Electronic tags (Tag): composed of coupling elements and chips, each RFID tag has a unique electronic code, attached to the object to identify the target object, commonly known as electronic tag or smart tag rfid electronic tag: active tag, passive tag, semi Active semi-passive tags.
RFID working principle: After the tag enters the magnetic field, it receives the radio frequency signal from the reader, and uses the energy obtained by the induced current to send out the product information stored in the chip (Passive Tag, passive tag or passive tag), or actively send a certain Frequency signal (Active Tag, active tag or active tag); after the reader reads and decodes the information, it is sent to the central information system for relevant data processing.
At present, the tire traceability marks on the market generally use the form of "bar code + sidewall information" to store various types of tire information, but the bar code and sidewall position information are located on the surface of the carcass, and the tire will soon be worn away after use . Once these information cannot be seen visually, it means that the tire information is lost, so that information such as tire model, pattern, and diameter cannot be identified. If tires are illegal and unsafe to use (unqualified tires, overloaded use, expired use, etc.), it will directly cause difficulties for the user's use, maintenance, and settlement of claims, leading to disputes and even frequent safety accidents. Waste of energy resources and damage to the environment.
The application of RFID technology can standardize the orderly production and sales of the tire industry (prevent counterfeiting, OEM, and cross-country goods), realize tire lifecycle management; standardize the transportation industry, ensure personal and property safety; promote and standardize the tire retreading industry, and realize tires Circular Economy
Demonstration of the application of RFID in tires: In the tire building process, the electronic tag is implanted inside the tire, which can withstand the deformation, high temperature and high pressure in the tire building and vulcanization process. The finished tire has undergone X-ray inspection, bubble inspection, dynamic balance and uniformity inspection, durability test inspection, etc., showing its reliable performance
It can be seen that the combination of RFID technology and tire manufacturing technology can not only solve the problems encountered in the current tire identification and traceability processes, but also that the tires use RFID electronic tags embedded in the tires, which can write tire production data, sales data, and use Data, retreading data, etc., and the corresponding data can be collected and read through the terminal at any time, and combined with the corresponding management software, the recording and traceability of the tire's full life cycle data can be realized.
Rapid prototyping is a important role in the inspection drawing design is reasonable, if you don't have a designed of product, and without verification for structure and function, when begain a large number of production, will find the design flaws that will cause huge economic loss.
Today, we will introduce some details that our company workers pays attention to in the process of repair rapid prototyping after getting off the CNC machining. That’s great, if you could leave a message to add
1. When ABS rapid prototype is bonded, pay attention to the amount of glue and avoid cracking.
2. Careful read the production process and 2S-drawings.
3. Grasp the dimension accuracy of the rapid prototyping by hand polishing.
4. Acrylic panel in bonding by glue, have to don't have craze and bubble.
5. When assemble cann’t in the wrong place, and don't have a dislocation and clearance
6. PC's products in the oven or hair dryer, don't be too high temperature.
7. POM, nylon, PP cann’t able to glue, the reason is that these three materials glue instability, so try not to use CNC machining in section.
8. When the workpiece has an R Angle, cann’t polishing it into a right Angle. There are also places with radians on the edge of the workpiece. Also, pay attention to do it.
9. When painting do not have color difference off the paint, in the oil and spray oil control dust point.
Not everyone can good for Rapid prototyping worker, It is necessary to be patient, to sit still, good guys.
With the development of Shaped springs application technology, more requirements are put forward for Shaped spring materials. Mainly in terms of improving fatigue life and anti-relaxation performance under high stress; secondly, according to different purposes, it is required to have corrosion resistance, non-magnetic, electrical conductivity, wear resistance, heat resistance, etc. For this reason, in addition to the development of new varieties of Shaped spring materials, it has also achieved beneficial results in strict control of chemical composition, reduction of non-metallic inclusions, and improvement of surface quality and dimensional accuracy.
(1) Development of Shaped Spring Steel Production Process In order to improve the quality of Shaped spring steel, industrially developed China has generally adopted out-of-furnace refining technology, continuous casting technology, new rolling and online automatic detection and control equipment.
In order to ensure the chemical composition of steel and reduce the content of gases and various non-metallic inclusions, a large-capacity electric furnace or converter is used for smelting, and an external ladle is used for refining to reduce the oxygen content (mass fraction) to (0.0021~0.0010)%. Produce ultra-pure steel, which greatly improves the design and working stress of the Shaped spring.
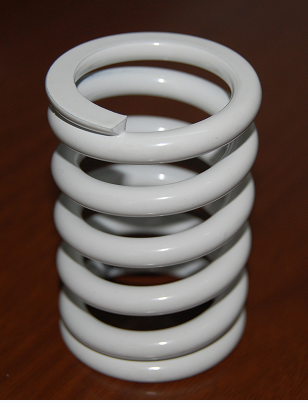
The continuous casting production process has been adopted in the production of Shaped spring steel. Continuous casting can reduce steel segregation, reduce secondary oxidation, improve surface decarburization, and make the structure and performance stable and uniform through techniques such as electromagnetic stirring and low-temperature casting.
The split-type full continuous rolling mill can improve the dimensional accuracy and surface quality, and at the same time make the steel microstructure uniform along the length. In order to ensure the surface quality of the product during the rolling process, online automatic detection and control are adopted. In order to be suitable for the production of variable cross-section Shaped spring flat steel, a new austenite rolling process was developed, that is, the steel is heated to the austenite zone and then quenched to the metastable austenite zone for plastic processing and quenching. This process can increase the strength of the steel without reducing its plasticity. In addition, the properties of Shaped spring steel can be improved by online heat treatment and surface hardening after rolling.
(2) The development of alloy steel The main function of alloying elements is to improve mechanical properties, improve process performance and give certain special properties. SiCr steel has been applied to valve Shaped spring and Suspension Shaped spring. Si is an anti-stress relaxation alloy element. Adding V and Mo to SiCr steel forms SiCrV and SiCrMo steels, which can improve fatigue life and anti-relaxation properties. At the same time, SiCr drawn wire has better relaxation resistance when working at high temperatures than piano wire and carbon Shaped spring wire for important purposes. With the high-speed and miniaturization of engines, Ti alloys with good anti-flutter performance, light weight and small elastic modulus have been widely used, and their strength can reach 2000MPa.
How to save the remaining materials after CNC machining
Customers who use CNC cutting machine know that CNC cutting machine will leave a surplus material after cutting, but this phenomenon generally enterprises do not have a good solution.
Therefore, CNC cutting machine can save materials from the following three aspects. The following is a brief introduction to the specific operation implementation plan:
First of all, for the unreasonable purchase of plates, which leads to parts arrangement can not be finished, forming the problem of remaining edges. When enterprises purchase materials, for various reasons, the flatness of the purchased plates is not high and the plate surface is not regular enough. To a large extent, it is difficult to plan the plate surface cutting, and the parts to be cut can not be arranged reasonably, resulting in excessive surplus materials.
Solution: enterprises in the purchase of plate, should pay attention to waste of surplus materials as a reference factor. Not only to consider the material, flatness, price, but also to consider the purchase of this material, the amount of surplus material will be generated, in the cutting machine try to use surplus material.
Secondly, the machine operator's budget ability of steel plate arrangement is not enough, and improper arrangement leads to steel plate surplus. In general, the layout of cutting parts requires designers to fully understand the cutting requirements of enterprises and make decisions.
Solution: operators need to calculate and design the cutting mode before cutting. Strive for one-time, maximize the arrangement of parts to be cut on a single board surface, in order to reduce material loss and processing time.
Finally: surplus material management is not in place, can not be tailored to suit, reasonable use. Due to improper management of surplus materials, reasonable materials can not be used properly, resulting in waste of surplus materials.
Solution: sort out the surplus materials, do not stack them, and make records to facilitate management, so as to achieve the purpose of saving surplus materials.
In our lives, many things use springs. Springs have become necessities for many things. These things are produced in different industries. Therefore, since objects cannot be separated from springs, industry cannot be separated from springs. . Springs are a kind of messy appearance, large and small, thick and thin, and some surfaces also have colors. In short, they are characterized by good elasticity, and some have different characteristics and use. The following Zhejiang spring manufacturer introduces the difference between compression spring and extension spring.
First of all, from a design perspective, there are many differences between the two in design
(1) The basic parameters required for compression spring design are outer diameter, inner diameter and length, which are also the space occupied by the spring. This is the first condition. Spring force, when the spring is in the working state, it is necessary to clearly understand the actual force (N) required in order to select the material, wire diameter and compression, that is, the compression stroke, so as to determine the number of turns.
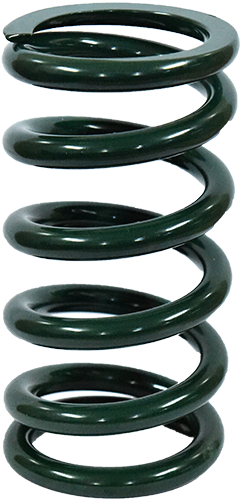
(2) Spring working environment, working in a high humidity environment, the surface of the spring should be treated to prevent corrosion and moisture; working in a high temperature environment, because temperature has a great influence on the service life of the spring, so high temperature environment work needs to be selected High temperature R. Electrostatic material, working normally.
Second, the key elements of Extension spring design
(1) The required tension, that is, the weight that can be loaded, determines the material, wire diameter and adjustable length of the Extension spring. Space range, knowing the space range, you can determine the outer diameter, free length and winding times of the Extension spring.
Finally, in terms of shape
(1) For Extension spring, Extension spring is a coil spring under axial tension. For Extension spring, it is usually made of circular cross-section material. In the case of no load gravity, the tension between the coil springs is usually very tight, and there is no gap between the rings.
(2) For the compression spring, the compression spring is used under the pressure of the coil spring, and the material used in it is mostly circular in cross section. It is also useful to have a stroke made of rectangular and multi-strand steel. The spring is usually It is for the pitch. For example, the shape of the compression spring is: cylindrical, conical, convex and concave, and a small non-circle. When the amount is large, the compression spring has a certain gap between the circle and the circle. When the spring shrinks and deforms under the action of external load , Deformation energy storage.