Ptfe teflon tube extrusion machine is divided into many kinds, exactly say ptfe tube forming process has push and pressure method, extrusion method, hydraulic method, welding method, winding method, etc., which is mainly push and pressure method.Generally dispersed PTFE resin with particle size of 500 microns and apparent density of 0.45g/ml ~ 0.55g/ml is adopted.The small diameter tube chooses the compression quite big resin, the medium and large diameter tube chooses the compression quite small resin.Extruder usually choose 200 and 260 solvent oil.PTFE thermal shrinkage tube, PTFE spiral tube, PTFE steel wire reinforced hydraulic tube and so on can be produced by the secondary processing of PTFE tube.
1.1 common ptfe teflon pipe
Ptfe ordinary tube is made of ptfe dispersion resin at room temperature with organic solvent as extruder, and then through drying and sintering.According to the size of the pipe diameter can be divided into two types of ordinary pipe and micro pipe.Ordinary tube inner diameter > 4mm, micro tube inner diameter ≤4mm.
Typical formula for PTFE tube production:
Dispersed PTFE resin: 100 (weight)
Extruder: 18 ~ 24
Production process:
PTFE, extruder - mixing - pushing - pressing - drying - sintering - cooling - products.
Production process parameters:
Mixing: temperature ≤19 ℃, time 10min ~ 20min, mixed at 25 ℃ ~ 30 ℃ for more than 24h.
Blank: compression rate is about 50mm/ min, pressure is 0 ~ 3MPa.
Pushing pressure: the cavity temperature is 30 ℃ ~ 50 ℃, and the die temperature is 50 ℃ ~ 60 ℃.
Drying: under 210 ℃,2h ~ 3h
Sintering: batch sintering, temperature rise rate of 60 ℃/ h,375 ℃±5 ℃ insulation for 4h.
Continuous sintering, dry area 100 ℃ ~ 250 ℃, preheating area 250 ℃ ~ 330 ℃, sintering area 380 ℃ ~ 420 ℃, cooling area less than 300 ℃.
Main equipment: mixing machine, preforming machine, vertical pushing press, drying and sintering furnace.
USES: as insulation and fluid conduit.
1.2 polytetrafluoroethylene heat-shrinkable tube
PTFE thermal shrinkable tube has the property of being heat-shrinkable, so it can be tightly coated on the surface of other workpieces, making the workpieces resistant to corrosion, electrical insulation and viscosity.Widely used in electrical, chemical, mechanical, printing and other industries.The maximum shrinkage of PTFE shrink tubes is reported to be more than 75%.
It is processed by disperse PTFE resin. The principle is that PTFE is subjected to stress during processing and produces forced high-elastic deformation, which is reversible and freezes at low temperature. If the forced high-elastic deformation is reheated, it will gradually disappear and return to the original state.
Typical formula for PTFE thermal shrinkable tube production:
Disperse PTFE resin 100 (weight)
Extruder 20 ~ 22
Production process:
PTFE resin, extrusion aid → mixing → storage → pre-molding → pushing and pressing → drying → sintering → cooling → heat treatment → blowing → cooling → product.
Production process parameters:
The front part is the same as ordinary PTFE tube.
Heat treatment: the quenching process of the dried and sintered pipes after further full sintering at high temperature, the temperature is 390 ℃±2 ℃, and the coolant is -5 ℃.
Blowing: at 310 ℃ or so, fill the compressed gas below 0198MPa, the blowing rate is 200% ~ 400%.
Main equipment: blowing machine, other PTFE tube and the same.
1.3 ptfe teflon steel wire reinforced hydraulic pipe
The common PTFE pipe will break under the pressure of about 40kg/ cm2. When it is combined with steel wire, the pressure resistance will be greatly improved. The maximum working pressure abroad reaches 700kg/ cm2.The results show that the compressive strength and pulse strength of the hose are related not only to the steel wire strength but also to the weaving Angle.When the braiding Angle is 54°44 "for single-layer braiding, the steel wire does not extend under internal pressure, the length and diameter of the hose do not change, and the pressure resistance is the best.
When used as hose for hydraulic system in aviation industry, in order to prevent electrostatic breakdown of inner tube caused by hydraulic oil flow, trace conductive carbon black should be added in the manufacture of PTFE inner tube.However, it was found that adding carbon black could not completely prevent electrostatic discharge from passing through the tube wall and increase the gap.
In the 1960s, Attas manufactured composite tubes, in which the inner layer of the tubes was a uniform mixture of conductive carbon black and PTFE, and the outer layer of the tubes was pure PTFE.This form of tube body layer has axial conductivity, so it can not only eliminate static electricity, but also prevent seepage.
The process:
Inner resin (including conductive carbon black), outer resin → blank → pushing → drying → cooling → testing → weaving → fitting joints → testing.
PTFE steel wire composite hose is mainly used in aircraft hydraulic system, air conditioning system, fuel system, lubricating oil system.In civil industry, it is suitable for soft connection of hydraulic pressure, steam pressure and steam transportation in rubber, plastic, pharmacy, clothing, shipbuilding, automobile, machine tool, motor, diesel engine and paper making industries.
PTFE spiral tube, also known as PTFE flexible hose, has not only all the excellent properties of PTFE, but also flexible properties.At present, there are two kinds of PTFE spiral tube and chemical fiber, stainless steel wire and plastic coated glass fiber woven reinforcement.
It is made of PTFE through secondary processing. The process is that PTFE thin-walled tube continuously rotates forward through a combination mold with a temperature of 270 ℃ ~ 280 ℃ at a certain speed.
It is mainly used for the inlet and outlet pipes of the shock parts such as the soft connection dislocation connection, serpentine pipes, pump engines and so on.Used for shielding cable and protecting cable sleeve of aircraft engine.
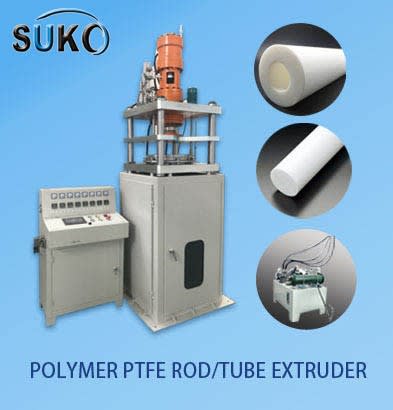
Keywords: PTFE, Ptfe tube, teflon, tube, ptfe pipe, machine, extrusion, extrusion machine, pushing, sintering, extruder