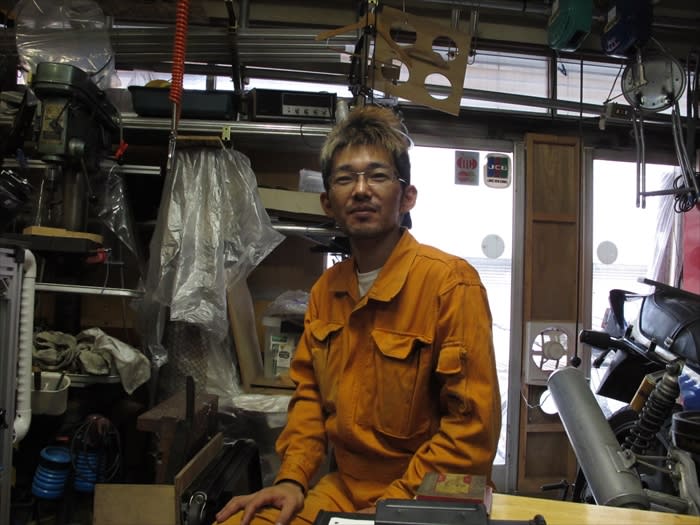
(ヘンテコなピッチのタップをお土産に持って来るのは止めて下さいね)
追加写真
kagayakiさんから頂いたコメントに「手配写真が出回った・・・なぜモザイクがはいっていないか・・・」と
ありましたので,お望みの様な写真にしてみました.

M4のネジ切ろうとタップを調べたら“M4 P0.75” なんてのはやっぱりイレギュラー,使い道に困ります.
もう一人の工作マニアの方.
おそらく国内でトップレベルの工作マニアが集う掲示板『趣味のCNCマシン掲示板 』
(主催はHP“旋盤で作る天体機材”のRock Hill様)
この掲示板で知り合った“溶接工A”さん.
大阪南部にお住まいということで先日わざわざ来てくださいました.
まだ若き30才.
なのに自宅の設備は自作CNCフライスの他に“岩下”のNCフライス盤(自作ではなく工業用),旋盤はオークマ製.
なんと平面研削盤に円筒研削盤まで持っているというからすごい.
研削盤なんてミクロンオーダーで研磨する機械.こんなん素人で持っている人,日本にそうはいないと思う.
同じく旋盤での切削の話しを聞いたら同じように返ってきた.
今使っているバイトは“スローアウェイチップ”(参考までに)と呼ばれる,刃先交換式の超硬切削チップ.
メーカーが用途に合わせて刃先を形成してくれて,切れなくなったら交換するヤツ.
これらはNC機やマシニングなどの自動機向けらしく,刃物がむき出しで回転している汎用機には向いてないらしい.
小学生のときにカンナ掛けを覚えて,高校生のときにボール盤を買ったという強者.
知的感漂うこちらも若き工作マニアの獅子って感じ.
(本人の希望でモザイク処理をおこなっています)

先日切り倒した“貝塚伊吹”の処理に困っているのをブログで知って,自宅から電動チェーンソーを
持ってきてくれました.
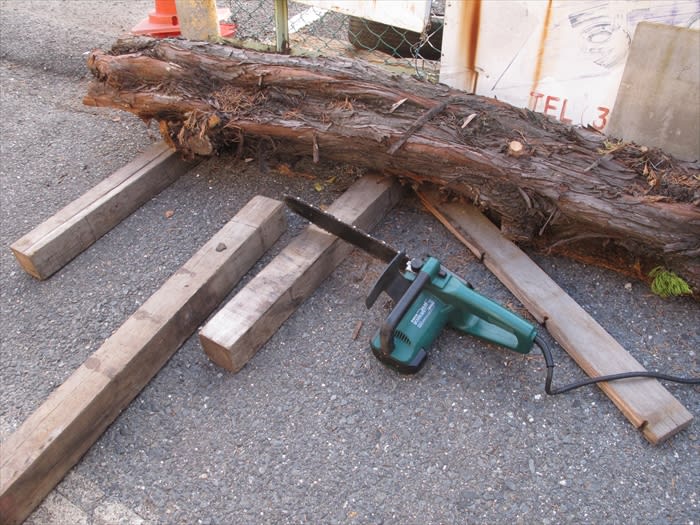
チェーンソーは生まれて初めての道具.
勝手が分からずへっぴり腰
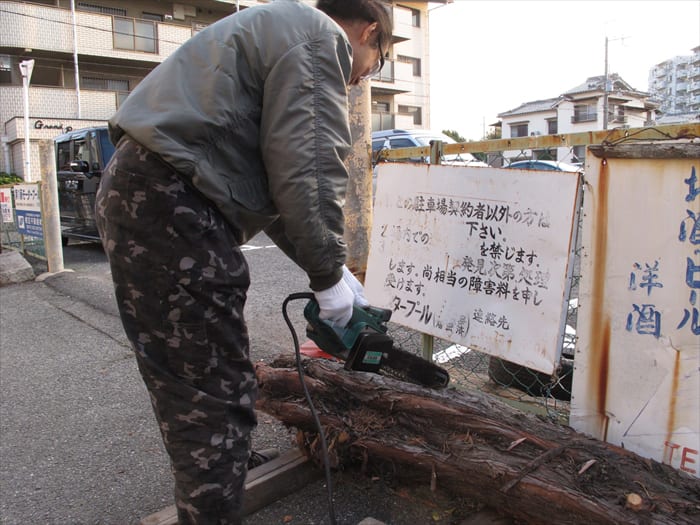
切り込む位置を変えながら,まっすぐになるように切ってます.

電動なので非力といっていましたが,やっぱり早いです.

溶接工Aさんにお手本を見せてもらいました.
結構グイグイ行ってます.

処分に困っていたこの“貝塚伊吹”.
切り刻んで燃やせるゴミで処分しようと考えていましたが,これを見た“kagayaki”さんの一言目
「イスにしたら良さそう」が頭から離れません.
そうこうしていたら先日買ったデジタル角度計を思い出しました.

任意の角度で“ゼロリセット”が出来て
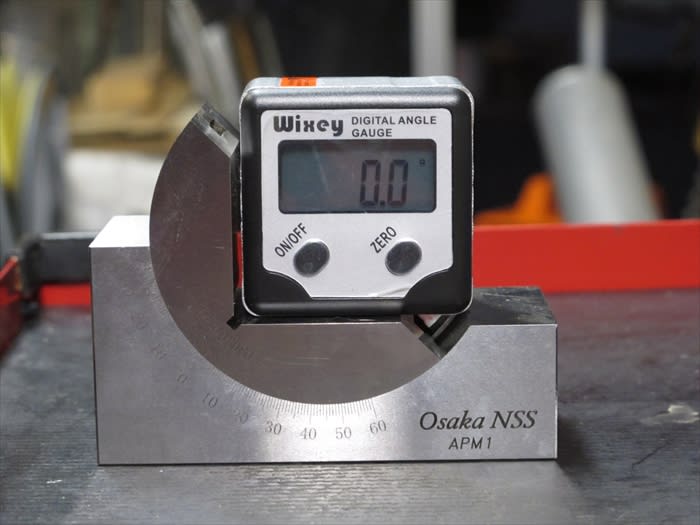
本体を傾けると,デジタルで角度が表示される便利モノ.(これで5千円もしないんです)

実は溶接工Aさんも庭の木でイスを作られた事があるそうで,作り方を教えてくれました.
切断する目安を書いた方がいいとのことで,イスの座面として“美味しい”ところを残すようにこの角度計で木の両端に
ケガキを入れます.

その線に沿って切断します.
しかし横向きでは全然力が入らず,ケガキ通りに切れないばかりか非常に疲れます.
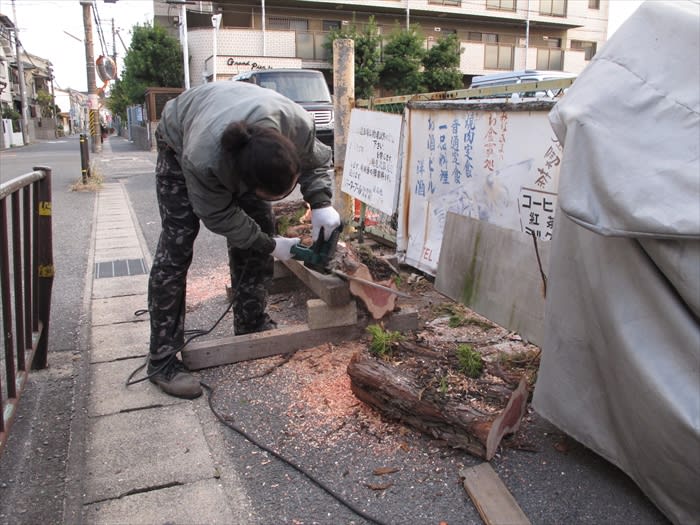
小さな脳みそ使って考えました.

非常に切断しやすいです.それも真っ直ぐに切れます.
途中で荷締めベルトの位置を変えて,最後まで真っ直ぐに切ってきます.
小さな脳みそもアドレナリン全開で良く思いついてくれます.

じゃ~ん
見事に半分に切断できました.
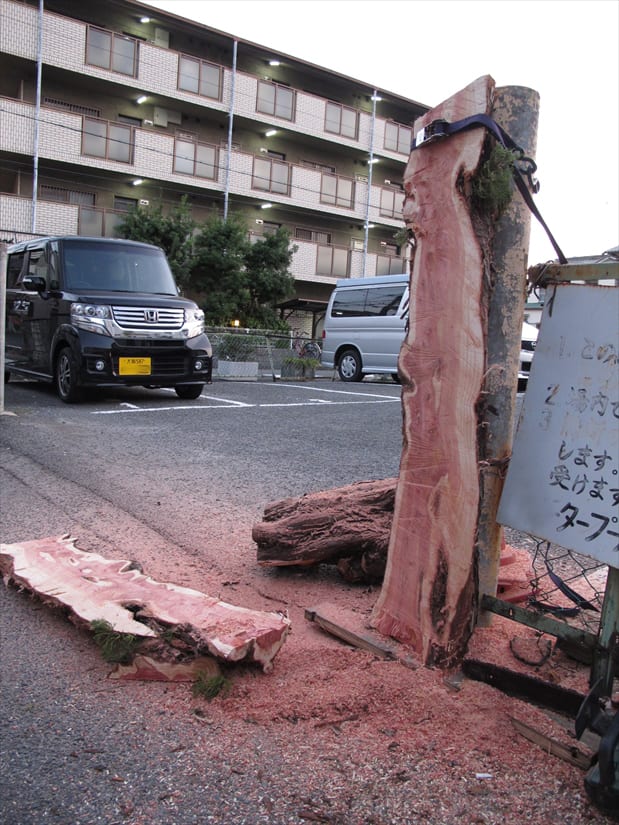
後で表面をカンナ掛けしやすいようにとチェーンソーの刃を立てて表面をさらってくれました.
(手前が最初に切り始め所.力が入らず斜めにノコが入っているのが分かると思います)

足になる部分(約50センチ)を二個と座面の木,用意出来ました.
面倒な切断が終わっている切断済みキット.いわゆる“製作キット”にしました.
これで忙しい某氏も喜んで木のイス作りのことを考えてくれるでしょう.

『会社の前に置くイスにいいなあ』と言っていたのは,会社の従業員さんが疲れたときに一息入れて一服する,
そんなときに腰掛けるところが有れば,少しでもくつろげるだろうにと思ってのこと.(たぶん)
なんて従業員思いなんでしょうか.(きっと)
涙が出てきそうな話です.(半分ほんと)
溶接工Aさん,ありがとうございました.
また遊びに来てください.こちらも工房へお邪魔するのを楽しみにしています.
追伸
使わないと思っていた半分に切った残りの方も,なんか形に風情が有って良いので暇が出来たら床の間の前に置く
花瓶台にしようと思って残すことにしました.
ではまた.