タグチメソッドの損失関数と工程フィードバックについての内容をさらします.
1.損失関数
タグチメソッドの損失関数とは,部品や製品のねらい値に対するバラツキで発生する製造側及び顧客側(社会側)の損失を表す関数で,下記に示す式になります.

ここで,
y :製品,部品等のねらい値
m :製品,部品等の個々の実際の値
Δ0 :製品,部品が実際に機能しなくなる値(機能限界)
A0 :機能限界に達した場合の損失金額
グラフにすると,下記のようになります.

Fig Loss Function Sample
黒の線:損失関数
赤の線:規格限界(公差)
青の線:一様分布
緑の線:正規分布
この図を見れば判りますが,公差内でもバラツキが大きい場合は,損失が大きくなります.(正規分布に比べ,一様分布のほうがバラツキは大きいです)
この式は2乗損失と呼ばれるもので,統計では実際の値の推計を,平均やら中央値(メディアン)やら,最小2乗法やら等々で推計しますが,その時の推計の外れ方を,(y-m)^2とかで評価(この式が一番簡単な評価方法)するそうです.(赤池情報量規準とかもこの仲間でしょうか)
上記式に比例定数A0/Δ0を付け加えて,田口さんが損失関数を定義しました.
この損失関数の意味は,デミングさんが言うとおり,「規格に合わせるだけでは不十分で,さらなるバラツキの低減が必要である」という事になると思います.
ちなみに,上記の式を考えた安全率と公差は,下記のようになります
安全率:
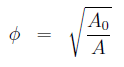
ここでAは手直しもしくは廃棄のコスト
つまり,安全率は機能損失コストと不良品を処理するコストに比例するという事です.
今まで1.2やら2やら4やら10とか経験に基づいて決めていたものに対し,経済的な観点も考慮して決めましょうという提案です.
公差:

これは通常の公差の計算:±ねらい値×安全率と同じ考えだと思います.
2.工程フィードバック
次に工程のフィードバックですが,これは,どの様に工程のねらい値を経済的にコントロールするかを示したものです.
これはすでに工程設計にて,グチメソッドのパラメータ設計(直交表実験)を使い,工程のパラメータの把握にてバラツキ自体(共通原因のバラツキ)の低減及び,ねらい値調整のためのパラメータの把握が十分なされている事を前提としています.
つまり,工程を稼動させる前に,きちんと工程設計がなされていれば,フィードバック制御が可能であるという事です.
このフィードバックに必要な要素及び,式が下記になります.
(品質特性によるフィードバック制御(計量値の場合))

ここで,
L0 :現行の損失関数(円/個またはバッチ)
L :最適時の損失関数(円/個またはバッチ)
Δ :目的特性値の許容差
A :不良品損失(円)
B :計測コスト(円)
C :調整コスト(円)
n0 :現行の計測間隔(個またはバッチ)
n :最適計測間隔(個またはバッチ)
D0 :現行の調整限界
D :最適調整限界
u0 :現行の平均調整間隔(個またはバッチ)
u :最適平均調整間隔(個またはバッチ)
l :計測方法のタイムラグ(個またはバッチ)
σm :計測誤差の標準偏差
上記を見ていただいて判るように,このフィードバックシステムは,常時出力を監視しているのではなく,監視(計測)費用と不良を出す損失とのバランスを見て,監視間隔を見ているわけです.(サンプリングによる制御と同じような感じでしょう)
つまり,サンプリング回数が少なければ,正しい波形が取れないデジタル・オシロスコープみたいなな感じでしょうか.
ちなみに調整は,下記式による調整量を用いないと,前に漏斗の実験の時のようなハンティング現象が起きる可能性があります.
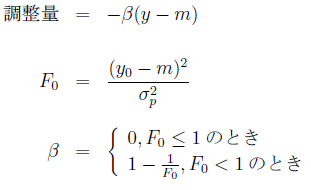
上記式は,製品のねらい値のバラツキが,調整限界より小さい場合は調整不要であるが,大きい場合は調整をかけなければならない.つまり,調整限界より大きなバラツキがあり調整しない場合は,大きく損をする可能性があるということです.
これは,共通原因・特殊原因のバラツキ両方に言えることです.特殊原因の場合は,すでに調整方法がわかっているとの前提ですので,調整を行えばいいだけですが,共通原因の場合は,再度パラメータ設計等を行い,共通原因のバラツキをもっと提言する必要があるということになると思います.
普通にシューハート図等による管理では,工程は安定しているが,損をしているかどうかは自明ではありません.しかし,調整限界も考慮する事により,損失まで管理しようというのが,この考え方の基だと思います.
また,調整による工程の管理は,まさしくフードバック制御です.下記条件がそろっていれば,かなり効果的でしょう.
3.検査設計
この場合は,トラブル単位(保証単位)(a)=検査単位(b)=処理単位(c)の場合を書きます.
これは,通常の工業製品(例えば家電)等の場合は,製品1つ1つが保証されるもの(単位)であり,通常は製品1つ1つを検査しており,手直しや,破棄も製品1つ1つで行うからです.
石油やジュースのようなものは,こうではありませんし,鉄ロールや,布とかも違います.
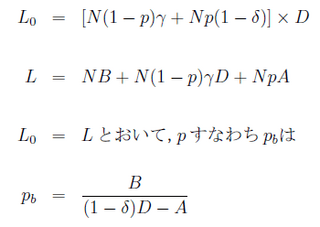
ここで,
D :出荷後トラブルを起こした時のトラブル1個あたりの平均損失(円)
B :検査費用(選別費用)(円)
A :品物に対し,破棄,手直し,値下げ,などの処置を出荷側が行った
ときの1個あたりの経費や損失(円)
p :不適合率(不良率)
δ :その検査で不良となるものの中で,合格品の割合.不明の時はゼロとする.
L0 :品物をそのまま出荷した時の損失.
L :品物を選別して不良品は手直し,破棄などそのまま出荷せず,
あるオペレーションをしたときの損失(円)
pb :臨界不適合率(不良率)
ここでの限界不良率とは,その不良率以上では全数検査しないと確実に(自社と顧客双方が)損をする率であり,限界不良率以下だから検査しないといっても,実際の不良率が限界不良率に近ければ近いほど自社・顧客双方の儲けは薄くなり,儲けが薄いため,やはり倒産という事になるやも知れません.
もちろん限界不良率以下の場合に全数検査したら,検査費用や処理費用等の費用がかかり,やはり儲かりません.
つまり,検査だけでは儲かる品質を維持するのはかなり難しいという結論になります.
やはり,QCの基本通り,「品質はライン(研究開発・製造・販売・管理)で造り込み」実際の不良率を限界不良率よりかなり低く維持すること(=工程能力を高く維持する事)を行わないと,倒産への道を進む事になります.
もちろん,工程能力が低く,限界不良率近い不良率の場合は,全数検査しか手がありません.
ちなみに最終検査はどの工場でも全数行っているとは思います.これは,どちらかというと,全ラインの工程能力の確認のために行うためだと思います.
最終検査ですから,すべての工程で作られた部品が組みつけられ,製品になったものを検査するので,ここでの検査はすべての部品を一度に検査しているのと同等になります(もちろん最終検査の検査項目しだいですが)ので,検査としては効率がいいと思います.不適合品の処理は一番費用がかかりますが.
従って,最終検査は全数検査を行ったほうが,品質のモニタリング,品質向上のためのデータ収集のためにはいいと思います.(もちろん,最終検査の費用の低減は独自に図られるべきです.)
QC=検査ではありません.海外の工場で必ず書かれている出荷検査の意味の"Out Going QC(Shipping QC)"の看板を見ると,毎回悲しくなってしまいます.
そう,本当は"Shipping Inspection"と書いて欲しいのです.こう書かれない限り,QCのリーダやマネージャが事務所から出てきて,現場を見,現物に触れ,現実を感じることを自発的に行ってくれないような気がします.
ただ,QCには検査は必要ですし,不適合品の管理も必要です.私は検査を,「品質向上のためのデータ収集及び,不適合品の解析のため」に行うことが第一義であると思っていますし,人と話す時もこう言っていたつもりです.(通じているかどうかは別にして)そして,そのデータ等を元に「継続的改善」を進めていくのです.
また,「工程能力が高くなければ,儲かる品質を確保できない」という事の理解が必要であると思います.品質を考慮してないプロセス・リソースの計画や人材の投資等(ただ単純に需要数と釣合う投資)では,工程能力の低さから,必ず品質が不足すると思います.従って儲からないのです.コストを単純に低減するのでは儲からないのです.必要なのは,顧客の期待品質と釣合うための工程能力を確保するだけの投資だと思います.「品質は金がかかる」という人がいますが,本当は,「品質確保もできない程度の投資では,丸損:もっとお金がかかる」のです.そして,その損は,自社と顧客双方で支払わなければならないのです.
4.参考文献
1.損失関数
タグチメソッドの損失関数とは,部品や製品のねらい値に対するバラツキで発生する製造側及び顧客側(社会側)の損失を表す関数で,下記に示す式になります.

ここで,
y :製品,部品等のねらい値
m :製品,部品等の個々の実際の値
Δ0 :製品,部品が実際に機能しなくなる値(機能限界)
A0 :機能限界に達した場合の損失金額
グラフにすると,下記のようになります.

Fig Loss Function Sample
黒の線:損失関数
赤の線:規格限界(公差)
青の線:一様分布
緑の線:正規分布
この図を見れば判りますが,公差内でもバラツキが大きい場合は,損失が大きくなります.(正規分布に比べ,一様分布のほうがバラツキは大きいです)
この式は2乗損失と呼ばれるもので,統計では実際の値の推計を,平均やら中央値(メディアン)やら,最小2乗法やら等々で推計しますが,その時の推計の外れ方を,(y-m)^2とかで評価(この式が一番簡単な評価方法)するそうです.(赤池情報量規準とかもこの仲間でしょうか)
上記式に比例定数A0/Δ0を付け加えて,田口さんが損失関数を定義しました.
この損失関数の意味は,デミングさんが言うとおり,「規格に合わせるだけでは不十分で,さらなるバラツキの低減が必要である」という事になると思います.
ちなみに,上記の式を考えた安全率と公差は,下記のようになります
安全率:
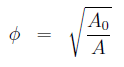
ここでAは手直しもしくは廃棄のコスト
つまり,安全率は機能損失コストと不良品を処理するコストに比例するという事です.
今まで1.2やら2やら4やら10とか経験に基づいて決めていたものに対し,経済的な観点も考慮して決めましょうという提案です.
公差:

これは通常の公差の計算:±ねらい値×安全率と同じ考えだと思います.
2.工程フィードバック
次に工程のフィードバックですが,これは,どの様に工程のねらい値を経済的にコントロールするかを示したものです.
これはすでに工程設計にて,グチメソッドのパラメータ設計(直交表実験)を使い,工程のパラメータの把握にてバラツキ自体(共通原因のバラツキ)の低減及び,ねらい値調整のためのパラメータの把握が十分なされている事を前提としています.
つまり,工程を稼動させる前に,きちんと工程設計がなされていれば,フィードバック制御が可能であるという事です.
このフィードバックに必要な要素及び,式が下記になります.
(品質特性によるフィードバック制御(計量値の場合))

ここで,
L0 :現行の損失関数(円/個またはバッチ)
L :最適時の損失関数(円/個またはバッチ)
Δ :目的特性値の許容差
A :不良品損失(円)
B :計測コスト(円)
C :調整コスト(円)
n0 :現行の計測間隔(個またはバッチ)
n :最適計測間隔(個またはバッチ)
D0 :現行の調整限界
D :最適調整限界
u0 :現行の平均調整間隔(個またはバッチ)
u :最適平均調整間隔(個またはバッチ)
l :計測方法のタイムラグ(個またはバッチ)
σm :計測誤差の標準偏差
上記を見ていただいて判るように,このフィードバックシステムは,常時出力を監視しているのではなく,監視(計測)費用と不良を出す損失とのバランスを見て,監視間隔を見ているわけです.(サンプリングによる制御と同じような感じでしょう)
つまり,サンプリング回数が少なければ,正しい波形が取れないデジタル・オシロスコープみたいなな感じでしょうか.
ちなみに調整は,下記式による調整量を用いないと,前に漏斗の実験の時のようなハンティング現象が起きる可能性があります.
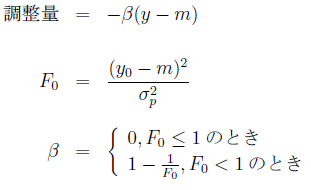
上記式は,製品のねらい値のバラツキが,調整限界より小さい場合は調整不要であるが,大きい場合は調整をかけなければならない.つまり,調整限界より大きなバラツキがあり調整しない場合は,大きく損をする可能性があるということです.
これは,共通原因・特殊原因のバラツキ両方に言えることです.特殊原因の場合は,すでに調整方法がわかっているとの前提ですので,調整を行えばいいだけですが,共通原因の場合は,再度パラメータ設計等を行い,共通原因のバラツキをもっと提言する必要があるということになると思います.
普通にシューハート図等による管理では,工程は安定しているが,損をしているかどうかは自明ではありません.しかし,調整限界も考慮する事により,損失まで管理しようというのが,この考え方の基だと思います.
また,調整による工程の管理は,まさしくフードバック制御です.下記条件がそろっていれば,かなり効果的でしょう.
- モデルがかなりしっかり出来ている.(モデルの選択・パラメータ設計が出来ている.
- フィードバックをかける信号(通常は出力)の測定誤差が十分小さい.
- フィードバックのタイミングも遅くない.
3.検査設計
この場合は,トラブル単位(保証単位)(a)=検査単位(b)=処理単位(c)の場合を書きます.
これは,通常の工業製品(例えば家電)等の場合は,製品1つ1つが保証されるもの(単位)であり,通常は製品1つ1つを検査しており,手直しや,破棄も製品1つ1つで行うからです.
石油やジュースのようなものは,こうではありませんし,鉄ロールや,布とかも違います.
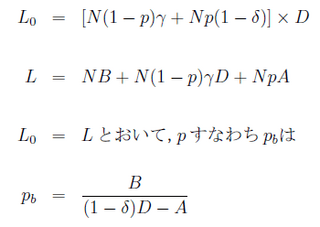
ここで,
D :出荷後トラブルを起こした時のトラブル1個あたりの平均損失(円)
B :検査費用(選別費用)(円)
A :品物に対し,破棄,手直し,値下げ,などの処置を出荷側が行った
ときの1個あたりの経費や損失(円)
p :不適合率(不良率)
δ :その検査で不良となるものの中で,合格品の割合.不明の時はゼロとする.
L0 :品物をそのまま出荷した時の損失.
L :品物を選別して不良品は手直し,破棄などそのまま出荷せず,
あるオペレーションをしたときの損失(円)
pb :臨界不適合率(不良率)
ここでの限界不良率とは,その不良率以上では全数検査しないと確実に(自社と顧客双方が)損をする率であり,限界不良率以下だから検査しないといっても,実際の不良率が限界不良率に近ければ近いほど自社・顧客双方の儲けは薄くなり,儲けが薄いため,やはり倒産という事になるやも知れません.
もちろん限界不良率以下の場合に全数検査したら,検査費用や処理費用等の費用がかかり,やはり儲かりません.
つまり,検査だけでは儲かる品質を維持するのはかなり難しいという結論になります.
やはり,QCの基本通り,「品質はライン(研究開発・製造・販売・管理)で造り込み」実際の不良率を限界不良率よりかなり低く維持すること(=工程能力を高く維持する事)を行わないと,倒産への道を進む事になります.
もちろん,工程能力が低く,限界不良率近い不良率の場合は,全数検査しか手がありません.
ちなみに最終検査はどの工場でも全数行っているとは思います.これは,どちらかというと,全ラインの工程能力の確認のために行うためだと思います.
最終検査ですから,すべての工程で作られた部品が組みつけられ,製品になったものを検査するので,ここでの検査はすべての部品を一度に検査しているのと同等になります(もちろん最終検査の検査項目しだいですが)ので,検査としては効率がいいと思います.不適合品の処理は一番費用がかかりますが.
従って,最終検査は全数検査を行ったほうが,品質のモニタリング,品質向上のためのデータ収集のためにはいいと思います.(もちろん,最終検査の費用の低減は独自に図られるべきです.)
QC=検査ではありません.海外の工場で必ず書かれている出荷検査の意味の"Out Going QC(Shipping QC)"の看板を見ると,毎回悲しくなってしまいます.
そう,本当は"Shipping Inspection"と書いて欲しいのです.こう書かれない限り,QCのリーダやマネージャが事務所から出てきて,現場を見,現物に触れ,現実を感じることを自発的に行ってくれないような気がします.
ただ,QCには検査は必要ですし,不適合品の管理も必要です.私は検査を,「品質向上のためのデータ収集及び,不適合品の解析のため」に行うことが第一義であると思っていますし,人と話す時もこう言っていたつもりです.(通じているかどうかは別にして)そして,そのデータ等を元に「継続的改善」を進めていくのです.
また,「工程能力が高くなければ,儲かる品質を確保できない」という事の理解が必要であると思います.品質を考慮してないプロセス・リソースの計画や人材の投資等(ただ単純に需要数と釣合う投資)では,工程能力の低さから,必ず品質が不足すると思います.従って儲からないのです.コストを単純に低減するのでは儲からないのです.必要なのは,顧客の期待品質と釣合うための工程能力を確保するだけの投資だと思います.「品質は金がかかる」という人がいますが,本当は,「品質確保もできない程度の投資では,丸損:もっとお金がかかる」のです.そして,その損は,自社と顧客双方で支払わなければならないのです.
4.参考文献
- Dening, W. Edwards, The New Economics: for Industry, government, education -2nd ed., 1994, ISBN:0-262-54116-5
- 田口玄一 他, 製造段階の品質工学, 1989, ISBN:4-542-51102-2
- 宮川雅巳, 品質を獲得する技術 タグチメソッドがもたらしたもの, 2000, ISBN:4-8171-0399-6