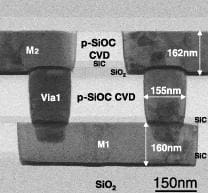
薄膜形成技術は物理的気相成長法 PVD(Physical Vapor Deposition)と化学的気相成長法 CVD(Chemaical Vapor Deposition)に大別される。
PVD
蒸着、電子ビーム、蒸着、スパッタなどが含まれる。真空蒸着は真空中にて原料が融点以上に加熱して残留ガスと衝突させずに基板へ堆積させる技術である。
現在主流として用いられているIonBeamSputtaerはAr、Xeなどの希ガスをプラズマで発生させ、ターゲット金属電極に衝突させはじき出された原子を反対側におかれた基板に堆積させる方法である。スパッタの堆積速度を上げるためにマグネトロンスパッタ装置が良く用いられる。これはターゲット電極裏に永久磁石を配置し電子を電界と磁界によって生じるサイクロイド運動によって閉じ込めて高密度のプラズマを生成できる。このことから1μm/分の堆積速度が得られる。
スパッタ原子は等方的に散乱させていくためにあまりにも電極間の距離が近いと散乱角度の影響を受けて基板に入射してしまう。それを防ぐために電極間の距離を伸ばし、圧力を下げるとことにより反射角の影響、背景原子との衝突の影響を防ぐことが出来る。この手法をロングスロースパッタという。(LTS)段差被覆性は向上するが堆積速度は下がる。
さらに原子の直進性を確保するために電極中間にコリメータという蜂の巣上のスリットを置いて一定の角度以上の原子を取り除くことが出来る。
最近でははじき出された原子を途中のコイル電極でイオン化して基板に引き込むIMP(IonMetalPlasma)スパッタも用いられている。

CVD
CVDは原料ガスをエネルギー源により分解して気相、表面反応に利堆積させる方法であり熱CVDとプラズマCVDの2つに大別される。
PVDと比べて段差被覆性に優れる、バッチ処理が可能、膜の抵抗率もPVD膜より低いというのが特徴である。
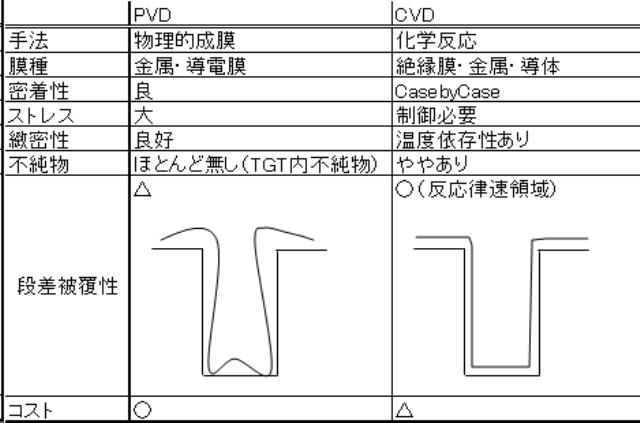
CVD-W タングステン(W)は耐熱性が高いことから主に基板へ落とすコンタクトやビアに用いられている。WF6を用いて堆積させる。
WF6+3H2⇒W+6HF 水素による還元
2WF6+3Si⇒2W +3SiF4 Siによる還元
2WF6+3SiH4⇒2W+3SiF4+6H2 (シランによる還元)
Si基板へのコンタクトではSiの還元により反応が始まる。Si上にのみ核が出来て水素による還元で急速にWが成長する。このプロセスでは反応性生物であるHFにより酸化膜が侵食され表面が荒れてしまう。シランにより還元するとHFが発生させずにWの粒径が小さくなる。しかしながらカバレッジが悪くなるために通常は最初の核形成でシランを用いて接合へのダメージを減らし、その後、水素還元にて接合へのダメージを軽減する。
CVD-TiN
W等の金属コンタクト配線材料のメタル拡散防止用に用いられるのがTiNである。スパッタ、もしくはCVDであるが被覆性からCVDが用いられることが多い。
TiCl4とNH3、N2/H2、NH3/H2が用いられる。
6TiCl4+8NH3⇒6TiN+24Hcl+N2
堆積温度はNH3還元で400から700度 温度が高いほどTiNに含まれるClが減る。
Al電極
Alは2.7μΩ・cm 合金でも3.5μΩ・cmと抵抗率が低く、SiO2巻くとの密着性も良いため電極材料としてよく用いられている。Al-Siは共融特性を示し、いずれかの原子を加えることによって融点がその各々の金属の融点より低くなる。ここで共融温度と呼ばれる融点の最小値は577℃(11.3%Si/88.7%Al)であるので生成の際の温度は577℃以下である必要がある。
Al中のSiへの溶解度は0.25重量%@400℃、0.5重量%@450℃、0.8重量%@500℃である。アニール中にSiはAl中に溶け込む。

溶け込むSiの量は溶解度だけでなく体積にも依存する。厚さHのAl金属が面積ZLでSiと接触している場合を考える。アニール後にSiは約√Dtだけ拡散する。Al膜におけるSiの拡散については4e-2exp(-0.92/kT)で与えられる。
これだけの長さでSiが飽和するとすれば消費されるSiの量は
Vol≒2√Dt(HZ)S(ρAl/ρSi)
接触面積A=HZで一様にSiが消費されるとすると拡散深さは
b≒2√Dt(HZ/A)S(ρAl/ρSi)
であるが現実には拡散は一様に起こらず限定された点で起こる。
このようなAlのスパイクを最小にする一つの方法はAlとSiwo同時に蒸着してAl中のSiの溶解度の近くまで
Siを加えること。Siとの間に拡散バリアとなる金属=バリアメタル(BM)を挿入することである。BMにはAlと反応せず密着性が良いことが求められる。前述のTiNは良く用いられる。

エレクトロマイグレーション(EM)
デバイスの微細化に伴い、配線寸法も縮小化が進んでおり流れる電流密度が増加している。EMは電流の影響により電子の運動量が原子に乗り移り金属原子が動いてしまう現象である。動いた部分は空洞(Void)になり、原子がたまったところは盛り上がる(PileUp) 盛り上がったところは配線のShort、Voidは配線のOPENを引き起こす。EMにより配線が断線するまでの平均時間MTFは
MTF≒1/J^2exp(Ea/kT)
とあらわされる。蒸着Alの活性化エネルギーEaは0.5eV程度である。(Al単結晶は1.4eV)EMを防ぐには銅と合金化して流会に銅を拡散させる。導電タイを絶縁膜で覆う、膜成長の間に酸素を導入するなどの対策がある。
流された元素が蓄積するのは粒界の3重点のため線幅が狭くなれば3重点も少なくなり生じにくくなる。
ストレスマイグレーション(SM)
温度、パッシベーション膜の応力により物理的に断線してしまう現象である。応力によるVoidの発生は3重点のない粒界で発生するため配線幅は小さいほど不利である。
Cu埋め込み技術
配線によるRC遅延を防止するために高伝導率の金属と低誘電率の絶縁膜が求められている。CuはAlよりも伝導率が高くEMに強いことからすでに多くのデバイスに用いられている。CuはPVD CVD メッキによって堆積させることが出来る。
Cuの問題としては腐食すること、エッチングで切れないこと、酸化膜との密着性が悪いということが挙げられる。
Cuを切る条件が見つからないことから通常は配膳溝を作成した後にCuを堆積させ、CMP等により余分なCuを取り除いて配線を生成するのが普通である。この手法をダマシンプロセスという。デュアルダマシンプロセスでは配線と下層配線への接続Viaが一括形成され、その後にCuを堆積、CMPにて平坦化させる。
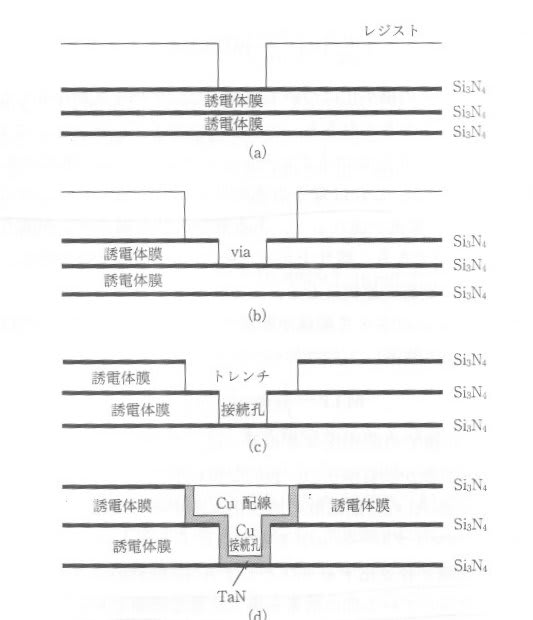
Cuは層間絶縁膜に用煮に拡散してしまうため底面や側面にはTa系の膜を用いて拡散を防止する。
Cu膜の堆積にスパッタと並んで用いられるのが安価なメッキ法である。硫化銅液を電解質とした電気分解によりウエハをカソード(陰極)側にすることにより銅イオンが集まり、銅が析出する。しかしながら溝に等方的に幕が堆積していくとVoidが生じてしまう。これを防ぐためにアクセラレータ、サプレッサー、レベラーが用いられる。メッキの促進と抑制をコントロールできる。
PVD
蒸着、電子ビーム、蒸着、スパッタなどが含まれる。真空蒸着は真空中にて原料が融点以上に加熱して残留ガスと衝突させずに基板へ堆積させる技術である。
現在主流として用いられているIonBeamSputtaerはAr、Xeなどの希ガスをプラズマで発生させ、ターゲット金属電極に衝突させはじき出された原子を反対側におかれた基板に堆積させる方法である。スパッタの堆積速度を上げるためにマグネトロンスパッタ装置が良く用いられる。これはターゲット電極裏に永久磁石を配置し電子を電界と磁界によって生じるサイクロイド運動によって閉じ込めて高密度のプラズマを生成できる。このことから1μm/分の堆積速度が得られる。
スパッタ原子は等方的に散乱させていくためにあまりにも電極間の距離が近いと散乱角度の影響を受けて基板に入射してしまう。それを防ぐために電極間の距離を伸ばし、圧力を下げるとことにより反射角の影響、背景原子との衝突の影響を防ぐことが出来る。この手法をロングスロースパッタという。(LTS)段差被覆性は向上するが堆積速度は下がる。
さらに原子の直進性を確保するために電極中間にコリメータという蜂の巣上のスリットを置いて一定の角度以上の原子を取り除くことが出来る。
最近でははじき出された原子を途中のコイル電極でイオン化して基板に引き込むIMP(IonMetalPlasma)スパッタも用いられている。

CVD
CVDは原料ガスをエネルギー源により分解して気相、表面反応に利堆積させる方法であり熱CVDとプラズマCVDの2つに大別される。
PVDと比べて段差被覆性に優れる、バッチ処理が可能、膜の抵抗率もPVD膜より低いというのが特徴である。
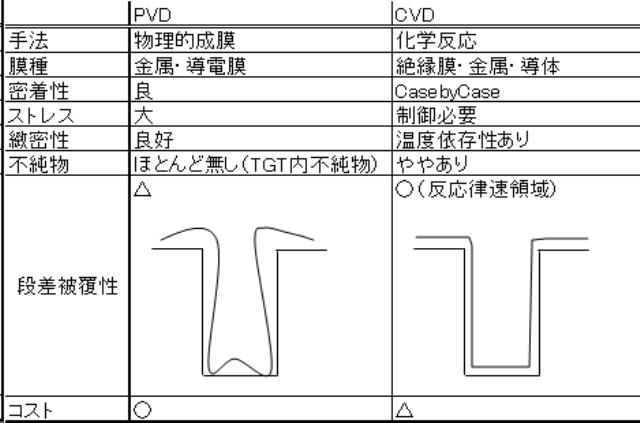
CVD-W タングステン(W)は耐熱性が高いことから主に基板へ落とすコンタクトやビアに用いられている。WF6を用いて堆積させる。
WF6+3H2⇒W+6HF 水素による還元
2WF6+3Si⇒2W +3SiF4 Siによる還元
2WF6+3SiH4⇒2W+3SiF4+6H2 (シランによる還元)
Si基板へのコンタクトではSiの還元により反応が始まる。Si上にのみ核が出来て水素による還元で急速にWが成長する。このプロセスでは反応性生物であるHFにより酸化膜が侵食され表面が荒れてしまう。シランにより還元するとHFが発生させずにWの粒径が小さくなる。しかしながらカバレッジが悪くなるために通常は最初の核形成でシランを用いて接合へのダメージを減らし、その後、水素還元にて接合へのダメージを軽減する。
CVD-TiN
W等の金属コンタクト配線材料のメタル拡散防止用に用いられるのがTiNである。スパッタ、もしくはCVDであるが被覆性からCVDが用いられることが多い。
TiCl4とNH3、N2/H2、NH3/H2が用いられる。
6TiCl4+8NH3⇒6TiN+24Hcl+N2
堆積温度はNH3還元で400から700度 温度が高いほどTiNに含まれるClが減る。
Al電極
Alは2.7μΩ・cm 合金でも3.5μΩ・cmと抵抗率が低く、SiO2巻くとの密着性も良いため電極材料としてよく用いられている。Al-Siは共融特性を示し、いずれかの原子を加えることによって融点がその各々の金属の融点より低くなる。ここで共融温度と呼ばれる融点の最小値は577℃(11.3%Si/88.7%Al)であるので生成の際の温度は577℃以下である必要がある。
Al中のSiへの溶解度は0.25重量%@400℃、0.5重量%@450℃、0.8重量%@500℃である。アニール中にSiはAl中に溶け込む。

溶け込むSiの量は溶解度だけでなく体積にも依存する。厚さHのAl金属が面積ZLでSiと接触している場合を考える。アニール後にSiは約√Dtだけ拡散する。Al膜におけるSiの拡散については4e-2exp(-0.92/kT)で与えられる。
これだけの長さでSiが飽和するとすれば消費されるSiの量は
Vol≒2√Dt(HZ)S(ρAl/ρSi)
接触面積A=HZで一様にSiが消費されるとすると拡散深さは
b≒2√Dt(HZ/A)S(ρAl/ρSi)
であるが現実には拡散は一様に起こらず限定された点で起こる。
このようなAlのスパイクを最小にする一つの方法はAlとSiwo同時に蒸着してAl中のSiの溶解度の近くまで
Siを加えること。Siとの間に拡散バリアとなる金属=バリアメタル(BM)を挿入することである。BMにはAlと反応せず密着性が良いことが求められる。前述のTiNは良く用いられる。

エレクトロマイグレーション(EM)
デバイスの微細化に伴い、配線寸法も縮小化が進んでおり流れる電流密度が増加している。EMは電流の影響により電子の運動量が原子に乗り移り金属原子が動いてしまう現象である。動いた部分は空洞(Void)になり、原子がたまったところは盛り上がる(PileUp) 盛り上がったところは配線のShort、Voidは配線のOPENを引き起こす。EMにより配線が断線するまでの平均時間MTFは
MTF≒1/J^2exp(Ea/kT)
とあらわされる。蒸着Alの活性化エネルギーEaは0.5eV程度である。(Al単結晶は1.4eV)EMを防ぐには銅と合金化して流会に銅を拡散させる。導電タイを絶縁膜で覆う、膜成長の間に酸素を導入するなどの対策がある。
流された元素が蓄積するのは粒界の3重点のため線幅が狭くなれば3重点も少なくなり生じにくくなる。
ストレスマイグレーション(SM)
温度、パッシベーション膜の応力により物理的に断線してしまう現象である。応力によるVoidの発生は3重点のない粒界で発生するため配線幅は小さいほど不利である。
Cu埋め込み技術
配線によるRC遅延を防止するために高伝導率の金属と低誘電率の絶縁膜が求められている。CuはAlよりも伝導率が高くEMに強いことからすでに多くのデバイスに用いられている。CuはPVD CVD メッキによって堆積させることが出来る。
Cuの問題としては腐食すること、エッチングで切れないこと、酸化膜との密着性が悪いということが挙げられる。
Cuを切る条件が見つからないことから通常は配膳溝を作成した後にCuを堆積させ、CMP等により余分なCuを取り除いて配線を生成するのが普通である。この手法をダマシンプロセスという。デュアルダマシンプロセスでは配線と下層配線への接続Viaが一括形成され、その後にCuを堆積、CMPにて平坦化させる。
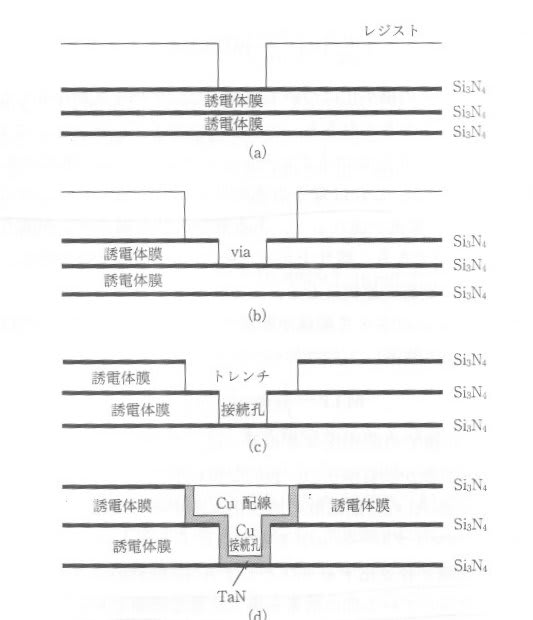
Cuは層間絶縁膜に用煮に拡散してしまうため底面や側面にはTa系の膜を用いて拡散を防止する。
Cu膜の堆積にスパッタと並んで用いられるのが安価なメッキ法である。硫化銅液を電解質とした電気分解によりウエハをカソード(陰極)側にすることにより銅イオンが集まり、銅が析出する。しかしながら溝に等方的に幕が堆積していくとVoidが生じてしまう。これを防ぐためにアクセラレータ、サプレッサー、レベラーが用いられる。メッキの促進と抑制をコントロールできる。